GM Sees Building, Design Future in 3DGM Sees Building, Design Future in 3D
GM estimates using 3D technology saved 5%-8% in costs for its recently completed Lansing Delta plant.
June 30, 2006
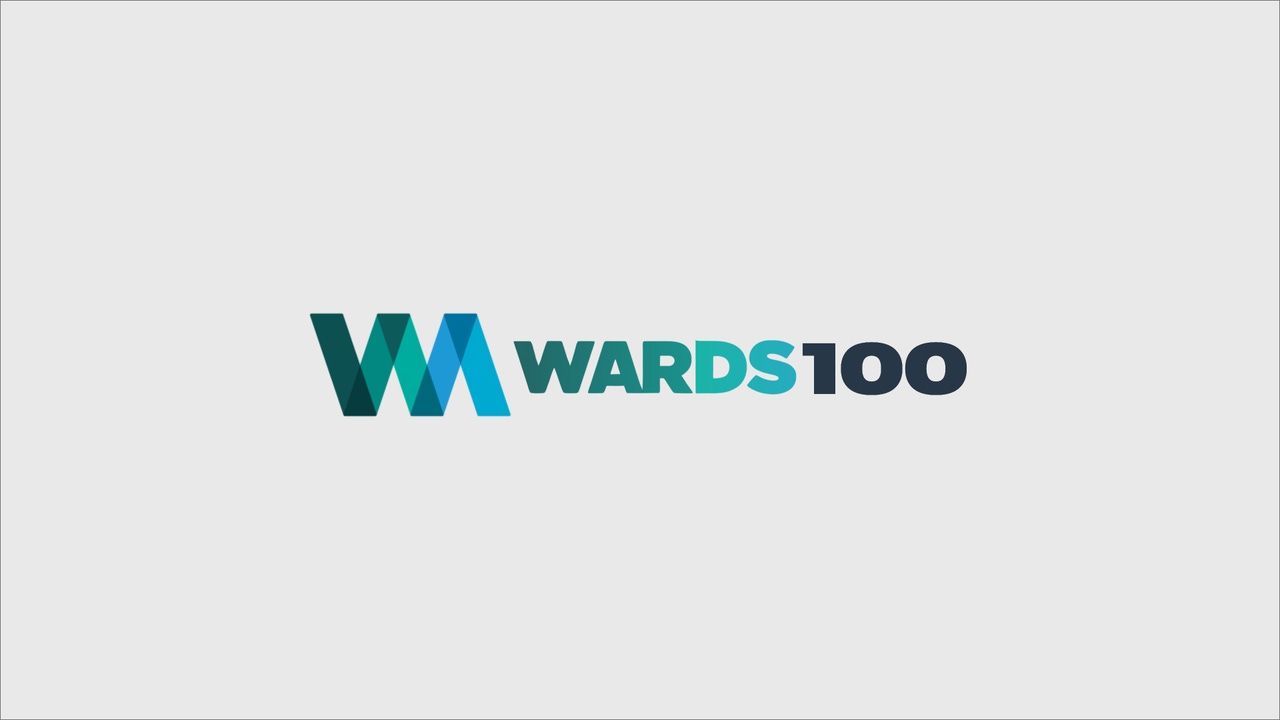
WARREN, MI – With its newly opened Lansing (MI) Delta assembly plant as the prototype, General Motors Corp. is embracing 3-dimensional facilities design as a critical cost-cutting, time-saving tool.
Company executives and a host of contractors and architects that worked on the design and construction of the plant are touting 3D technology – which has come a long way from the drive-in monster movies of yesterday – as the way of the future.
GM says it is the first auto maker to apply 3D capability on such a massive project.
“Now we’re convinced this is going to be a way of life,” Jim Wiemels, general manager-GM Manufacturing Engineering, says at an event here to showcase the technology.
Without releasing numbers, managers estimate 3D helped save 5%-8% in construction costs on the newly opened Lansing Delta Plant – a 2.4 million-sq.-ft. (222,967-sq.-m) facility that will manufacture the Saturn Outlook, GMC Acadia and Buick Enclave cross/utility vehicles. Job one for the first of the CUVs is slated for this fall.
It took 19 months to construct the CUV plant. That’s about 20% less time than anticipated and marks the fastest construction turnaround of a GM facility in the U.S.
The auto maker now expects all its North American architectural and construction contractors to adopt the 3D method, quickly becoming the industry standard. The imaging innovation currently is in use in expansions or other projects at six GM complexes.
GM is embracing 3D design to reduce construction costs and project time.
Dave Skiven, executive director-Worldwide Facilities Group, notes the auto maker is a bit of a “Johnny-come-lately” to 3D.
In fact, Skiven, who led construction of Saturn Corp.’s Spring Hill, TN, plant in the late 1980s, says 3D technology was available at the time. But it was used to wow his bosses with virtual tours of the facility and not as a pre-construction tool, Skiven says.
The new slogan in facilities design these days is “build to the model.”
“This is our mantra, this is the way we’re going to run our business,” he says.
GM operates 170 plants in 34 countries, and getting overseas contractors to use 3D may prove a short-term challenge, officials here say. But GM employs off-the-shelf software and computing tools to make 3D possible, and that should make the process easily adaptable, they say.
In recent years, 3D has evolved as the go-to technology for everything from validating production line operation to helping detect flaws and improve quality at GM plants. In virtual assembly rooms, or VARS, designers wear thick, heavy-duty goggles, compared with the traditional flimsy red and blue movie glasses, to bring the 3D animation to life.
With computer processing speeds several hundredfold that of 20 years ago and high-speed Internet now readily available, Skiven and others here expect most companies can and should be equipped to use 3D.
“We’re just scratching the surface,” says Jack Hallman, director-capital projects Worldwide Facilities Group. Hallman says GM soon will be using 4D technology, which adds the element of time and allows designers to better estimate timetables for complex construction projects.
GM also employed 3D for a brownfield expansion of its Flint (MI) Engine South facility, which makes the Vortec 4200 I-6 engine in Chevrolet TrailBlazers and GMC Envoys. The existing Flint Engine South plant is about 760,000 sq.-ft. (70,604 sq.-m) and was opened in 2000. Using virtual technology, another 442,000 sq.-ft. (41,062 sq.-m) was added in 2005.
This September, production of HFV6 engines will begin in the new section of the facility for the ’07 Enclave, Outlook and Acadia. The HFV6 also will be installed in Cadillac STS, SRX and CTS models produced at GM’s Lansing Grand River plant.
With the tool, thousands of interferences, or design conflicts, were eliminated between blueprints, as architects, contractors and suppliers gathered in one room to examine construction plans from every possible angle.
“At the end of the day, we could push a button and everything was updated in real time,” says Frank Venegas Jr., chairman and CEO of The Ideal Group Inc., a general contractor on the Flint project. Using 3D helped hold down “design creep,” common for large projects with multiple contractors and subcontractors.
“Ten (percent) to 15% of the cost of a job is in creep. And with this job, we basically eliminated that,” he says.
Troy Creed, an electrician working in general assembly at Lansing Delta, says the 3D simulations were so realistic, he reflexively ducked out of the way of a virtual pillar during one session.
Creed says he already has watched the plant operate at full capacity – in a virtual sense.
“I’m waiting now to see that in reality,” he says.
GM partnered with GHAFARI, Alberici Group, Ideal and Dee Cramer Inc. on the math-based technology.
GHAFARI was the main architectural firm on both the Lansing and Flint projects. Ideal was the main contractor for the Flint Engine South facility; and Alberici was the main contractor for Lansing Delta Township’s body shop, general assembly and central administration.
Dee Cramer Inc. was the lead contractor for the heating, ventilation and air conditioning systems at the plants.
About the Author
You May Also Like