Honda Alabama Workers Leave Mark on New Odyssey Minivan
Honda not only sought workers’ input early, it embedded a number of them into the company’s research-and-development team in Ohio a full year before any drawings of the new minivan were released.
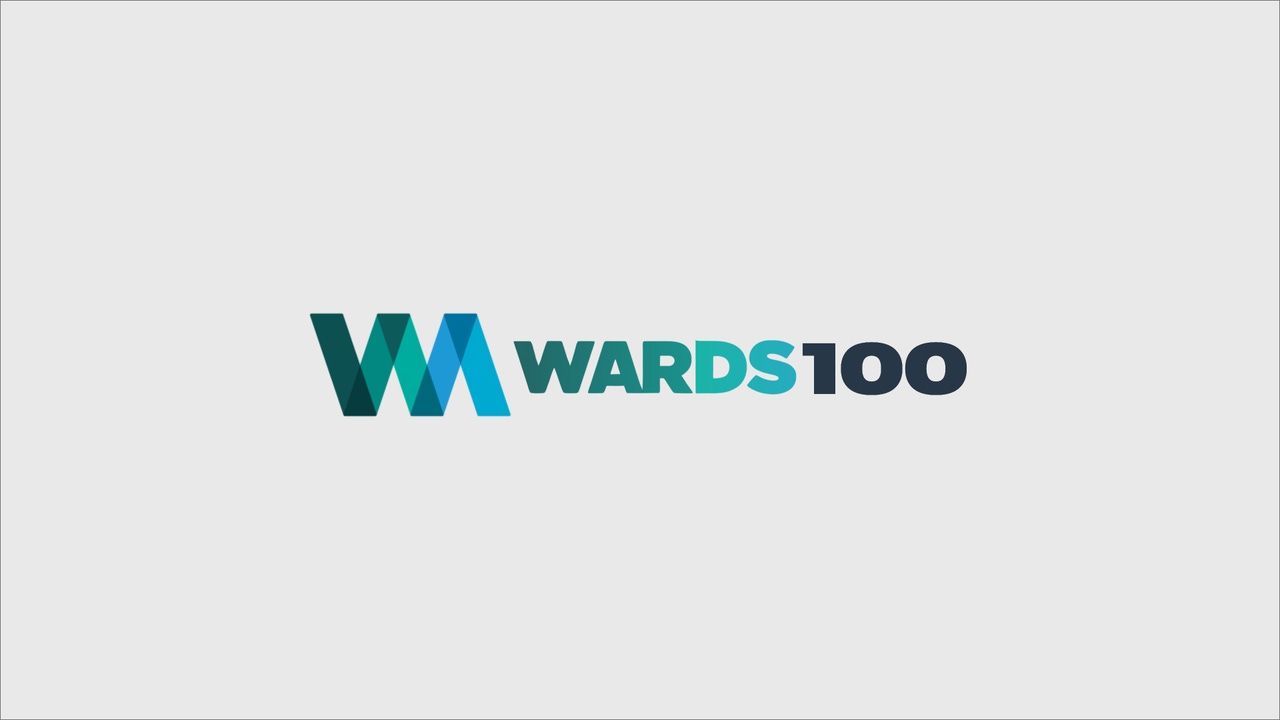
Special Coverage
CAR Management Briefing Seminars

TRAVERSE CITY, MI – Thanks to its assemblers, the redesigned-for-’11 Odyssey minivan will continue to challenge the Chrysler Town & Country as the segment’s best product, says Mike Oatridge, vice president-Honda Mfg. of Alabama LLC.
Workers at the auto maker’s Lincoln, AL, plant are launching production of the new Odyssey, which enters its fourth generation with its latest redesign.
But the vehicle also ranks as the first Honda product fully designed and developed in the U.S., and much of the credit goes to assembly workers in Lincoln, Oatridge says.
“A product that is easier to build for our associates, one that incorporates input from the most fundamental level of design, has far greater potential to be a superior product for our customers,” he tells the annual CAR Management Briefing Seminars here.
Honda not only sought workers’ input early and often, it embedded a number of them into Honda’s research-and-development team in Ohio a full year before any drawings of the new minivan were released.
“It provided them a chance to learn about the conceptual ideas for the product and how it would impact our (Lincoln) plant,” Oatridge says.
On the plant floor, Honda put together a team of trainers from the assembly line, so change requests would be communicated by the people closest to the production of the vehicle.
“In the past, we would begin writing our operation standards after the first prototypes were built. But this time, associates from the floor helped write the operation standards even before the first prototype was built,” Oatridge recalls.
Assembly-line workers real experts in vehicle production, Oatridge says.
That allowed Honda engineers and assemblers to craft standards geared to their actual work processes, not some hypothetical situation. Feedback was sought from every worker at Lincoln, with a trainer following prototypes down the assembly line and collecting input on the spot.
“This resulted in a greater buy-in from our associates, as they realized how serious we were about reflecting their voices into the build process,” Oatridge says.
The interaction led to a number of manufacturing changes, saving money, energy and ensuring better quality.
For example, assemblers use a rubber mallet to ensure the rear-quarter glass on the current Odyssey fits properly, as a great deal of force is necessary to set it in place.
A change was needed, so Honda outfitted workers with high-tech gloves to gauge the impact needed to set the glass. Based on the data received, a new clip was designed to make the glass easier to set and featuring an audible “click” once it is properly engaged.
A new headliner design from the assemblers also enhances quality and ergonomics on the ’11 Odyssey. A large, complex part with wiring harnesses to accommodate lighting, HVAC parts and entertainment systems, it requires a lot of overhead work.
The size of the current headliner forces the auto maker to ship it stacked horizontally, which takes up too much room in trucks and adds shipping costs. But with early input from assemblers and collaboration with engineers, Honda determined a way to modify its design.
“Certainly R&D could have pushed back and kept the original design, but they had respect for a more associate-friendly quality part,” Oatridge explains. “The new design uses a shorter, one-piece headliner.”
As a result, the headliner can be installed through the front windshield opening, instead of the rear of the vehicle. Additionally, Honda has moved installation of wiring harnesses, HVAC parts and entertainment to a supplier as a sub-assembly. Fitting it into the minivan now demands very little overhead work.
The auto maker now can stack the new headliner vertically, so fewer trucks are needed, saving shipping costs and energy. And because it is heavier, a lift assist has been added to make the part easier to install.
Workers also helped preserve the design concept of the new minivan. The ’11 Odyssey features the brand’s trademark lightning bolt beltline but with a more cab-forward design. The new styling pushes the top of the windshield back about 2.4 ins. (6 cm) and the bottom edge forward by 2.2 ins. (5.6 cm).
The new design also made the instrument panel larger and more cumbersome to handle. In the current model, installation goes through the door opening.
But using virtualization technology, Honda determined the new IP would not fit through the door. Finding the snafu early on, the auto maker was able to make a quick change to solve the problem and preserve the concept design’s integrity.
“Throughout my Honda career, it has been proven to me again and again that associates at the spot are the experts,” says Oatridge, who joined the auto maker’s Canadian operations in 1989. “They have the ultimate responsibility to putting all the pieces of the puzzle together for the customer.”
Read more about:
2010About the Author
You May Also Like