Honda Continues Quest to Drive Down Assembly Line Injuries
Plant injuries declined from 50 per 100 workers annually a decade ago to 5.5, the auto maker says. Work to improve ergonomics, including some collaboration with Ohio State researchers, continues.
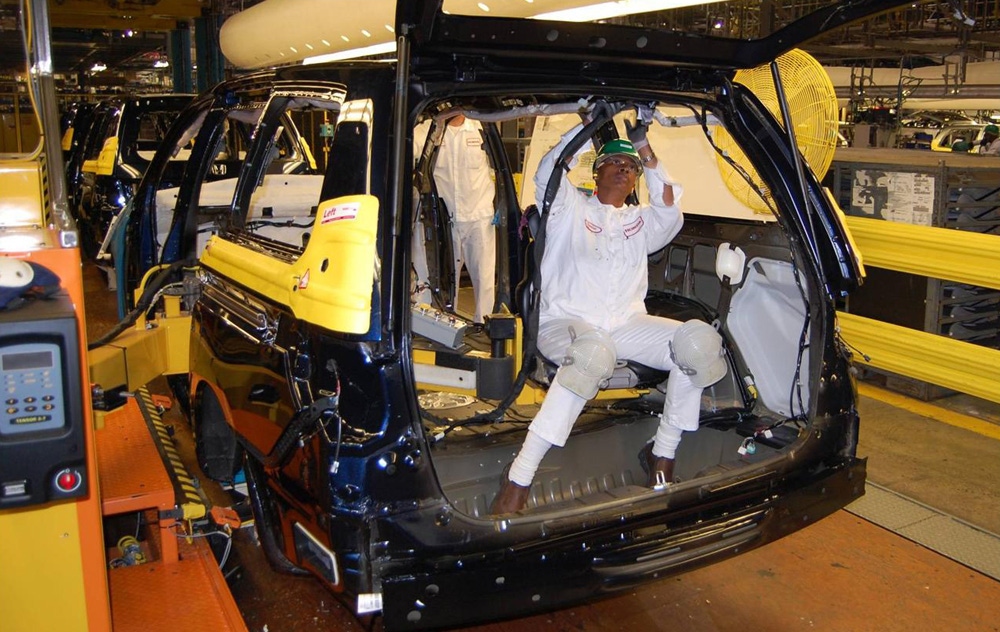
Keeping assembly-line workers healthy and accident-free is paying off, with a 90% drop in injuries at Honda of America Mfg. over a 10-year period, says Jeff Garlock, associate chief engineer.
“The entire (auto) industry is dealing with an aging workforce and needs to help workers achieve tasks more easily,” he says.
With cooperation from assembly-line workers, HAM’s injury rate declined from nearly 50 injuries per 100 employees a decade earlier to 5.5 in the fiscal year ended March 31, 2011.
“We have a big interest in keeping our associates healthy,” Garlock says. “Honda has a big incentive to design processes that don’t hurt (workers).”
Honda engineers have collaborated on ergonomics with outside researchers, including a team at Ohio State University that tested and validated devices and processes developed with the goal of reducing assembly-line injuries.
OSU researchers led by William Marras, a professor who occupies a Honda-endowed chair in the department of integrated systems engineering, evaluated solutions to ease tasks associated with reaching into the recesses of vehicles. They can cause shoulder and back strains that could sideline workers.
The researchers, in collaboration with Honda engineers, tested a cantilevered chair that allows workers to sit while reaching into vehicles.
They also tested a rotating car carrier that tilts a vehicle sideways so standing workers can reach inside to perform nine different operations.
The original Super Chair, as Honda engineers dubbed it, had a bucket seat that prevented workers from moving freely and cost $100,000 to build. But OSU and Honda engineers collaborated on a modified design that features a flat seat and costs only $4,000.
Using the car carriage is the better overall option for preventing injuries, Marras says. “Under these conditions, if you can tilt the car, the chair becomes unnecessary.”
But Honda engineers decided against using the rotating car carrier for now, because it was deemed too expensive and would require extensive modification of assembly lines. Garlock says the Super Chair now is employed in Honda’s Alabama plant on both the Odyssey minivan and Pilot cross/utility vehicle lines.
The tests were performed in the OSU Center for Occupational Health in Automotive Manufacturing that Marras directs. Honda asked Marras’ team to test an existing chair already used in a number of its own plants.
Ten male and female workers, five of whom were experienced assembly-line employees, sat on a padded seat at the end of an L-shaped steel beam locked into a track above.
The “L” slid back and forth as workers pulled the chair across the floor and into the floor with their legs. Five college students representing first-time, untrained workers also participated.
Researchers concluded the chair reduced loads on the spine and shoulder stress when the workers installed the roof console and insulation, as well as tightened bolts in the center of the car.
Performing tasks on the edge of the vehicle while sitting in the chair reduced spine load but did nothing to limit shoulder stress.
“We thought that sitting inside the car would make installing the seatbelt easier, but it turned out that you’d need two right hands,” says Sue Ferguson, senior research engineer and lead author of the study.
In the study, a dozen people installed equipment in a car’s interior, underbody and engine compartment while standing. Researchers measured stresses on workers’ bodies when the car was tilted at different angles.
Seven of the nine different installation tasks became much less strenuous when the car was tilted 45 degrees on its side. Similar improvements were noted for the other two tasks when the car was rotated 90 degrees.
The test subjects were different in the two studies because workers in the chair study were from an area in the plant where the device could be used. The workers in the rotating-test carrier were from a subassembly area in the plant.
It might be possible to reduce costs of the carrier, which has infinite adjustability, if one with fixed angle is used, officials say.
Honda engineers constantly assess and grade assembly-line plant processes and have instituted practices to reduce injuries, including rotating workers more frequently in various tasks.
Exercise regimens also have been inaugurated to harden workers for their tasks, especially those they haven’t performed before.
Honda also provides videos workers can watch to learn how specific tasks need to be performed at each station along the line. This was instituted at Honda’s East Liberty, OH, assembly plant more than a year ago.
Honda spokesman Ron Lietzke says Marras’ OSU team has been important to Honda for evaluating ergonomic stress. The researchers assess the strain of repetitive motions. Marras has been in the forefront of this kind of research, Lietzke says.
The OSU research also has helped Honda engineers evaluate handling the kickback stress produced by torque wrenches.
In addition, the researchers evaluate the parameters for reach and push-pull tasks, as well as the insertion of clips in the vehicles. Honda’s manufacturing engineers feed this data back to designers.
Honda encourages assembly workers to report discomfort at its earliest stages. “We want to tackle it before it becomes serious for them,” Lietzke says.
OSU evaluates and grades assembly processes green, yellow or red. Those labeled as red are eliminated. “Our target is zero injuries,” Lietzke says.
“The overall challenge was to change the culture, where injuries are no longer accepted as part of the business,” says Mark Salsbury, chief of HAM safety initiatives. “We cannot just accept injuries as inevitable.
“I am not saying an injury will never occur,” he admits. “I am talking about the way we respond to every single injury, no matter the severity. I am talking about a mindset where if we had done something differently, we could have prevented an injury.”
About the Author
You May Also Like