GM Looks to Global Manufacturing to Stay Competitive
Every GM plant in the world will have a "Common Bill of Processes" to assure all vehicles with the same architecture will follow the same manufacturing sequence.
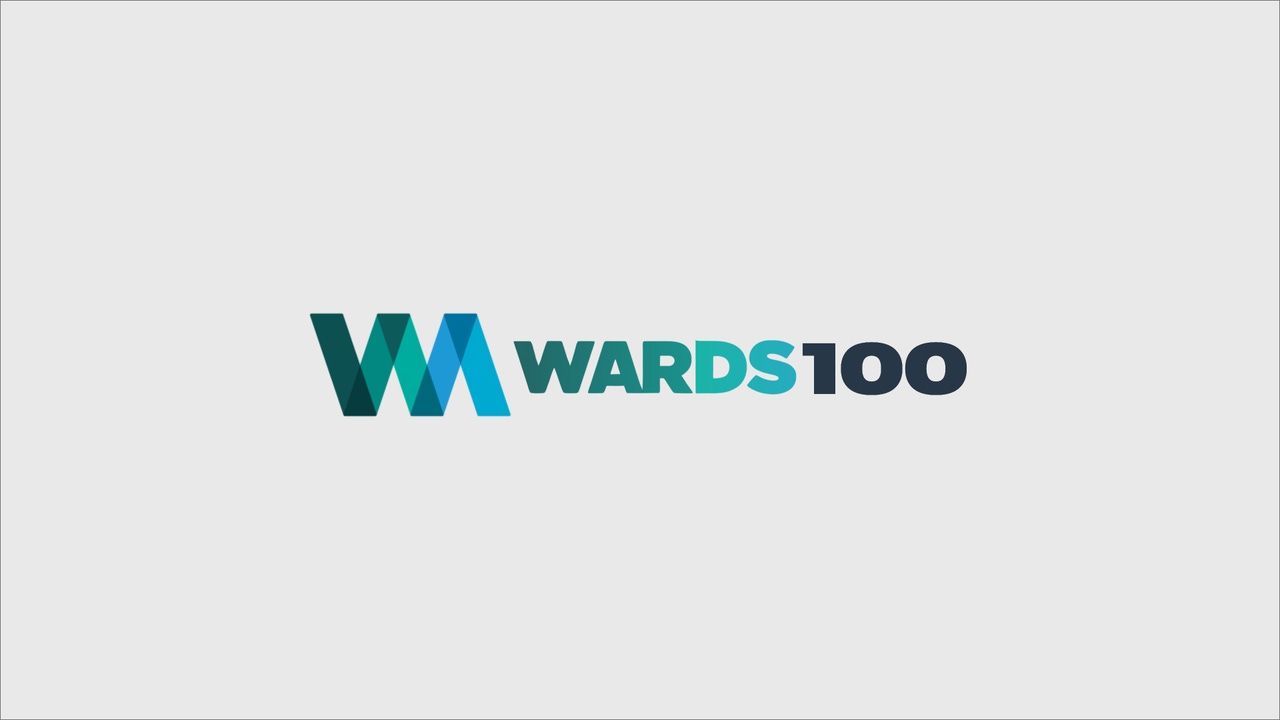
TRAVERSE CITY, MI – Having a global eye for processes as well as products will enable General Motors Corp. to be leaner and more agile, says one of the auto maker's key manufacturing executives at the Management Briefing Seminars here.
Mary Barra, executive director-global manufacturing engineering since July 2004, says growing globalization at GM is a sign the auto maker is addressing its long-term challenges as well as its short-term crisis of declining sales.
As an example, she points to the forthcoming next-generation global midsize vehicle architecture (formerly called Epsilon) that will be used for high-volume cars such as the Opel Vectra, Buick LaCrosse, Chevrolet Malibu and Saab 9-3, among others. The original Epsilon platform it replaces morphed into three different regional architectures. The resulting economies of scale of the single new platform will reduce component costs significantly and total investment will be 30% less than for current Epsilon derivatives.
GM's plant in Russelsheim, Germany, will make seven different cars on the new platform, including hatchbacks, convertibles, sedans and station wagons.
The auto maker's manufacturing operations are becoming more efficient due to the global view the product platform represents, Barra says.
Mary Barra
Every GM plant in the world will have a "Common Bill of Processes" to assure all vehicles with the same architecture follow the same manufacturing sequence. Common locator holes and tolerances will allow workers to build variants of vehicles in the same plant without affecting the vehicle's design.
In addition, GM is launching a "Global Dimensional Information System" to replace regional programs that differ from one another, Barra says.
Although all GM plants will follow the same sequences, automation will vary. Barra says a "Common Bill of Equipment" will allow managers to use labor rates and other costs to decide which operations should be automated and which could be handled by workers.
Read more about:
2006About the Author
You May Also Like