Light Makes Might
General Motors Corp. is stepping up activity on aluminum and carbon fiber programs that should hit the market around mid-decade. The lightweight materials are becoming increasingly popular in the auto industry as manufacturers continue to strive to improve fuel economy and lower emissions by reducing vehicle mass, in addition to developing new powertrain technologies. The aluminum program involves
February 1, 2003
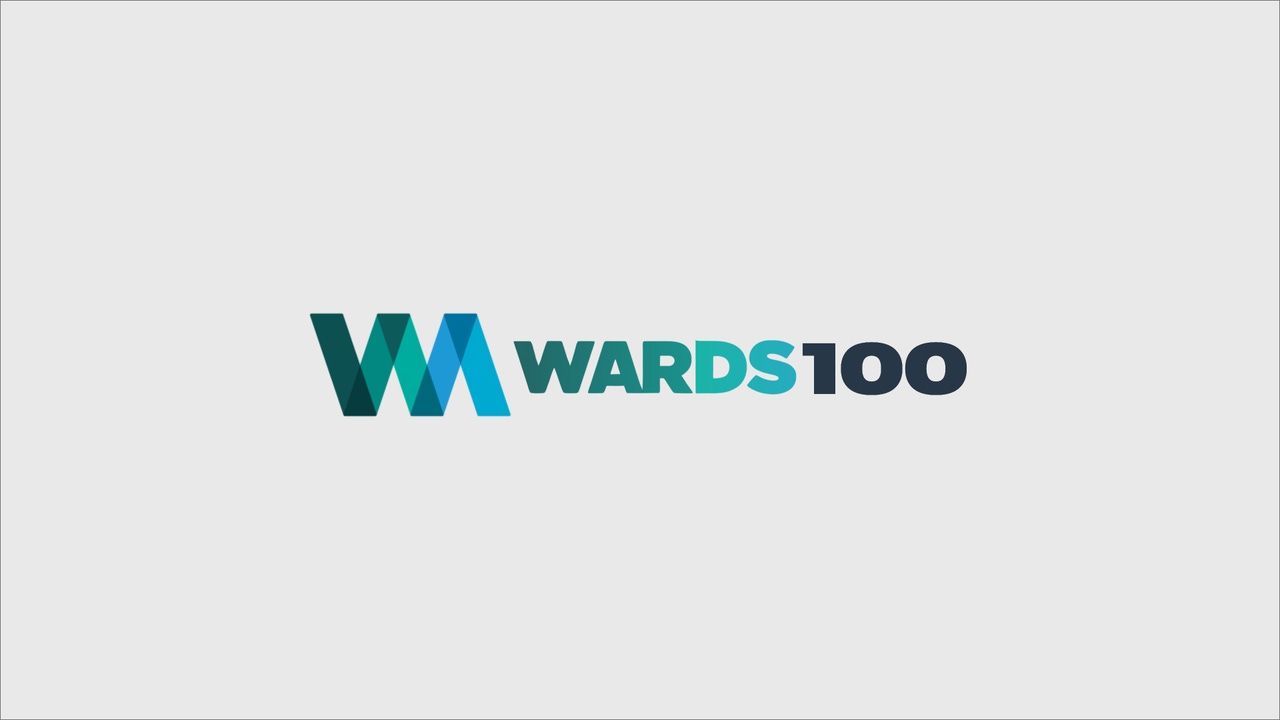
General Motors Corp. is stepping up activity on aluminum and carbon fiber programs that should hit the market around mid-decade.
The lightweight materials are becoming increasingly popular in the auto industry as manufacturers continue to strive to improve fuel economy and lower emissions by reducing vehicle mass, in addition to developing new powertrain technologies.
The aluminum program involves GM's Gen IV V-8 engines, due in 2006, and precision sand casting technology. The process will allow GM to cast an intricate aluminum engine block that is lightweight yet strong enough to withstand outputs between 350-450 hp.
Precision sand casting makes use of a low-pressure injection method instead of the traditional procedure, which relies on gravity — meaning aluminum is pumped into the mold rather than poured in. The improved technology reduces the porosity of the aluminum casting, which improves durability and, ultimately, customer satisfaction.
Ford Motor Co. has been using precision sand casting at its Brook Park, OH, plant since 2000 for the 2.3L 4-cyl. engine that powers the Ford Ranger and Mazda6. The process also is used by other industries to make products such as telephone bodies and aircraft. GM will spend $80 million to shoehorn precision sand casting technology into its Saginaw, MI, Metal Casting Operations (SMCO), a facility more than 80 years old that already is jam-packed with lost foam and green sand casting process technologies.
SMCO Plant Manager Rick Sutton anticipates eventually producing 1,500 to 2,000 Gen IV block castings daily. Plans called for prototype engine blocks to be built during the first quarter of this year.
Meanwhile, GM appears nearly ready to join the auto industry's growing fascination with carbon fiber. Dave Hill, GM vehicle line executive-performance cars, says the auto maker has completed research and development work and is preparing to put a carbon fiber program into production. “It's not something you can take to the bank,” Hill tells Ward's. “We don't know when we'll be able to do it, but hopefully it will be quite soon.”
Hill declines to provide a timeline, or specify on which vehicle a carbon fiber application may appear. “We've committed a lot of money to this project,” he says.
“And we will put it into production if we can get the quality and throughput that we benchmarked. So it's not research and development. It's ‘productionizing’ a technology.”
Prime candidates for GM's carbon fiber program likely would be vehicles that emphasize high performance and luxury, such as Chevy Corvette and Cadillac XLR. Hill concedes carbon fiber probably will appear first in GM “premium products.”
Carbon fiber-reinforced plastic interests auto makers because it's extremely tough, and it's 50% lighter than non-optimized steel and 30% lighter than aluminum. The material is made by heating synthetic fibers, such as rayon, until charred.
However, carbon fiber's historic problem has been its outlandish price. At one point, it cost well over $100 per lb. (0.45 kg) vs. 40 cents per lb. for traditional steel. That's why so many carbon fiber projects have crumbled. In 1979, Ford showed off an LTD sedan made almost entirely from carbon fiber composites.
GM debuted a carbon fiber-intensive prototype in the early 1990s. Both projects went nowhere because of cost issues. Ford also experimented with carbon fiber driveshafts on its Aerostar minivan in the 1980s, and Toyota Motor Corp. adopted the material for the driveshaft on its Mark II in 1992. Toyota went back to steel four years later.
However, cost is decreasing. Prices are falling toward a somewhat reasonable $5 to $10 per lb., and the allure of establishing a reputation for being technically advanced and environmentally responsible is growing. BMW AG, Chrysler Group and Ford's Aston Martin Lagonda Ltd. have carbon fiber projects under way.
Read more about:
2003About the Author
You May Also Like