Complex challenge: building the minivan won't be easyComplex challenge: building the minivan won't be easy
For manufacturing managers, it's the stuff dreams are made of, but not the good kind. Superficially at least the manufacturing plan for General Motors Corp.'s new front-drive minivans sounds like a nightmare of complexity. Picture this:* In one assembly plant in Doraville, GA, GM hopes to build distinct versions of minivans for three U.S. marketing groups and GM of Europe; left- and right-hand drive,
April 1, 1996
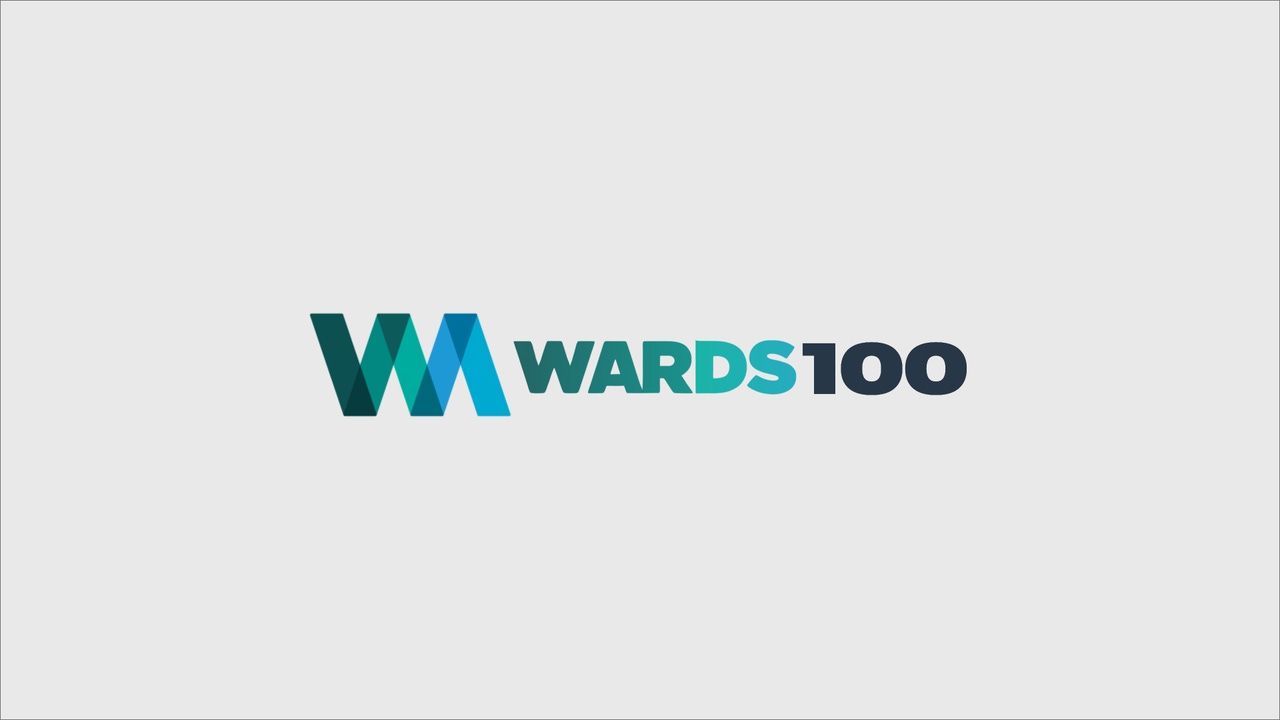
For manufacturing managers, it's the stuff dreams are made of, but not the good kind. Superficially at least the manufacturing plan for General Motors Corp.'s new front-drive minivans sounds like a nightmare of complexity. Picture this:
* In one assembly plant in Doraville, GA, GM hopes to build distinct versions of minivans for three U.S. marketing groups and GM of Europe; left- and right-hand drive, short- and long-wheelbase, four- and five-door models.
* Thanks to GM's global sourcing initiatives -- and serviceability needs for the Europe-bound vans -- parts are being shipped in from all over the world. Two -- and eventually three -- engines will be shipped in from overseas for installation in Opel models. Engines for U.S. versions are being imported from Mexico.
* All exhaust systems are coming from Belgium, taillamps are shipped in from England, alternators from France. There are 30 different fastener suppliers, many of them shipping directly from Europe.
* The new van has an aluminum hood. That's good news for consumers who will enjoy how easily it lifts, but to manufacturing engineers, aluminum body panels are a hassle on the factory floor. They usually require special handling to avoid dings.
Considering that GM is just recovering from the disastrous launch of the Chevrolet Cavalier/pontiac Sunfire in Lordstown, OH, which dragged on for six months, it would be easy to think GM once again has bitten off more than it can chew.
But Donald E. Hackworth, vice president and group executive of GM's Midsize and Luxury Car Group, says he is confident the apparent complexity of the project is under control and that the vehicle will be a sales and a manufacturing success.
However, he says production ramp-up will be very gradual, accelerating eventually to about 60-units per hour.
Richard A. Heithaus, minivan program manufacturing manager, also is confident of success:because the minivan team dealt with all the variables during the design phase and involved manufacturing engineers early, Mr. Heithaus there are fewer build combinations for the new minivan than for the old Cutlass built in Doraville.
That was accomplished, Mr. Heithaus says, by simplifying assembly operations and minimizing the number of parts, variations and options. For instance, Velcro and snap-fit attachments were used wherever possible in interior component assembly instead of more complicated fasteners, and an all-wheel-drive option was nixed.
Headliners on all versions of the vehicle are the same color. interior fabric and color choices for each minivan model also are limited in order to cut build complexity.
Mr. Heithaus did his homework, too. He studied what went wrong at Lordstown, as well as what went right, and says he was astonished at how much help and information he got from other GM organizations.
He also visited Ford plants and Toyota's facility in Georgetown, KY. For a better understanding of how to deal with parts and components delivered from overseas on container ships, he visited New United Motor Mfg. Inc. in California.
But Mr. Heithaus is particularly proud of the modular wire harness configurations GM engineers created for the new minivans.
Vehicles as varied as the new U-van family typically would require dozens of different wire harness configurations to accommodate widely varying options and equipment. However, Mr. Heithaus says GM engineers analyzed all the possible configurations and were able to develop a small number of "jumper" harnesses that could be color-coded and mixed and matched to take the place of a far greater number of conventional harnesses.
GM is spending $250 million to refurbish the Doraville plant for minivan production, and a $110 million contiguous stamping plant will be finished in 1998.
GM officials are vague about when the plant will hit capacity. They say production launch will be slow to ensure quality.
Equipped with almost 500 robots, the new Doraville facility is part of a new generation of highly flexible GM plants that win be capable of building a wide variety of products to accommodate shifting marketplace demands. If van sales are disappointing, cars could easily be built on the same line, says Mr. Heithaus.
Read more about:
1996About the Author
You May Also Like