Lean and Green
Honda will re-do all of its plants by 2003 SUZUKA, Japan - In refurbishing its Suzuka assembly plant, Honda Motor Co. Ltd. has taken "best practices" from its production facilities in Japan and overseas.The company's goal: to put in place a "green" manufacturing system by 2003.The No. 1 and No. 3 Suzuka lines will be the "standard" for all Honda production facilities around the world, says Honda President
February 1, 2001
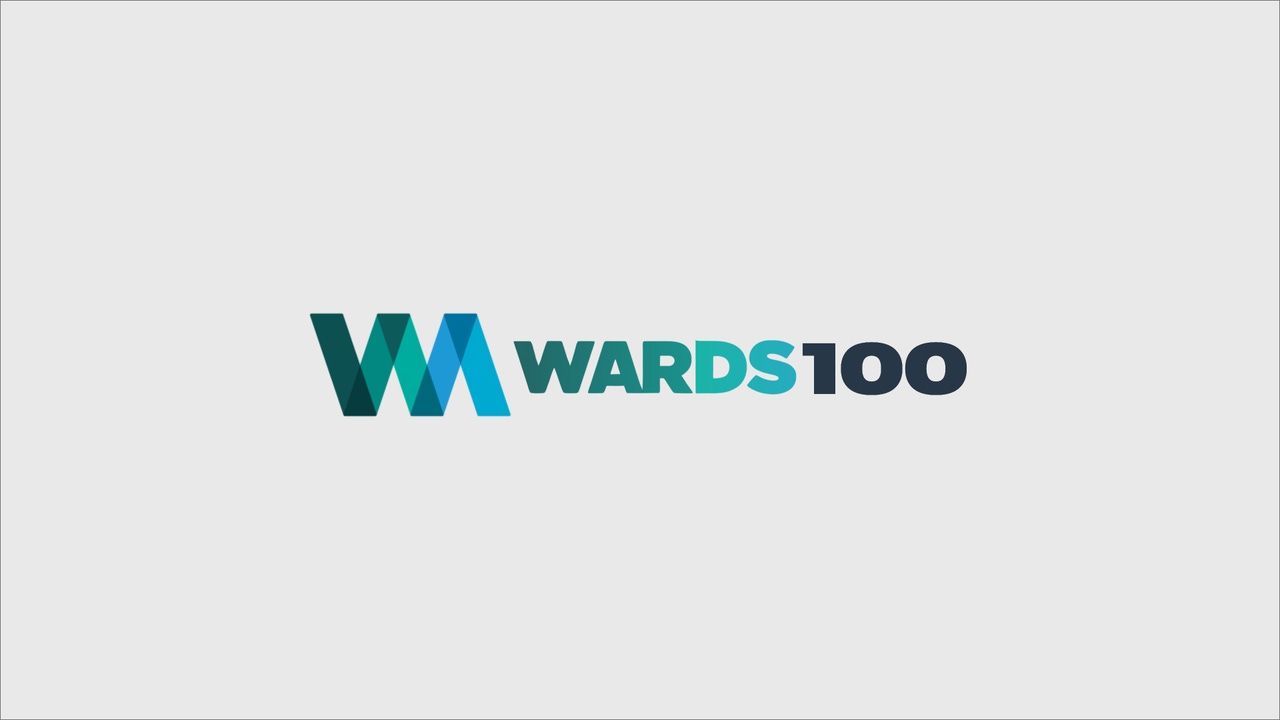
Honda will re-do all of its plants by 2003 SUZUKA, Japan - In refurbishing its Suzuka assembly plant, Honda Motor Co. Ltd. has taken "best practices" from its production facilities in Japan and overseas.
The company's goal: to put in place a "green" manufacturing system by 2003.
The No. 1 and No. 3 Suzuka lines will be the "standard" for all Honda production facilities around the world, says Honda President Hiroyuki Yoshino. "Our objective is to respond flexibly and quickly to market changes, to create a clean and energy efficient manufacturing process, and to build a production line in which each individual involved in the process can exert his or her wisdom."
In the process, Honda expects to cut global retooling and manufacturing costs by $1 billion (100 billion) over the next four years. Included: $700 million (70 billion) in vehicle assembly and $300 million (30 billion) in powertrain production.
Not coincidentally, the automaker plans 20 new product launches over the next three years, a goal made easier - and cheaper - by employing the new system. Investment to overhaul the No. 1 Suzuka line came to roughly half the amount spent for construction of the new No. 3 line in 1989.
Although Honda declines to disclose investment amounts, the No. 3 Suzuka line is similar in many ways to Mazda Motor Corp.'s No. 2 Hofu line, which cost $60 million (60 billion) to construct in 1992. Both facilities were built during Japan's economic bubble; both feature high levels of automation in final assembly. Extrapolating from the Hofu investment, analysts estimate that the No. 1 Suzuka line cost around $300 million (30 billion).
The biggest saving in percentage terms was in final assembly where Honda slashed investment cost by 55% when compared to the No. 3 line's price tag; welding and paint shop expenditures were 50% and 40% lower. Honda declines to disclose details about investments made in the plant's stamping and plastic molding shops, though it says the sums were minimal.
Resulting from improved equipment and assembly processes, including increased usage of modules, manpower requirements have been cut by one-third; utility costs are down one-fourth.
Equally significant, tooling costs for each new model launch - potentially every car in Honda's lineup - will be cut by more than 50% as virtually no investment is needed to modify the line's flexible final assembly and painting shops.
Even in welding, tooling costs will be reduced by half, due mainly to increased usage of "flexible" welding jigs and general-use pallets. In stamping and molding, savings on the order of 20% are envisioned.
And on the productivity side, time through the line has been cut by 30% to 13 hours, from 16.5 before.
Unchanged at 10 days for mixed assembly lines such as those in Suzuka and Sayama is the company's quick ramp-up from start of production. In fact, driving the decision to introduce the new system was the unexpected popularity of the CR-V.
When the model was launched in 1995, Honda originally planned to produce it in Suzuka, then was forced to shift export models to Sayama. It took months to tool up at considerable expense.
And there's another big benefit: Customers can now take delivery of their car just two weeks after ordering it, one week faster than today.
Honda Managing Director Motoatsu Shiraishi notes that by adopting "flexible" welding jigs, the automaker can assemble eight models on the same line, up from five before.
This flexibility has analysts drooling. Jardine Fleming Securities (Asia) analyst Stephen Usher explains, "Greater flexibility in manufacturing will enable the company to shuffle products between plants as dictated by changes in demand. As a result, Honda also will be able to introduce new models more quickly and at lower cost than the competition."
The company's estimate: a 20% cut in ex-factory price.
Mr. Yoshino says, "We have half the production capacity of Toyota, GM and Ford. If we hope to compete with companies that have 4 to 5 million units of capacity, we must have a better manufacturing system than they do." Globally, Honda built 2.4 million vehicles in 1999.
TOTAL INVESTMENT: NEARLY $1 BILLION Analysts estimate that the total investment, when the system is in place at Honda's main production facilities overseas, will approach $1 billion. Refurbishment of the Suzuka and Sayama plants will cost about $470 million (51 billion).
An estimated $900 million investment in the new Lincoln plant in Alabama and the Alliston and Swindon lines in Canada and the U.K. is not included in the total.
In Japan, two-thirds of spending (around $345 million) is earmarked for the Suzuka and Sayama plants. The bulk of the remainder will be for construction of a new engine plant in Sayama, the first stage to be completed in spring 2001. The automaker has no immediate plan to shut down the 47-year-old Wako engine plant, located 13 miles east of Sayama.
Most of the Suzuka and Sayama investment is earmarked for welding, painting and final assembly. None will go to Yachiyo Industry Co., Honda's minivehicle affiliate, or to the automaker's Tochigi sports car and Hamamatsu transmission plants.
TARGET: 2003 Honda intends to have its "green" manufacturing structure in place by 2003. Already, it is in use at the No. 1 and No. 3 Suzuka and No. 2 Sayama lines in Japan. Overseas, it is up and running at Honda of Canada Mfg.'s Alliston, Ont., plants (both No. 1 and No. 2 lines) and Honda of America Mfg.'s East Liberty, OH, unit.
By the beginning of next year, the system will be in place at Honda's No. 1 line in Sayama and Honda of the U.K. Mfg.'s No.1 Swindon line. A new No. 2 line in Swindon and all-new assembly plant in Lincoln, AL, are scheduled to open in late spring and late autumn next year. Both facilities will adopt the new production system.
The No. 2 Suzuka line, which makes SUVs and vans (such as the CR-V, Life, SM-X, Step Wagon and HR-V), will be shut down in March. No decision has been made on future use of that space.
The most extensive renovation was done on the 31-year-old No. 1 Suzuka line where all three shops (welding, painting and final assembly) were overhauled. This was its first major refurbishment.
Closed for four months at the beginning of last year, the line began production trials after Japan's "Golden Week" holiday in early May. Full operation began in September, and already daily production has reached capacity of 500 units. With the addition of a second shift in February, output will be upped to 1,000 units. The line produces the 3- and 5-door versions of the HR-V, Logo and new Civic.
Meanwhile, the No. 3 line makes 3- and 4-door Civics and Integras along with 3- and 5-door versions of the Logo, Orthea, Partner, CAPA and Life, all wagons or vans of varying types. Line capacity is 1,050 units per day, unchanged from before the renovation.
Mr. Shiraishi says all 10 Civic and Accord assembly lines will basically be the same.
The No. 2 Alliston line and new Lincoln plant will concentrate on sport/utility vehicles and passenger vans. Thus their welding and paint shops will not be interchangeable with Honda's main car lines, but will be compatible with each other.
Installation of the system at Honda's smaller plants - in Brazil, India, Indonesia, Malaysia, Mexico, the Philippines and Thailand - where production is 100 to 150 units per day - will take place from 2003.
BY OPERATION * In the welding shop, Honda reduced bodies in process and energy consumption by 40% and 20%, respectively, while cutting manpower requirements by a third. To achieve these results, the company focused on reducing "model specific" investment.
Mr. Shiraishi explains, "We developed jigs that were not dedicated to specific models. We also installed common transport processes employing general-use pallets and, to the extent possible, standardized body specifications between models."
Other features include: * Spot welding speed has been doubled by switching to electric-driven robots (from conventional hydraulic units) and by adopting a new "server gun" welder. Developed and produced by Honda Engineering Co., the new welder contributes to a 46-second takt (the time it takes a vehicle to move through the station), 20% faster than before.
* It takes 3 minutes to reposition welding jigs for different models, thus the slightly faster takt time than in the final assembly shop. The smallest production lot is 20 units.
* Of the shop's 162 welding robots, one-third fewer than before, 98% are new. All units were supplied by Fanuc Ltd. and Yaskawa Electric Corp. The main welding line is fully automated. Overall, welding automation including off-line assembly of doors, trunk lids and hoods is around 70%.
* Gaps between key body components have been cut by two-thirds to one-fourth.
* Meanwhile, jig weight has been significantly reduced. Previously, the "complete front" jig weighed 6,225 lbs. (2,830 kg). That's been trimmed to 2,640 lbs. (1,200 kg) and Honda plans to lighten the unit further to around 1,870 lbs. (850 kg).
Similarly, the "side panel" jig, which was 10,715 lbs. (4,870 kg), now weighs 4,445 lbs. (2,020 kg).
* Main dies are 40% lighter due to simplified design (no weights were given). These include the hood, tailgate and front and rear doors.
* In the paint shop, Honda reduced bodies in process and energy consumption by 25% and 30%, respectively. Meanwhile, labor productivity is up 40%, though no staffing figures were available.
* Takt time for paint application is 47 seconds; it is 52 seconds for sealing. Moreover, the number of processes has been reduced from seven to five.
* By adopting general-use carrier designed with common "pickup" points, the shop can accommodate all models in Honda's car lineup. Flexible design eliminates the need for new equipment - thus investment - when a new model is introduced. Meanwhile, the unit's small body mass and light weight (at 550 lbs. [250 kg], half the previous units' weight) contribute to energy savings as less heat is absorbed by the carrier's steel frame. n The decision to convert to water-borne paints for middle and outer coats cuts volatile organic compounds by 75%. Honda says all of its plants will be converted to water-borne paints within five years.
* In final assembly, No. 1 line automation, at 7%, is half the level of the newer No. 3 line, now estimated at 14%. When the No. 3 line opened 11 years ago, the automation rate stood at 18%.
* Meanwhile, Honda reduced the number of assembly tasks in which line workers are placed in awkward or uncomfortable positions by 80%.
About the Author
You May Also Like