Picking Up the Pieces GM management takes initiative, but no plant closingsPicking Up the Pieces GM management takes initiative, but no plant closings
Freeing Delphi Automotive Systems, slashing 10% of the jobs in its unwieldy marketing bureaucracy and building new assembly plants to replace older ones are Chairman John F. (Jack) Smith Jr.'s first gambits to reinvigorate General Motors Corp. in the wake of its $2 billion bloodletting with the United Auto Workers union.Both sides are picking up the pieces. GM will schedule heavy overtime through
September 1, 1998
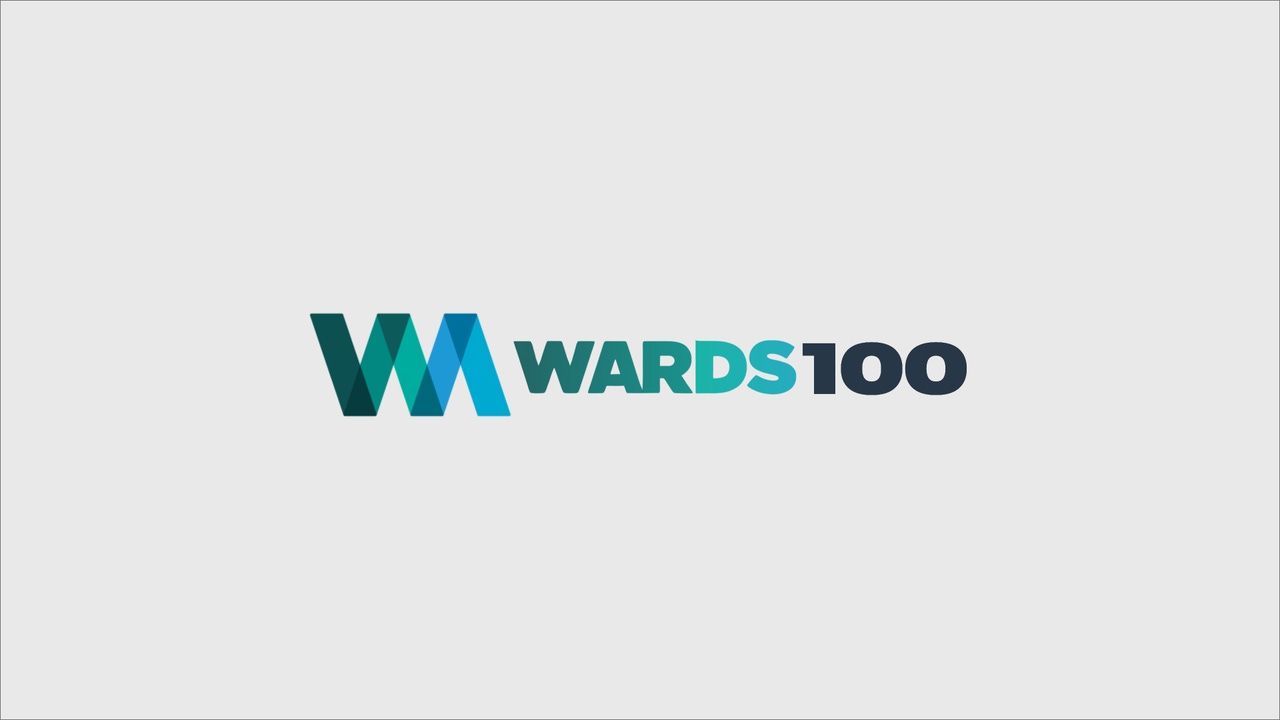
Freeing Delphi Automotive Systems, slashing 10% of the jobs in its unwieldy marketing bureaucracy and building new assembly plants to replace older ones are Chairman John F. (Jack) Smith Jr.'s first gambits to reinvigorate General Motors Corp. in the wake of its $2 billion bloodletting with the United Auto Workers union.
Both sides are picking up the pieces. GM will schedule heavy overtime through the fall at nearly all of its North American plants, trying to recapture as many of the 500,000 vehicles of lost production as possible.
To jumpstart sales, GM is offering 0.9% financing on most 1998 models and will fatten rebates on models such as Oldsmobile Aurora, from $2,000 to $3, 000. The No. 1 automaker's U.S. market share, which crashed to 20.9% in July, remained below 25% in August, but shouldapproach 30% in September, say GM officials.
Like a homesteader cleaning up after a tornado, GM is trying to look beyond the damage and grasp a vision of reconstruction. This is no time for business as usual.
"We absolutely lost customers permanently," says Ronald L. Zarrella, group executive in charge of North American sales, service and marketing. "Once you lose them, it's hard to get them back."
In the short-term the strikes do not appear to have been worth it. Would you trade $2 billion in lost profits for a 15% gain in engine cradle production from a stamping plant you probably don't need anyway? Would you, as a labor leader, force your members to forego millions of dollars in lost income and suffer continued insecurity just for a brief 14-month reprieve for three plants that will be sold or closed anyway two years from now?
From another perspective, however, the two organizations may have scared each other into a long overdue reality check. By challenging the legality of the strike and raising the prospect of a devastating $1-billion-plus damage award, GM made the UAW think twice about dragging the battle out until Labor Day.
But by staying out long enough to halt the launch of the new GMT800 pickup truck, the UAW inflicted more pain than GM was willing to endure.
Finally, both sides are hinting about an "ongoing high-level dialog to work through our differences . . . without resorting to costly work stoppages."
Sources close to the settlement negotiations say UAW leaders have given Chairman Smith an implied assurance that, at least through the end of 1998, there will be no tactical strikes at strategically vital parts plants. Such strikes, like this year's walkouts in Flint, and a March 1996 strike at two Delphi brake plants in Dayton, forced the company to shut down 27 of its 29 North American assembly plants.
Such a truce, if it holds, should enable GM to make up most of the lost production, keep its new pickup truck launch on schedule and finish the year with a strong fourth quarter.
It also sets the stage for what could be a sweeping redefinition of this long fractious relationship when the two parties meet next summer to hammer out a national labor agreement.
After weeks of hunkering down behind the scenes, Mr. Smith resurfaced at the University of Michigan management conference in Traverse City to declare "we are not in denial any more." Through the first week of August he set forth three initiatives that at least temporarily calmed the buzz, most critically amplified in Fortune magazine, questioning his ability to lead this complex and confounding company.
Among the moves, approved at the Aug. 3 board of directors meeting:
n Early next year GM will sell 15% to 20% of the stock in Delphi Automotive Systems, which should generate between $2 billion and $3 billion. Later, the remaining equity in the world's largest automotive parts supplier will be distributed to GM shareholders through an exchange of shares.
n Marketing chief Mr. Zarrella unveiled a radical overhaul of the company's hidebound sales and distribution system. Gone are the corporate vice presidencies attached to six distinct marketing divisions. In their place will be a brand management structure headed by current Chevrolet General Manager John G. Middlebrook, and a new leaner field organization led by current Pontiac-GMC chief Roy S. Roberts. Mr. Zarrella says the changes will take $300 million out of GM's annual $1.8 billion marketing budget, and up to 1,000 jobs out of its 5,000-person marketing staff.
n Mr. Smith will continue trimming GM's North American manufacturing network. That includes building new plants and closing older plants. In short, he wants to apply the modular assembly concept, soon to be launched at a small-car plant in Gravatai, Brazil, to GM's small-car assembly plants in the U.S., Canada and Mexico.
Let's take each initiative separately.
The Delphi spinoff has been expected for years. The news is that the initial public offering will be followed quickly by an exchange of Delphi for GM stock covering the80% to 85% not sold directly to the public. With a total market capitalization of $11 billion, the Delphi deal could be the largest initial public offering ever.
The UAW has not signaled that it will consider a separate labor contract, but Delphi President J.T. Battenberg III wants one. The union's 50,000 jobs within Delphi will be less secure as the world's largest supplier cuts its umbilical cord to GM.
"This is a major step," says Mr. Smith. "Being independent of GM will create new opportunities with OEMs who had been reluctant to do business with Delphi because of their corporate ties to General Motors."
It should help Delphi achieve its objective of generating half of its sales from outside GM's North American operations by 2002. The flip side: In order to maintain GM business, Delphi may have to rely more heavily on its rapidly growing Mexican manufacturing base where wages of less than $10 a day and lower capital investment requirements make it easier to compete.
Delphi already is combining its Chassis Systems Div. with its Energy & Engine Management group based in Flint. Alan S. Dawes, who had been vice president of Chassis Systems and is one of GM's rising young executives at age 43, will become Delphi's chief financial officer.
"Should GM decide to proceed with the sale as announced, the UAW's record is clear - we can and will aggressively work to protect the rights and interests of UAW members impacted by the sale," says Richard Shoemaker, head of the UAW's General Motors department.
Mr. Battenberg informed Mr. Shoemaker of the spin-off just prior to the early August announcement.
"Anytime you go through a change of this magnitude, there's certainly a period of concern," Mr. Battenberg says. "Delphi operates with 61 unions around the world. We will honor pre-separation commitments with all our unions."
The second, and most specific initiative, is the marketing shakeup. Since he arrived four years ago from Bausch & Lomb, Mr. Zarrella has been expected to overhaul the structure of five distinct marketing divisions that are part of the legacy of legendary GM Chairman Alfred P. Sloan.
Not only has he done that, he also has slashed layers, and up to 1,000 jobs, out of the cumbersome field organization through which GM supports its dealers.
At the foundation of the new structure are market-area teams, patterned after Saturn's field operation, that will be responsible for supporting dealers from all GM divisions, excluding Saturn. Team members will be rewarded on a pay-for-performance basis that emphasizes sales targets reflecting how Mr. Zarrella wants to position each brand, rather than maximizing any one division's volume or market share.
Those who meet or exceed the targets could earn bonuses worth between 20% and 25% of their base salaries.
"We're too complicated and we're too slow," says Mr. Zarrella. "We need to better recognize when customers' needs change and help them migrate to other brands within our company."
Mr. Zarrella also wants to trim the number of GM dealerships from about 8, 000 today to about 6,800 by the end of 2000.
Predictably, dealers' reviews of the plan are mixed.
"This is going to clear out a lot of the bureaucracy," says Frank Ursomarso, a large dealer near Wilmington, DE. "Now I have four GM franchises and I have four different people calling on me. That's way too many."
Mr. Ursomarso points out that he has a higher-than-average percentage of people over age 55 in his market area. So the Pontiac Bonneville is one of his hotter products.
"If this system works, I will know it when it becomes easier to get enough Bonnevilles," he says. "I particularly like the idea of them sending a guy in here who is going to be on an incentive plan."
In Sterling Heights, MI, Oldsmobile-GMC dealer Jim Muir is more skeptical.
"I wonder about this separation of the brand management function from the sales and service function," Mr. Muir says. "It seems that the heritage that is Olds, that is Chevrolet, or that is Pontiac is gradually going away."
Also going away will be sluggish selling car models such as the Oldsmobile 88 and Cutlass. Although Buick, Pontiac and Chevrolet officials publicly deny it, specula tion continues that the Riviera, Camaro and Firebird will go out of production in the next 12 months.
While Mr. Smith boasts that GM will introduce 23 new vehicles in the next three years, at least half of them will be light-truck or car/truck hybrids aimed at faster-growing market segments than the passenger cars they replace.
"In 1992 we had 109 models. Today we have 80. We have a product portfolio that gets us close to 70 models," says Mr. Zarrella. "There will be a continuing shift toward trucks. We still have more cars in the portfolio than we want."
GM still has more workers than it wants, too. Therein lies the powder keg that could prove far more explosive than the just-concluded Battle of Flint.
In 1996, fully aware that GM was in no position to guarantee a minimum number of jobs, the UAW went first to Ford, then Chrysler. The linchpin of the national contract was a largely symbolic pledge that hourly employment at those two companies would not fall over the next three years below 95% of what it was in October 1996. It was a promise GM simply could not make.
Next year, just for the sake of mutual survival, UAW President Stephen Yokich may have to focus on GM first. It appears that most of the 50,000 jobs GM wants out of its U.S. cost structure can be achieved through attrition, perhaps with an early-retirement package thrown in to accelerate the trend.
But there's some evidence management wants to cut deeper than that. There are at least three things happening to contribute to this.
First, Mr. Smith is pushing harder than ever to build the maximum number of models off the same chassis structure. Secondly, G. Richard Wagoner, president of GM's North American Operations, and Donald E. Hackworth, head of car and manufacturing operations, are increasingly impressed by the quality and productivity from the company's Mexican assembly plants in Silao and Ramos Arizpe.
Third, Mark Hogan, Mr. Hackworth's lieutenant for small-car development, is an aggressive proponent of modular assembly, which he pioneered as president of GM do Brasil.
Known internally as Project Yellowstone, Mr. Hogan's vision has scoped out a variety of scenarios, ranging from a new greenfield plant in Mexico, the southwestern U.S. or replacing existing operations in Lordstown, OH, or Lansing, MI. His mission is to make GM's small cars profitable by the end of this year, a target he probably won't hit. Wall Street analysts estimate that every GM small car loses an average of $1,000.
Modular assembly will turn unprecedented responsibility over to a small corps of suppliers, and drastically reduce the number of hourly workers needed to assemble a car. Whether those suppliers would agree to absorb UAW workers displaced from existing assembly plants, and how GM and suppliers would handle such workers' wages, are just two issues that illustrate how volatile this idea is.
In Traverse City, Mr. Smith said the company will build new assembly plants in the U.S., but will employ many less workers.
One supplier executive familiar with GM's Delta project, from which the 2002 Saturn SL, SC, Chevrolet Cavalier and Pontiac Sunfire will come, says GM has not yet given a green light to a full application of the Yellowstone concept. Those familiar with the Delta platform say it will incorporate many features common to modular assembly.
But where once a new Mexican plant was management's first choice, there is now a willingness to build a new plant adjacent to existing plants in either Lordstown or Lansing. The problem is that there is only need for one. The other plant likely closes, while more production is added to Ramos Arizpe and the CAMI joint venture with Suzuki in Ingersoll, Ont. If anyone can sell that deal to the UAW, he or she should be GM's next CEO.
For all of its theoretical hype, modular assembly is an unproven concept. GM's "Blue Macaw" plant in Brazil is almost a year from production. Volkswagen's Resende, Brazil, plant, in which suppliers actually put their parts on the car, so far is falling far short of productivity and quality goals.
"The big problem as you get into larger modules is that the OEM's confidence level in suppliers tends to waver," says Bradley R. Bump, vice president of the Berkt Group, a Farmington Hills, MI, consulting firm that has studied modular assembly operations in Europe and South America. "You take a company that does interiors: They may know plastics and how to build up instrument panels, but there are program management skills needed that they may or may not have. I think modular assembly will be more of an evolutionary process."
Only Jack Smith and GM's board of directors know if they have that much patience.
Read more about:
1998About the Author
You May Also Like