GM Battery Lab Now Testing Cells, Packs, Potential Suppliers
“Understanding cell chemistries is the key to becoming a smart cell buyer,” says Andrew Leutheuser, GM’s lead battery-systems engineer.
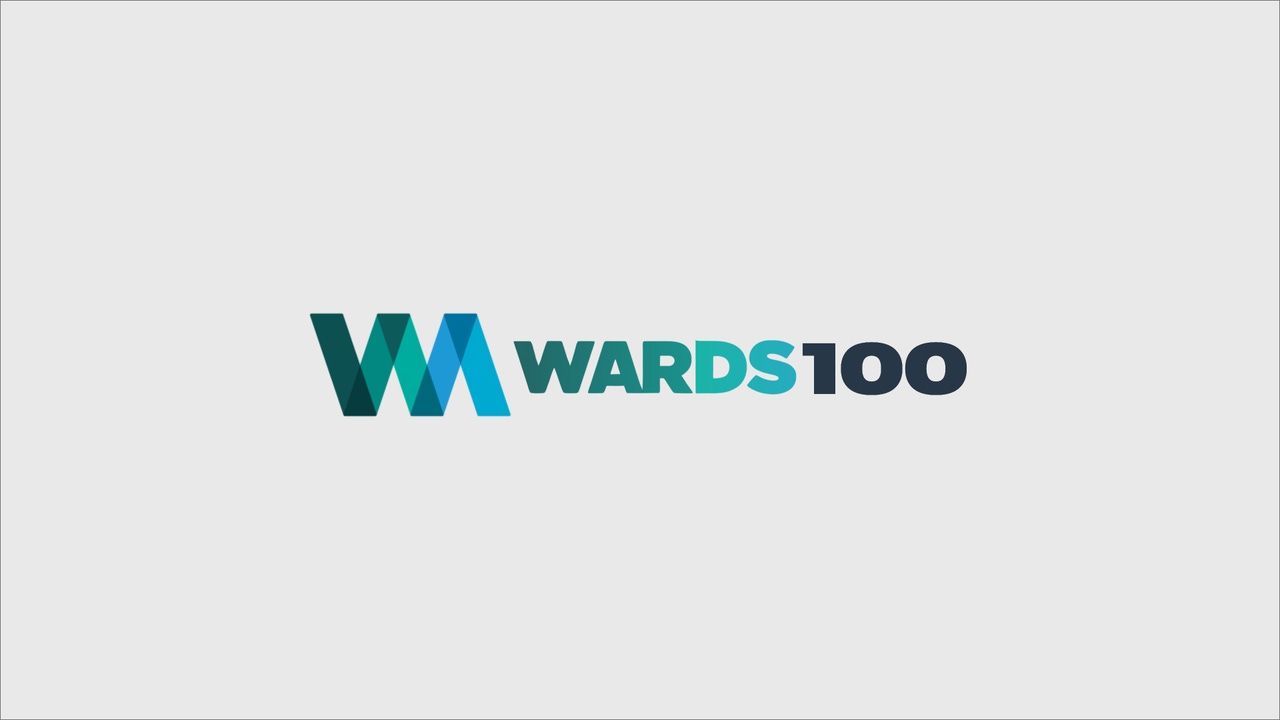
WARREN, MI – General Motors Co. offers a first peek inside its new battery lab, where the auto maker simultaneously tests cells and packs for upcoming extended-range and hybrid-electric vehicles, including the ’11 Chevrolet Volt.
GM cut the ribbon on the $25 million facility in June, with President and CEO Fritz Henderson joined by a group of federal, state and local politicians. Tax breaks played a big role in GM choosing a site here on the campus of its research and development complex.
The lab includes about 170 test chambers cycling battery charges up and down 24 hours a day, 365 days a year. During the cycling, engineers introduce severe temperature and humidity levels, while an automotive OEM-exclusive “shaker table” adds vibration to the testing mix.
Roughly two-thirds of the chambers currently are testing lithium-ion battery cells and packs for the Chevy Volt, while the rest test cells and packs for GM’s plug-in HEV technology and next-generation mild-hybrid system.
The lab gets its own power substation on the campus, but GM returns back to the grid an estimated 90% of the power it draws. If every cycler in the lab were to charge a battery simultaneously, it would pull an amazing 6 megawatts from the grid.
The lab generates 40 gigabytes of data daily, says Joe LoGrasso, manager-Global Battery Systems Engineering. “We’re generating a lot of data storage requirements,” he grins.
GM divides the lab into two parts: a cell- and module-testing area and a pack-testing area. Ironically, the auto maker uses old engine-testing rooms, built some 50 years ago with thick concrete walls and high-strength glass to withstand blasts from blown engines, because batteries can be just as volatile.
The 33,000-sq.-ft. (3,065-sq.-m) lab is located in a building that originally served as the home for Chevrolet advanced engineering, where for many years some of the industry’s most advanced powertrain work took place.
GM engineer Jack Laerzio tests a lithium-ion battery cell inside auto maker’s new lab in Warren, MI.
For many engineers, working on Chevy powertrains in the building marked the height of a career, says Ronn Jameison, director-Global Battery Systems Engineering.
“If you worked here, you’d made it,” he says, walking halls with fresh paint, trendy new LED lighting and flooring made from recycled tires.
But now that distinction belongs more to electrical, chemical and materials engineers than the old-fashioned mechanical types. The lab employs about 150 battery experts.
Reflecting the growth in electric propulsion, as well as GM’s emphasis on making battery power a core engineering competency, the auto maker’s battery teams numbered just 30 people three years ago. In addition to testing cells and packs, the lab scrutinizes various battery chemistries from suppliers. GM wants to be a battery expert, but it does not want be in the business of mixing chemistries or making cells.
For example, Li-ion, which GM considers its battery of choice going forward, can be made using as many as 25 different chemistries. And each chemistry yields different power and energy properties. Some GM products such as HEVs require more power, while EV applications such as the Volt demand more energy.
“Understanding cell chemistries is the key to becoming a smart cell buyer,” says Andrew Leutheuser, GM’s lead battery-systems engineer.
“We have to have a number of batteries ready for a number of applications,” he says.
When evaluating a battery supplier, GM looks for those with volume-manufacturing experience; a keen understanding of battery life; and knowledge of battery failure modes and abuse tolerance.
It also wants suppliers that operate transparently, have close relationships with raw-materials providers and possess a deep understanding of materials, design strategies and production processes both for today’s batteries and those yet to come.
Chemistry evaluation starts on paper before candidates are whittled down for a round of lab testing, followed by cell and pack qualification.
Troy-based Compact Power Inc., a division of South Korea’s LG Chem Ltd., won GM’s first battery-supply contract for the Volt. CPI will provide cells to GM, which will perform its own pack-assembly work at a manufacturing site in Brownstown Twp. south of Detroit beginning later this year.
CPI will supply GM with battery packs for Volt prototypes and perhaps even pre-production models until the Brownstown Twp. facility is fully operational early next year.
LG Chem and CPI also will supply GM’s PHEV program, which, following the shutdown of the auto maker’s Saturn brand and a more recent decision to kill a Buick cross/utility vehicle using the technology, still is looking for a home.
GM engineers do not reveal during the lab tour which product will get the PHEV technology, which remains on track for a 2010 rollout, but suggest a decision may have been made.
Japan’s Hitachi Ltd. has won the contract to supply batteries to GM’s next-generation mild-hybrid system. Known as BAS+, the belt alternator/starter system is designed to be compatible with any GM vehicle and powertrain around the world – from gasoline to diesel and 4-cyl. to V-8.
The current BAS system is available only on 4-cyl. Chevy Malibu and Saturn Aura midsize sedans, and it is larger and less efficient than BAS+.
Although GM considers Li-on ripe for full commercialization, as evidenced by product programs with the technology quickly nearing launch mode, issues surrounding lifecycle duration, recycling and workforce expertise still require development.
Cost remains the No.1 obstacle for Li-ion, but GM sees that softening in the coming years.
Speaking at a plug-in technology conference in Detroit earlier this week, Jonathan J. Lauckner, vice president-global program management, says the much-scrutinized cost of the Volt’s 16-kilowatt-hour battery pack could be “many hundreds of dollars less” than the $1,000 per kWh many experts have anticipated.
Looking further down the road, GM estimates batteries found in applications such as the Volt could shrink to between $300 and $500 per kWh by 2015.
“It’s volume; it’s materials; it’s optimization,” Leutheuser says, adding localized cell production to the list of ways to lower Li-ion battery costs. To get the Volt battery down to $500 per kWh, he says “it would take the higher range of production volumes.”
GM anticipates building roughly 10,000 Volts during its first full year of production in 2011, stretching that number to 60,000 in its second year, Vice Chairman Bob Lutz has said.
Volt battery costs could shrink to as little as $200 per kWh by 2020, GM estimates. Lauckner thinks $250 per kWh would make plug-ins competitive with conventional vehicles.
About the Author
You May Also Like