Manufacturing Flexibility Key to Honda’s Surprising 3Q Profit
Despite media headlines claiming Honda’s fuel-efficient cars led to a surprising third-quarter profit, its flexible plants deserve at least 50% of the credit.
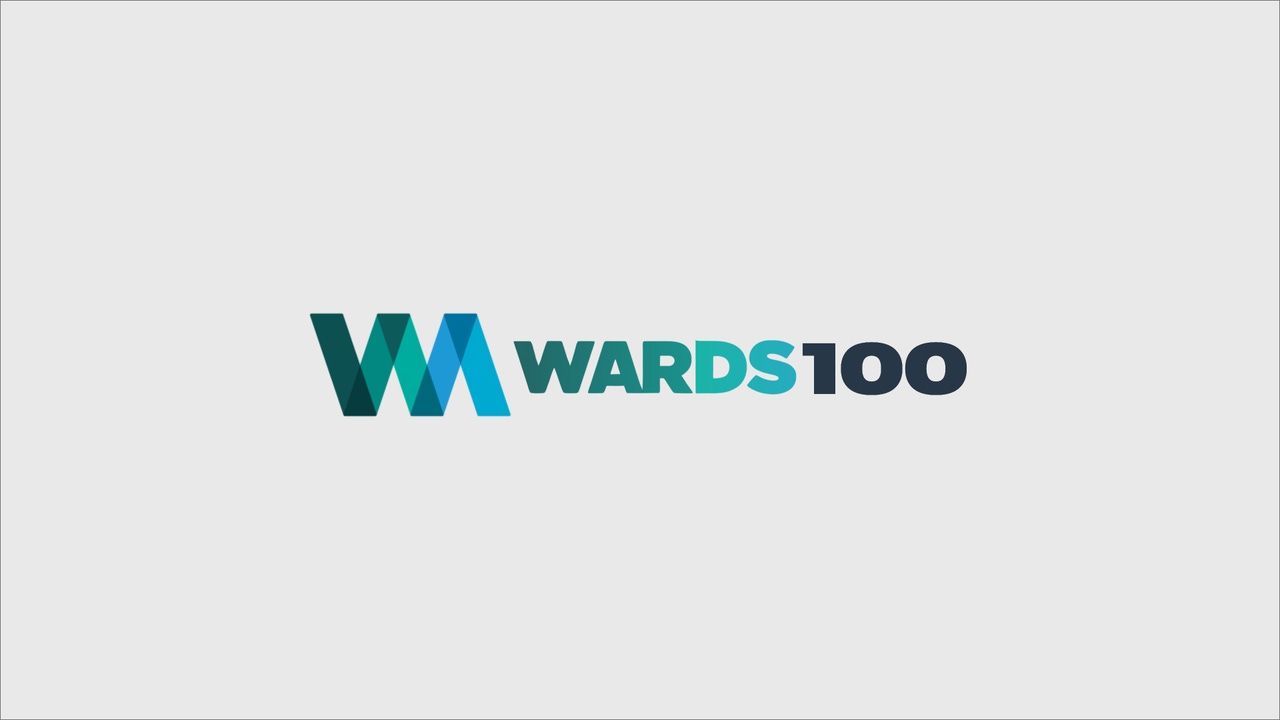
Commentary
Great products drive success and profits in the auto industry, but for once the cars may be getting too much credit.
With U.S. vehicle sales sluggish and getting slower, Honda reported a surprising 38% rise in earnings for its fiscal third quarter. Headline writers across the globe credited the auto maker’s lineup of fuel-efficient cars, but they were at best only half right.
Honda’s flexible and efficient manufacturing operations deserve the other 50% of the acclaim.
In the over-capacitized North American market, where it sells nearly half of its vehicles, Honda’s factories punched out a record number of cars and trucks in 2007. Four of its six plants in the region turned in all-time production records.
That would not be impressive if every single one of Honda’s products were flying out of dealer showrooms, as news reports have suggested, but they aren’t.
Like every other auto maker, Honda has its share of disappointments, products languishing at the end of their product cycle and downright duds. The Ridgeline pickup and most of Honda’s light trucks are not selling well; most Acura models saw sales slip; and the Accord Hybrid is kaput, to name only a few less-than-stellar performers.
What has gone unrecognized is Honda’s skill at juggling the production of its hits and slow-sellers among its six North American assembly facilities in a way that keeps plant-utilization rates soaring.
Last year, Honda launched an all-new Accord and added production of two cross/utility vehicles: the hot-selling Honda CR-V at the East Liberty plant and the so-so Acura RDX at the Marysville facility, both in Ohio.
Honda also shifted production of the Honda Pilot CUV from Alliston, ON, Canada, to Lincoln, AL, making Alabama the sole source for both the Odyssey and Pilot and bringing the plant to its full capacity of 300,000 vehicles and engines per year.
That enabled Honda to meet increasing demand for fuel-efficient Honda Civics by adding Civic output to Alliston Plant 2, which also assembles the slower-selling Honda Ridgeline pickup and Acura MDX CUV.
It was the first time the Canadian plant had built passenger cars since beginning production in 1998.
The global auto industry understands the importance of flexibility, but only Honda and Toyota seem to be implementing it to full advantage.
That’s because it takes years to commonize factories and vehicle architectures so they can be mixed and matched. Only a few auto makers will be there soon.
General Motors, which has been working on globalizing architectures and building plants with similar layouts for more than a decade under the "interbuildability" buzzword, should be able to start taking advantage of the benefits of flexibility in the next several years as all-new vehicle platforms debut.
Other auto makers will follow, but few will be flexible enough to build compact cars and big pickups in the same plant.
In a speech almost six years ago in the U.S., Hiroyuki Yoshino, then the president of Honda, surprised his audience by saying the auto maker had the capability to produce seven or eight models in each of its plants, but it needed to do better. Now we know why.
In a fickle marketplace where fuel prices and an uncertain economy can turn a hit into a miss overnight, manufacturing flexibility may be as important to profits as creating "gotta have" cars and trucks.
About the Author
You May Also Like