Is This GM's Silver Bullet? UAW remains guarded about Yellowstone'sprospectsIs This GM's Silver Bullet? UAW remains guarded about Yellowstone'sprospects
Building profitable small cars is a challenge for everyone, but it is a task of heroic proportions for General Motors Corp., the least efficient mass-producer in the world.For decades it has struggled to implement elaborate - and expensive - manufacturing strategies to dramatically reduce labor and production costs. In the 1980s it spent billions on brand-new highly automated plants with the hope
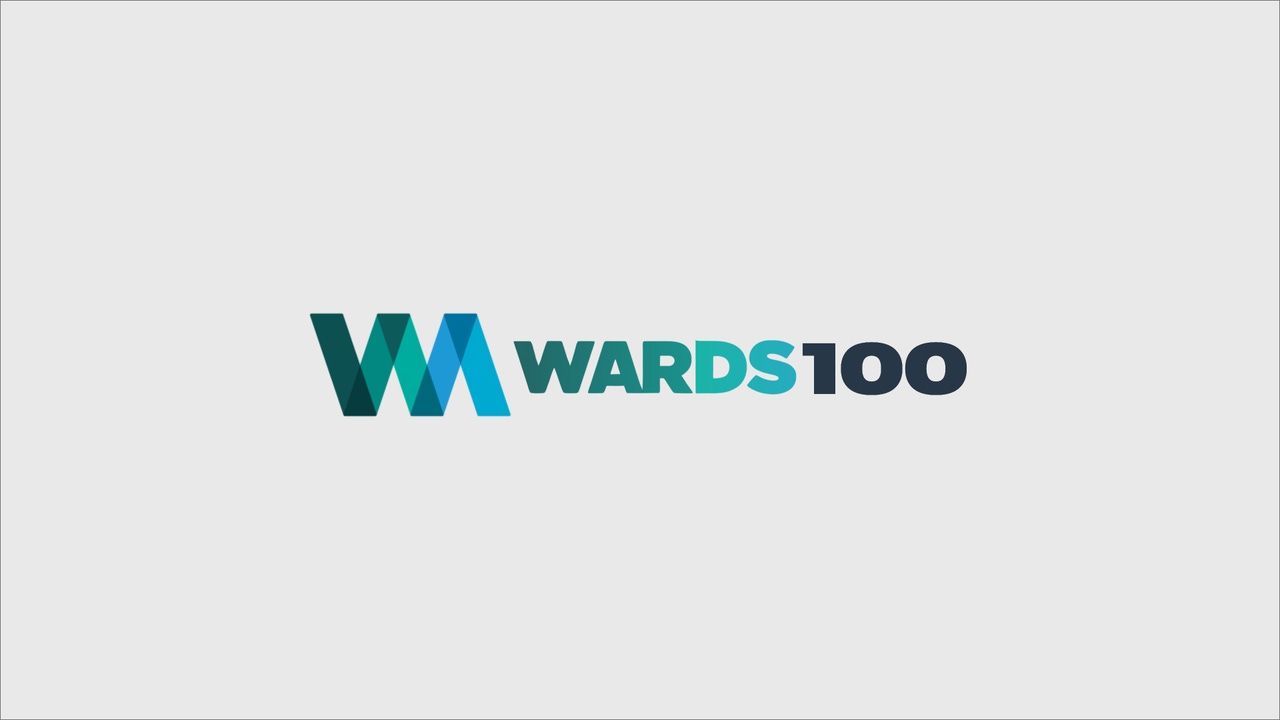
Building profitable small cars is a challenge for everyone, but it is a task of heroic proportions for General Motors Corp., the least efficient mass-producer in the world.
For decades it has struggled to implement elaborate - and expensive - manufacturing strategies to dramatically reduce labor and production costs. In the 1980s it spent billions on brand-new highly automated plants with the hope of supplanting high-cost labor with high-tech robots. The plan failed miserably. Its legacy: an apocryphal story about robots going berserk on the line and painting each other.
GM's ultimate small-car strategy - Saturn Corp. - has been a success by most accounts, but it came with a huge multi-billion dollar price tag. Furthermore, analysts give credit for most of Saturn's success to its innovative retailing and marketing rather than it's manufacturing technology.
When Saturn and GM's robot push began in the early 1980s, the goal was to compete with Japanese automakers that then enjoyed a reputed $2,000 cost advantage.
Now GM just wants to make a profit on every car. Mark Hogan, GM vice president and general manager-Small Car Group, says GM still loses about $1,000 on every small car it builds.
The newest strategy is a huge project called Yellowstone, formally unveiled in early January. It aims to replace aging small-car plants in areas such as Lansing, MI, and Lordstown, OH, with new greenfield plants and the latest modular assembly techniques to cut material and total factory costs by 20% and dramatically improve margins on finished vehicles.
The labor productivity target for Yellowstone is 100 vehicles per worker, per year. According to the Harbour Report, that would make Yellowstone factories among the most efficient small car plants in the world.
Not since GM unveiled its Saturn project in 1983 has such an ambitious project been proposed.
Within the next 60 days or so GM could begin breaking ground on up to three new plants to build a series of small vehicles in the U.S., says Mr. Hogan.
The project go-ahead and ground breaking decision await labor deals with the United Auto Workers union locals that represent employees at the Lordstown, OH and Lansing, MI, plants, which GM wants in hand by the end of March.
"We have been in close discussions with the UAW leadership and are engaged in a dialogue as to how we can make this work for our collective benefit. We plan to involve our unions in every phase of the process required to adapt our U.S. manufacturing network," Mr. Hogan says.
UAW President Stephen P. Yokich has not publicly opposed the project - which requires dramatic changes in union work rules and cuts assembly plant workers by about a third - but he hasn't given it a ringing endorsement, either.
"I'm concerned about a lot of things. If you don't have details of what's going on, you're concerned. And I don't know what's going on," Mr. Yokich tells reporters in early January. The union chief adds that he was "very surprised" he didn't have more details about Yellowstone.
Mr. Yokich tells reporters he plans to review Yellowstone with UAW Vice President Richard Shoemaker shortly. "I haven't been involved in any discussions, so I can't really tell you what's going on. And that's really the problem," he says.
Despite Mr. Yokich's current non-committal attitude, manufacturing analysts say the fact that he didn't reject the proposal outright is an extremely encouraging sign.
Mr. Hogan has made it clear the new strategy will rely on GM's growing retirement rate among hourly employees - not layoffs - to reduce the workforce.
And a possible carrot for the UAW will be the ability to organize supplier component assembly plants locating near the new greenfield facilities. Suppliers familiar with the plan privately say it has been made clear that their plants will have to accept the UAW if they want to participate in the program.
The Yellowstone project is so named "because it reflects our pride in America and is grounded in the spirit of adventure associated with this national treasure," says Mr. Hogan. It encompasses both the Delta and Epsilon car platforms. Delta, a global small-car platform, will be the first execution. Although small cars no longer are seen as an important segment in the U.S., they are crucial to automaker global strategies. GM's future small car portfolio will be 4 million units, half of its total global capacity.
Yellowstone is controversial because it is designed to have suppliers provide 15 built-up modules - including the interior cockpit, doors, headliner, seats and front and rear suspensions - to the final assembly plant.
Mr. Hogan says at least parts of the Yellowstone design and production philosophy will be involved at two or three new assembly plants: the Saturn facility in Spring Hill, TN, the GM-Suzuki Motor Corp. CAMI Automotive Inc. plant in Cambridge, Ont., GM's Ramos Arizpe, Mexico, facility and at least two Adam Opel AG plants in Europe.
It eventually would result in the closing of the current Lansing and Lordstown J-car plants, Mr. Hogan says.
GM already has sites picked out for the new plants, which would be located in a 50-mile (80-km) radius of Lordstown and Lansing. Each of the new facilities would be capable of building 215,000 to 220,000 vehicles annually on straight time and about 250,000 per year with overtime, he says. The plants, which also would incorporate contiguous stamping facilities for major panels, would be one-third the size and require one-third fewer workers than GM's conventional U.S. plants. They would run on either a three-shift or three-crew basis.
At least two brand new greenfield plants are being built because they only are expected to cost about $300 million, a fraction of the cost of a traditional GM assembly plant. "With roughly the same investment (for gutting an old "brownfield" facility) we can build a new manufacturing system with markedly improved operating cost, an ability to change products with the market, a lean material flow system and a quality focus centered around modern management techniques and employee involvement," Mr. Hogan says.
He won't say specifically how many models Yellowstone will spawn, but the program involves several derivatives of the Delta and Epsilon platforms. Delta will be used as the basis for replacements for the Chevrolet Cavalier, Pontiac Sunfire, current Saturns and Opel Astra. Epsilon will form the underpinnings for the Opel Vectra and Saturn LS. The programs involve several body styles and derivatives including crossover type car/truck hybrids, the GM executive says.
Key to the Yellowstone program, which resembles GM's "Blue Macaw" project under way in Brazil, will be the supplier parks planned for location near the final assembly plants. GM wants suppliers of the 15 key modules to locate in the parks. Including Tier II and Tier III firms, GM is hoping to have less than 100 suppliers involved in the Yellowstone project.
Plans are to have the new plants up and running within 30 months after the start of construction. Workers would move to the new Delta plants from Lordstown and Lansing, which would remain in operation until the new facilities are up to speed. Labor force reductions will be achieved solely through attrition, with no layoffs, Mr. Hogan says. "We're experiencing double-digit rates of retirements at those facilities anyway," he says. "We think we can do this without layoffs." The average age of the workers at Lordstown and Lansing is 47.
Mr. Hogan says he is optimistic about getting a deal with the union. "The GM board will not allow us to invest $1 billion in Delta unless we can make money," he says. "Yellowstone is the formula we've talked about for doing that. (The UAW) got a piece, the suppliers have got a piece and we've got a piece."
If GM can't reach local labor agreements with the UAW, it won't be able to build small cars in the U.S., Mr. Hogan says. If not, the automaker would have to rely on its foreign affiliates and partners for those vehicles, he adds.
If Yellowstone works, GM likely will apply the design and production formula to more up-market vehicles, Mr. Hogan says. "But we've got to be pragmatic with what the supply base can do and how we can apply (the concept) to brownfield plants. I'd characterize this as being pretty aggressive just to do three (new) plants this way," he says.
About the Authors
You May Also Like