SRG Develops Louvered Grille for GM Trucks
The prototype grille is part of an effort by SRG to gain new business in the relatively stagnant U.S. new-vehicle market with products it says not only are fashionable but functional.
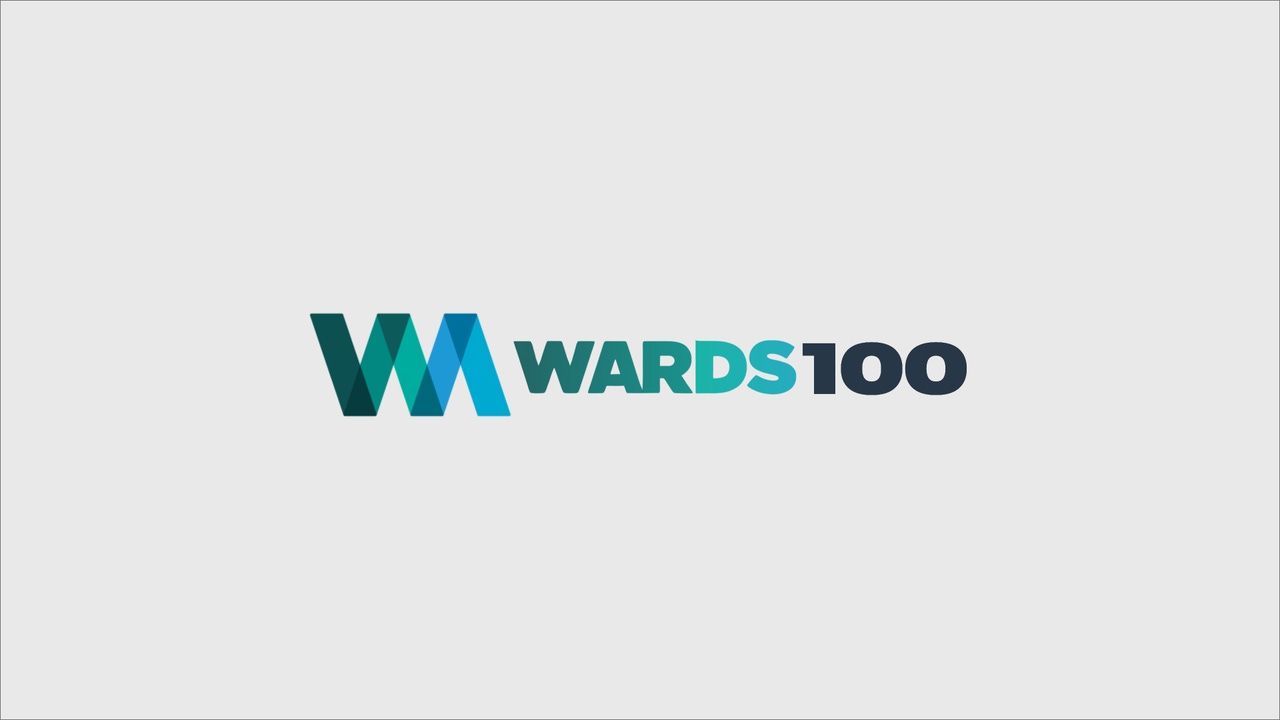
TAYLOR, MI – SRG Global Inc. has developed a prototype louvered grille for General Motors Co. aimed at improving the efficiency of the auto maker’s fullsize pickup trucks to help meet upcoming stringent U.S. emissions and fuel-economy regulations.
SRG, best known as a supplier of chrome-plated plastic parts, is working with GM on the project, says Jon DeGaynor, SRG vice president-business development and strategy.
“What we heard is that GM is moving 100% of their vehicles to louvered grilles,” DeGaynor tells Ward’s on the sidelines of the grand opening of SRG’s new Advanced Development Center here.
The BMW 3-Series already has such a feature, he says, although it is a secondary part, mounted behind the grille. “We’re trying to find a way to do it more efficiently, less expensively, as an integrated part.”
In theory, the louvers would be connected to the engine control module, opening and closing per engine temperature, says Dave Prater, SRG vice president-product engineering and development.
Closing off airflow not only reduces carbon-dioxide emissions, by allowing the engine to heat up faster, but also increases fuel economy by reducing drag.
The prototype grille is part of an effort by SRG to gain new business in the relatively stagnant U.S. new-vehicle market. “What will separate us in the future are cosmetic products that also provide a function for the vehicle,” Prater says.
SRG’s prototype GM grille closes, opens per engine temperature.
The opening of the 46,000-sq.-ft. (4,27- sq.-m) facility here, purchased last year and previously used as a chrome-plating operation, allows SRG Global to develop new ideas, such as the louvered grille, and perfect manufacturing consistency for production parts, DeGaynor says.
SRG Global was formed last year after Guardian Automotive Inc. purchased the assets of Siegel-Robert Automotive Inc.
Work at the Taylor center, which at any given time employs 10-15 people, will include perfecting the plating processes for popular satin-finished chrome. Pointing to American Honda Motor Co. Inc.’s signature Acura grille SRG plates, DeGaynor says color consistency can be an issue with satin finishes.
“You can do it once, but to be able to do it over thousands of parts for days, bright (chrome finishes are) easier,” he says, noting SRG is the largest consumer of matte satin finish-related chemicals globally.
“Everybody wants their own color, their own shade. So part of what we want to be able to do (at the Advanced Development Center) is to say (to a customer), ‘OK, we’ll master it. We’ll make sure we know we can launch it exactly at your color,’ because that’s a huge challenge.”
SRG primarily supplies chrome-finished exterior pieces, such as grilles, but also is shifting more toward interior trim as truck sales decline.
Acura signature grille with SRG-applied satin-finished chrome.
“Two or three years ago, all the plater capacity in North America was taken up because of the (high) percentage of trucks,” DeGaynor says. “If you think about a Ford F-150 grille vs. a Toyota Camry, or a Toyota Tundra vs. a Toyota Camry, it’s four or five times the surface area.
“We plate on a surface area basis, (and) the tradeoff between a Tundra and Camry (is) four times the capacity. Now we start looking at other places to use that capacity.”
In addition to housing a chrome-plating line, the Taylor facility, which is not far from SRG Global’s Warren, MI, headquarters, also can produce plastic injected-molded parts for coating and testing, boasting four presses ranging from 165 tons (150 t) for small emblems to 2,200 tons (1,996 t) for truck grilles.
Testing equipment here includes a copper accelerated salt spray that mimics 10 years of corrosion; walk-in oven and freezer; automated thermo-cycle chamber to test smaller electro-plated parts; and a humidity chamber.
An Electro Plating Wet Lab can do full electro plating on plastic and surface tension testing to lessen defects in the plating process.
SRG also touts the Advanced Development Center’s environmental aspects, including the ability to neutralize and convert Hex-Chrome to Tri-Chrome, the latter more environmentally friendly, it says.
SRG operates seven North American manufacturing plants and two technical centers in addition to the new Taylor facility, which has room for about 25-30 employees, Prater says.
Overseas, SRG has one technical center and two plants in Western Europe and one factory and a tech center in China. DeGaynor says the company is looking to grow its Chinese footprint, noting he has made multiple trips to the country this year, with more planned.
Additionally, SRG is due to open a new plant in Poland this month and hopes to establish operations in Mexico by 2011. Southeast Asia, India, Brazil and Russia are other regions the company is exploring for new operations.
DeGaynor says the smaller vehicles favored by developing markets don’t necessarily limit SRG’s prospects for growth. “Vehicles are getting smaller, but they are not getting de-contented.”
About the Author
You May Also Like