GM Prepared for Market Rebound
By 2015, more than 50% of production will come out of a network of flexible assembly plants, the auto maker says.
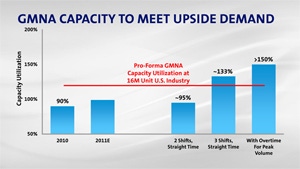
General Motors’ manufacturing operations won’t be caught off-guard should the U.S. market rebound from today’s stagnant sales pace to pre-recession levels of 16 million-plus units a year, says a top executive.
Diana Tremblay, global chief manufacturing officer, says despite taking out 1.5 million units of North American capacity post-bankruptcy, GM has several tricks up its sleeve to keep pace should the market make a comeback.
<link rel=
">
Speaking during GM’s Second Annual Global Business Conference for financial analysts, Tremblay says the auto maker’s North American manufacturing capacity utilization should close in on 100% by the end of this year.
But as demand increases further, third shifts could be added across the board to push plant utilization rates as high as 133%.
“At that point, we could respond to a 16 million-unit market,” she says, noting overtime could push utilization even further, to 150%.
Keeping up with expected increased demand in developing countries, especially Brazil, Russia, India and China, is something the auto maker also is preparing for, she says. “The growth we’re going to have, 80% of it is going to be in low-cost countries.”
Cutting the number of architectures underpinning GM’s global lineup by 50% will allow GM to keep up with demand and bring products to market quicker, she says.
The ability to build multiple vehicles at one plant also is essential, Tremblay says, noting by 2015 more than 50% of production will come out of a network of flexible assembly plants.
GM has made substantial quality improvements but is not where it needs to be, she says.
“We’re asking (workers) what could go wrong (during assembly) and putting in processes and systems to make sure (it doesn’t happen),” Tremblay says, citing the upcoming Chevrolet Sonic compact as an example.
Workers pointed out there were 14 different bolts used to install the transmission, increasing the potential for error. “We made changes so we have only two bolts,” she says. “It’s a better way to build quality.”
While its Tremblay’s job to ensure GM is able to quickly react to changing market conditions, preparing the supply base is the responsibility of Bob Socia, vice president-global purchasing and supply chain.
Socia says the March 11 earthquake and tsunami in Japan highlighted some shortcomings in industry-wide global supply logistics.
“I think it’s fair to say the industry’s management of the supply base was lacking. That’s where we’re putting the effort,” he says. “Not that we want to control the entire supply chain, but we want to understand (it). And we want to make sure our risk profile around the world is as solid as can be.”
GM managed its response following the Japan disaster by working “24/7 for three months,” he says. “Within 24 hours we assembled a cross-functional team, developed a plan, optimized schedules, developed alternatives and worked with suppliers to get up and running.”
“I believe we built trust and a new level of partnership internally and with many suppliers,” Socia adds. “It got us through the most challenging time with no material impact.”
He says GM already is dual-sourcing key parts and “will continue that as part of a solution.”
The overall health of the supply base “is pretty good,” Socia says. “I thought we’d have a lot more trouble than we experienced coming out of bankruptcy.”
He says there were 150 financially troubled GM suppliers when it exited bankruptcy. Today there are fewer than 40.
The auto maker’s once-frayed relations with its supply base also are on the mend, Socia says, in part because GM is making fewer running changes to its product-development and production plans.
“If you source business and go back and change volume, mix or the manufacturing footprint, it’s not an easy conversation to have (with suppliers), particularly if the supplier already made an investment.”
It also cost GM money.
“Every time we’d go back to a supplier and say (the program has) changed, they’d take money out of our pocket,” notes Chief Financial Officer Dan Ammann.
Read more about:
2011About the Author
You May Also Like