What Are We Measuring?What Are We Measuring?
Finally, the General Motors Corp. strike is over, but the vast majority of us remain confused about what was actually resolved in Flint.I really don't want to say who's right and who's wrong. I was troubled, however, by much of the newspaper coverage that presented the strike as primarily an issue of efficiency. Reporters in many articles often quoted the Harbour Report, which, based on their analysis,
September 1, 1998
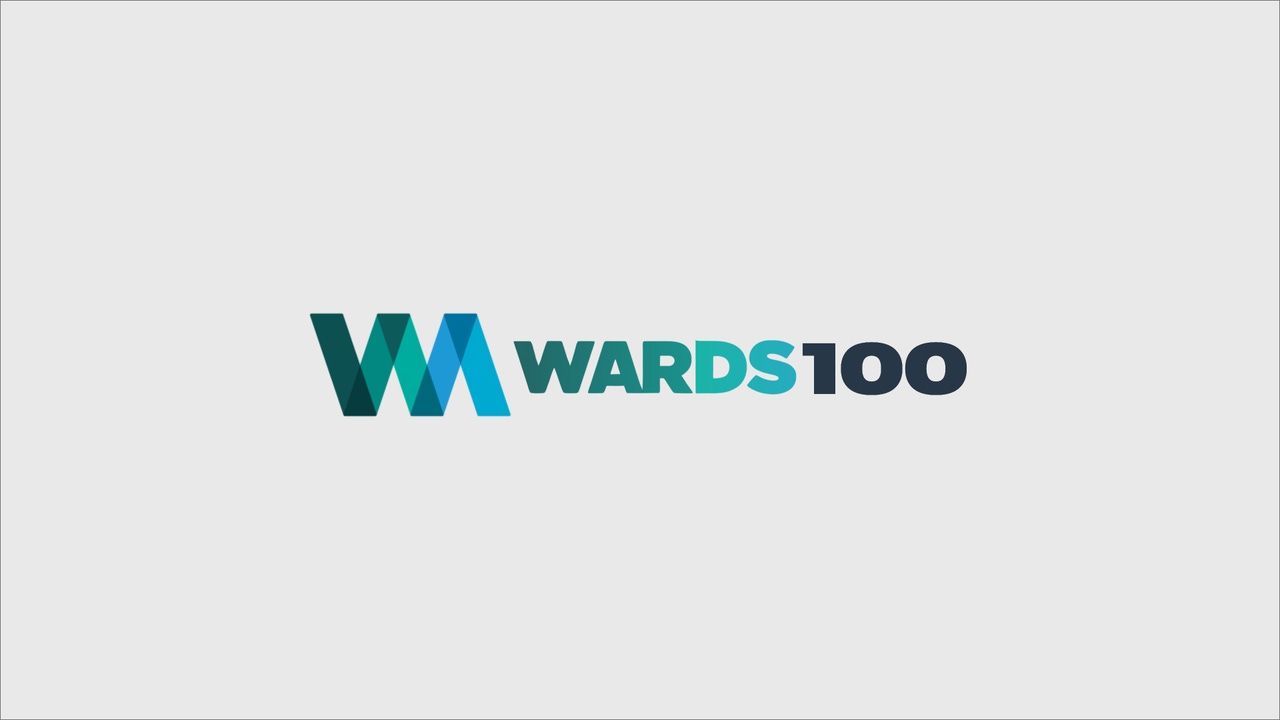
Finally, the General Motors Corp. strike is over, but the vast majority of us remain confused about what was actually resolved in Flint.
I really don't want to say who's right and who's wrong. I was troubled, however, by much of the newspaper coverage that presented the strike as primarily an issue of efficiency. Reporters in many articles often quoted the Harbour Report, which, based on their analysis, concluded that American carmakers generally are less efficient than their Japanese counterparts.
I've talked about this report before, but I want to talk about it again because most people still don't understand it, and consequently, come to a wrong conclusion.
The Harbour Report compares the efficiency of the various car companies based on the number of workers, or the number of labor hours, required to produce a car. Unless you read the report carefully, it is easy to assume that the more efficient a company is, the more profitable it is. Yet, Nissan Motor Co., which is the most efficient, (based on workers per car) is the least profitable automaker studied. Meanwhile, GM reported an operating profit in North America of $2.3 billion, even though it was the least efficient.
During the strike, GM's position was that it must become more efficient in order to improve profitability. Such efficiency gains require concessions from the UAW in terms of higher production quotas, fewer job classifications and more flexibility to move from one task to another.
Improving your efficiency, however, does not always translate into greater profits.
When a company talks about improving its profitability there are many more factors involved than just workers per car.
For example, if I give a person a tooth brush and have him clean five rooms and I give another person a vacuum cleaner and have him do a similar job, there's no question that the person with the vacuum cleaner is going to be more efficient. However, to determine who does the job the cheapest you have to make a cost analysis which takes into account the cost of labor, the cost of the tooth brush vs. the cost of the vacuum cleaner, etc.
The Harbour Report may be worthwhile to people who know exactly what it measures and can apply it correctly to their own operation. However, total efficiency is mostly controlled by manufacturing and involves many factors.
Take equipment in a stamping plant, for example, which happened to be one of the plants involved in the GM strike. If this facility does not have a proper size transfer press with the latest technology, it cannot take advantage of such stamping innovations that can double production of right and left panels at the same time. The Japanese discovered this technology early on and were one of the first to apply it, considerably ahead of any American company.
Another important factor is the design of the panels being stamped. If engineers, manufacturers and designers work closely together, they can come up with a design that will simplify the manufacturing process and minimize the number of operations to produce it. This can dramatically reduce costs.
On the other hand, designers can create a panel configuration so complex it requires an elaborate, expensive die. In addition, complex die designs also may have to be made from special, more expensive steel. That, of course, adds cost.
Designs that take advantage of the latest manufacturing technology give engineers more leeway in reducing costs. For example, by taking advantage of laser welding, one may weld metals of different thicknesses together, eliminating the need for additional reinforcements and brackets.
Tooling costs always are a major expense and can be greatly influenced by the way the funds are allocated. For example, I'm always amazed to find that one shop is building a set of dies for the outer door panels; another shop is building the tools for the inner door panels, and still another is building the tools for all the related brackets. It would be a lot easier and less expensive if all these tools were built in one place. You would avoid all the squabbles normally associated with matching panels. You also wouldn't need all the people required to coordinate changes between different locations.
Higher equipment use also results in a better return on your investment. But it may require you to staff a plant with more than the minimum number of people.
The Japanese also are able to minimize the number of equipment breakdowns by having good preventative maintenance programs. They also minimize the length of breakdowns by reacting quickly with the necessary fixes. What's more, when a breakdown occurs in a Japanese plant everybody pitches in - including the press operators - to get the equipment running again as quickly as possible. That doesn't always happen in U.S. Big Three plants.
So when you talk about improving profitability, you must go much deeper than just workers percar. - Mr. Sharf is a former vice president for manufacturing at Chrysler Corp.
Read more about:
1998About the Author
You May Also Like