Nano Growth
Although General Motors Corp. and North America, in general, have highlighted the development of nanocomposites for automotive applications, the European industry is hoping to catch up with an emphasis on nanotubes of carbon and silicon.
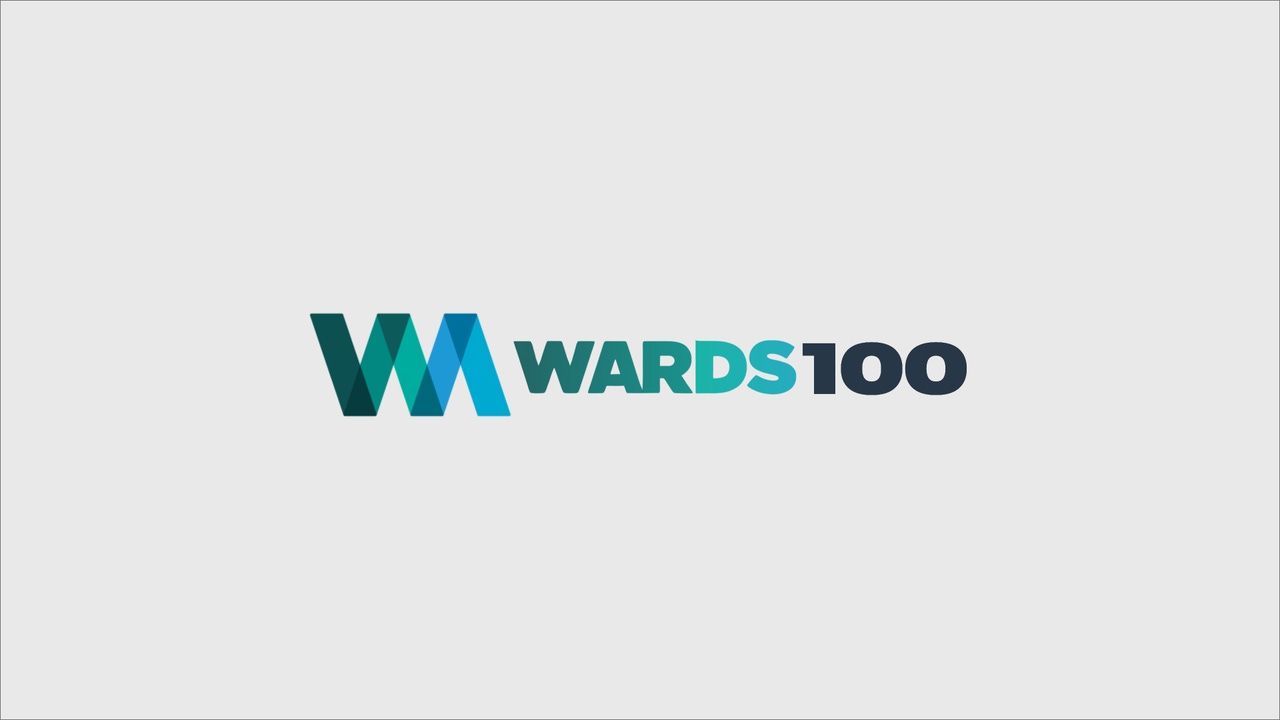
Although General Motors Corp. and North America, in general, have highlighted the development of nanocomposites for automotive applications, the European industry is hoping to catch up with an emphasis on nanotubes of carbon and silicon.
Tiny carbon molecules measured in nanometers — billionths of a meter — not only strengthen plastic parts; they allow them to conduct electricity, which opens a host of applications for high-volume body panels.
“Putting 1% of nanocarbon in a fender adds 9% rigidity and improves the electrical charge, which helps in the paint shop,” says Thibaud Vaugien, composite material manager for French composites maker Nanoledge. “Mercedes-Benz and Renault are testing it now.”
And at Menzolit-Fibron GmbH, which makes the sheet molding composite (SMC) material for the Volkswagen Eos trunk lid and Aston Martin DB9 fenders, “we are looking at nanocomposites for improvements to the surface quality of the SMC,” says Peter Stachel, director-marketing, research and development.
Until now, nanocomposites have been concentrated in low-volume applications in North America.
Working with Basell Advanced Polyolefins (Thailand) Co. Ltd., Southern Clay Products Inc. and Blackhawk Automotive Plastics Inc., GM added tiny spheres of clay to a thermoplastic olefin resin in 2001 to make the assist step for the '02 Chevrolet Astro and GMC Safari vans.
Since then, the auto maker has used it in other low-volume applications: stepside body panels in compact pickups, structural pieces in the Hummer H2 SUT and the center console in the Chevrolet HHR, where its scratch-resistance qualities are being evaluated.
Getting nanocarbon in fenders of a high-volume vehicle such as the Renault Megane, produced at a rate of nearly 800,000 units annually, would add enormous volume to the nanocomposite industry.
Arkema, a French industrial chemical company, last January opened a production line with capacity of 11 tons (10 t) annually, and it envisions expanding to 110 tons (100 t) in the future.
“We hope to be there in three or four years,” Jean-Marc Corpart, director-new business development, says.
“It depends on the speed of development of the market.”
Silicon particles in nano sizes present other opportunities, as well.
Nanoclay molecules are spherical, while nanosilicon particles are like little wires that hook together, says Stephan Sprenger, business unit manager-adhesives and composites at Germany's Nanoresins AG, noting the company made 110 tons (100 t) of nanosilicon material in 2005.
Nanoclay is good for thermoplastics, he says, but nanosilicon is better for thermoset materials, such as SMC-based body panels.
BMW AG is working on a roof module for the M6 sports car, in which nanosilicon is added to the resin to reduce the dimensional change in the part, allowing a design with reduced tolerances.
“It's also a good bet for adhesives,” Sprenger adds, “because it permits curing at room temperature instead of in an oven, saving considerable processing cost.”
Because silicon is transparent, it also works well in glazing and clear-coat finishes.
Porsche AG uses it in an acrylic coating to reduce scratching on a polycarbonate back window.
In addition, nanoparticles strengthen a resin by dispersing the forces that try to crack it, says Jan Bossaerts, an engineer at Hexion Specialty Chemicals in Belgium.
“A crack will develop in a material, and all the pressure is at the point of the crack,” he says.
“In steel, if you drill a hole at the point of a crack, the pressure is now dispersed around the circumference of the hole and the crack stops,” he says. “In a plastic material, the nanoparticles at the point of the potential crack are large enough to disperse the pressure.”
Although the auto industry and its composite suppliers are developing projects, “it's early days for nanocomposites,” Bossaerts says.
In industries such as sporting goods, nanocomposites already are in series production.
But for the auto industry, cost is a big issue, and costs still are falling.
“A few years ago, carbon nanotubes cost €60 per gram ($79 per 0.04 oz.),” says Nanoledge's Vaugien.
“Now it is €150 per kilogram ($197 per 2.2 lbs.).”
Arkema's Corpart expects its price to drop to about €100 ($132) per kilogram when volume reaches 110 tons (100 t) annually.
Nanosilicon, in comparison, costs about €40 ($53) per kilogram, Sprenger says.
In the short-term, a higher-performance material can be used to make a component thinner, which lowers weight and compensates for at least some of the higher material cost.
The longer-term view, however, includes new applications with new materials.
“Particularly when added to fibers, nanocarbon gives added functionality,” says Ata Yoosefinesai, who heads the Nanoforce technology transfer operation at London's Queen Mary University.
“Imagine conductive fibers in the fabric to heat seats,” he says.
Nanocalcium, Yoosefinesai adds, has different properties than the talc already used as filler in thermoplastics.
“It adds resistance to heat, so think of instrument panels exposed to the sun (and the heat absorption that could be eliminated),” he says.
“It (nanocalcium) also improves the flow of polypropylene (during production), which leads to simpler tools with fewer injection points, thus, reducing cost.”
About the Author
You May Also Like