New Vision
American Axle & Mfg. was formed in 1994 from a collection of castoff plants that General Motors Corp. no longer wanted. GM viewed the core business of truck axles as a low-tech, commodity-type sector and was glad 10 years ago to find outside investors, led by company founder Richard E. Dauch. But Dauch didn't see the axle business as low-brow, and the company's new $49 million tech center in Rochester
January 1, 2004
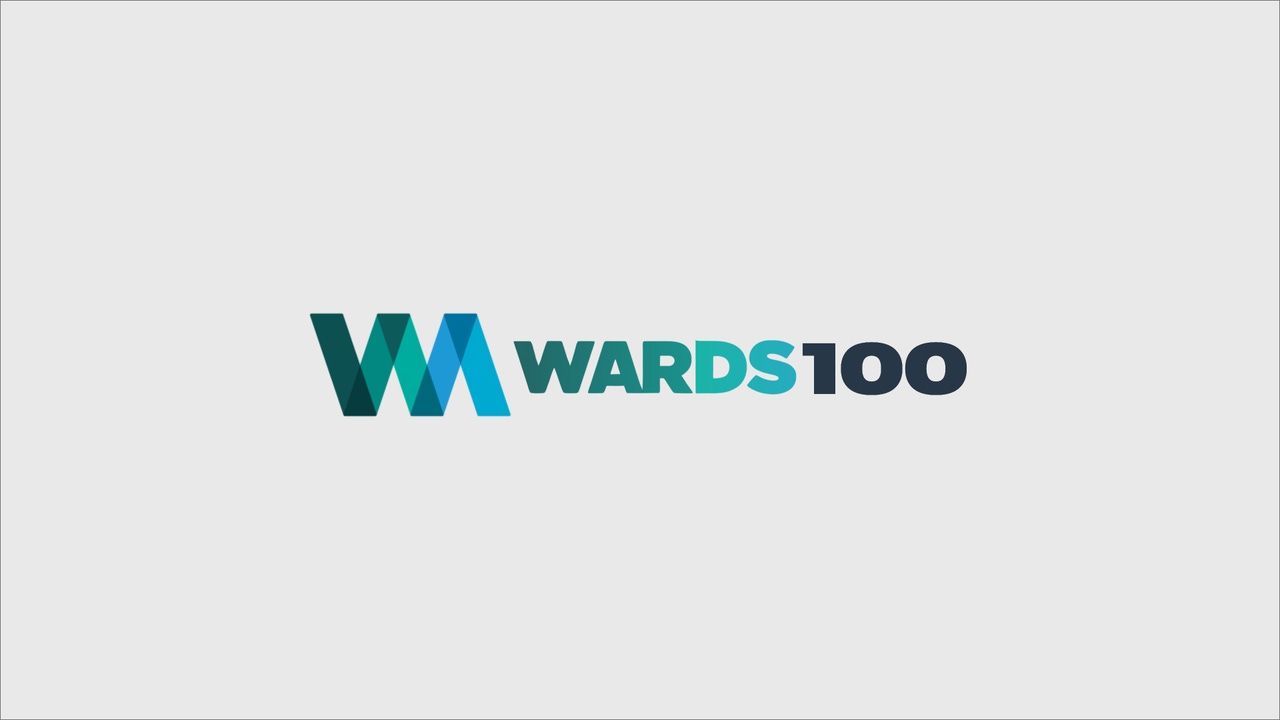
American Axle & Mfg. was formed in 1994 from a collection of castoff plants that General Motors Corp. no longer wanted.
GM viewed the core business of truck axles as a low-tech, commodity-type sector and was glad 10 years ago to find outside investors, led by company founder Richard E. Dauch.
But Dauch didn't see the axle business as low-brow, and the company's new $49 million tech center in Rochester Hills, MI, is a testament to that vision.
This second addition to AAM's 8-year-old facility — 37,000 sq.-ft. (3,437 sq.-m) that will be used to house a full-vehicle road-load simulator among other test equipment — will bring the lab to 120,000 sq.-ft. (11,148 sq.-m) and max out available space when fully completed in 2005.
The $12 million investment is a key piece of AAM's plan to move its product portfolio toward higher-tech components and into the cross/utility vehicle market.
“We've increased research and development funding 10% in dollars every year,” says Chairman and CEO Dauch, who has turned AAM into one of the industry's top-performing and fastest-growing suppliers.
After some initial lean years, Dauch says R&D spending has totaled about $300 million since 1994. New-technology-related sales, which made up 3% of AAM business when the company was formed, now account for 80% of revenues, Dauch says.
The expanded R&D center is seen as taking AAM to the next step as it looks to add electronics capability for a broader customer base both in North America and overseas.
The expansion is centered on development of several new products due for market by 2005, including a variety of all-wheel-drive power-takeoff units (PTUs) aimed at CUVs, plus AAM's new TracRite traction-enhancing differential, SmartBar automatically adjusting stabilizer bar and I-Ride independent rear-suspension module.
I-Ride was featured on two GM concepts, the Cheyenne pickup and Cadillac Sixteen supercar, and will get its first high-volume application on GM's next-generation '06 fullsize pickups and SUVs (GMT900 program) due in 2005 and expected to run through the '14 model year.
AAM can supply I-Ride in a modular form that can be installed with as few as four bolts. It is designed to work with platforms initially designed for a solid axle. That means I-Ride can be offered as an optional upgrade on some truck models or can be used as standard on higher-line versions of trucks that share platforms with lower-priced models. I-Ride also is being developed for CUV applications.
The supplier says it already has an application for its TracRite differential and SmartBar stabilizer on an upcoming niche vehicle. TracRite distributes power to the wheel or wheels with the most traction to ensure solid footing. SmartBar electronically controls the amount of vertical wheel travel, allowing a wide range under offroad conditions but minimizing travel on the highway for a better, safer ride.
AAM has relied on the light-truck market for its survival and growth but is looking to branch out into the unibody sector with a full line of new PTUs designed to work with most vehicle platforms and AWD configurations on the market. Officials won't say, but indications are one of its first applications will involve a small GM CUV in Brazil.
Once the expansion's fully operational in 2005, AAM's tech center will employ some 270 people. It operates seven days per week and does everything from rapid prototyping to extensive durability and fatigue testing on machines that can be programmed to duplicate an auto maker's own proving grounds test cycle. The lab can replicate the equivalent of six to eight months' track testing in one to three weeks.
The center also houses an anechoic chamber for noise, vibration and harshness testing, a $1.8-million materials analysis lab complete with an electron microscope and the new state-of-the-art road load simulator that can test complete vehicles up to 13,000 lbs. (5,897 kg) gross vehicle weight.
AAM says it now has a leading 36% share of the North American driveline market. About 72% of its business is axle-related. It produces 19,000 axles per day, some 35% of which are for 4- and all-wheel-drive vehicles.
Currently, about 85% of AAM's $3.5 billion business is focused on GM, down from 98% prior to the spin-off. Dauch's goal is to take that to 60% over the next five years.
Read more about:
2004About the Author
You May Also Like