Honda Says NA Tool Industry Viable
Honda of America launched an initiative in 2002 designed to help the North American tooling industry thrive by collaborating with suppliers and tooling companies.
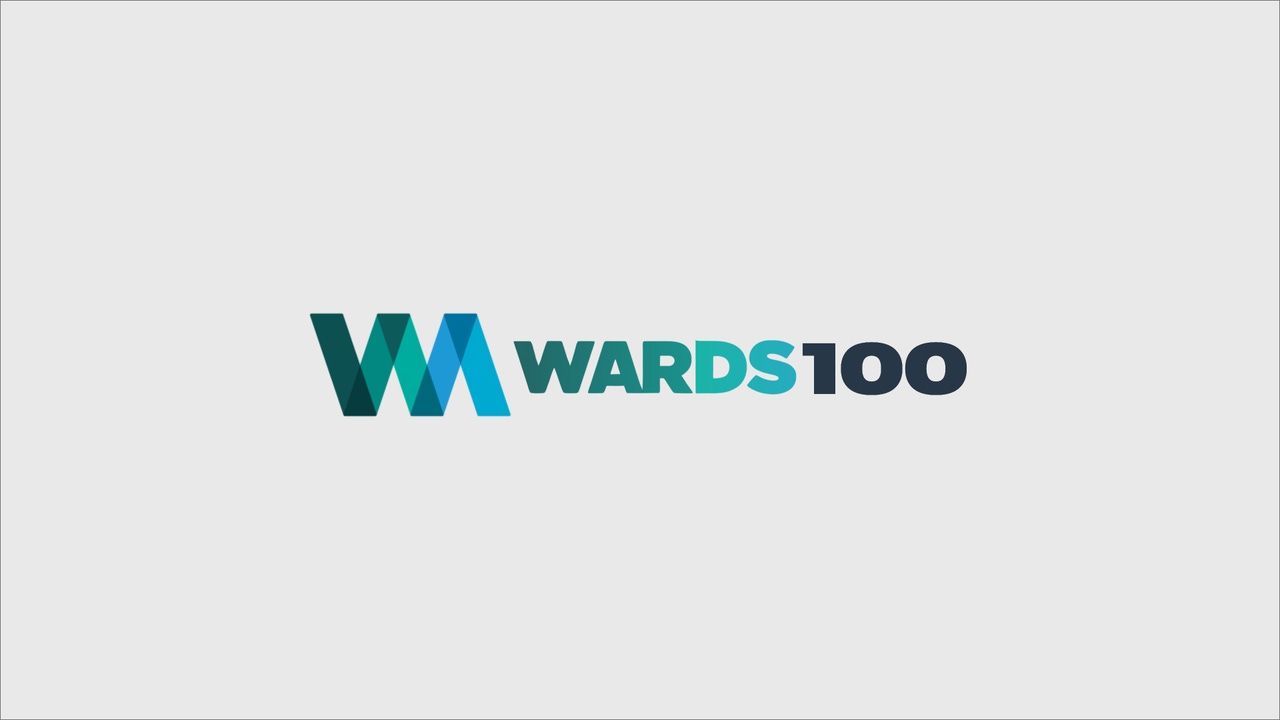
TRAVERSE CITY, MI – Contrary to conventional wisdom, the North American automotive tooling industry remains viable and has a good chance of becoming a strong contender on the global tooling scene in coming years.
That’s the outlook as viewed by Honda of America Manufacturing Inc.’s Timothy Myers, senior manager-North American purchasing. Myers is responsible for new model and quality systems, supplier development, the supplier support team and HAM’s Tooling Center.
Myers addressed a session at the Management Briefing Seminar here today that attempted to answer the question of whether there will be a domestic tooling industry 10 years hence.
“Yes, there can be a North American tooling industry, and we’ve developed a model on how to succeed,” Myers tells Ward’s in an interview before his speech.
Launched in 2002, the project brings together HAM’s purchasing and R&D group, its component suppliers and tooling companies in the U.S. and Canada to seek the most efficient means of bringing new models into production while meeting quality, cost and delivery targets, Myers says.
“We want to have tooling shops and suppliers to have a strong relationship,” he says, with Honda being the catalyst.
“In the old thinking, tooling was considered a commodity because of the high volumes involved,” Myers points out. “A lot of designs were done on paper; there was a craft mentality involved. Today we have smaller volumes and now look at tooling as value added” to the entire manufacturing process.
HAM’s major goal is to resolve issues and problems well ahead of production startup, which necessarily involves tooling suppliers with a shared interest in the outcome. “It’s a co-management concept to facilitate relationships between parts suppliers and tool makers,” he says.
Japan was key source of HAM tooling for latest Civic.
Four tooling manufacturers have signed on to the project so far: Northwest Tool & Die and Rapid Die & Engineering, both of Grand Rapids, MI; Quaker Mfg. of Salem, OH; and Unique Tool & Gauge of Windsor, Ont., Canada.
Myers says HAM anticipates having a total of six to eight tooling companies on board in the near future.
Tool shops traditionally have had little assurance of future business, creating inefficiencies in their operations, he says. “They didn’t know where they stood on the curve,” Myers says.
Under the HAM system, tool makers are assured a role for the long term, assuming they perform as expected. “We think they can feel more comfortable knowing that they have a reasonable assurance of a return on their investment,” Myers says. “It has to be a long-term viewpoint. That’s where the value comes in.”
A chief advantage of retaining the same tooling firms and suppliers is the potential for sharply reduced testing, assembly, machine and design times when new models come into production – especially if the components aren’t drastically re-designed, he says. Using a base model, those functions took a total of 695 hours, he points out. Using the co-management scheme cut that time to 337 hours for the next new-model cycle, he says.
HAM does not award contracts to the tool makers. “It comes down to trust. We’ve had to get everybody to trust everybody else,” he says.
Myers acknowledges the U.S. tooling industry has experienced declining fortunes. “That’s why we needed a new model.”
Based on a HAM internal global benchmark index of 100, in 2002 when the project began, the two shops that joined in that year stood at 152. By 2006, when the current four shops were aboard, that dropped to 115.
With a 44% share, Japan was the key source of HAM tooling for the latest Civic. Other global suppliers had a 15% share. A HAM co-management initiative accounted for 15%, and supplier-controlled local sourcing totaled 25%.
About the Author
You May Also Like