Not Done Yet
MARYSVILLE, OH Competing auto makers may begin to shake in their boots when they hear about Honda of America Mfg. Inc.'s next manufacturing strategy. Called BN20, it stands for better in the next 20 years an extraordinary statement from the company whose flexibility and efficiency puts others to shame. Honda, which established its first U.S. plant here 20 years ago, readily admits there was nothing
November 1, 2002
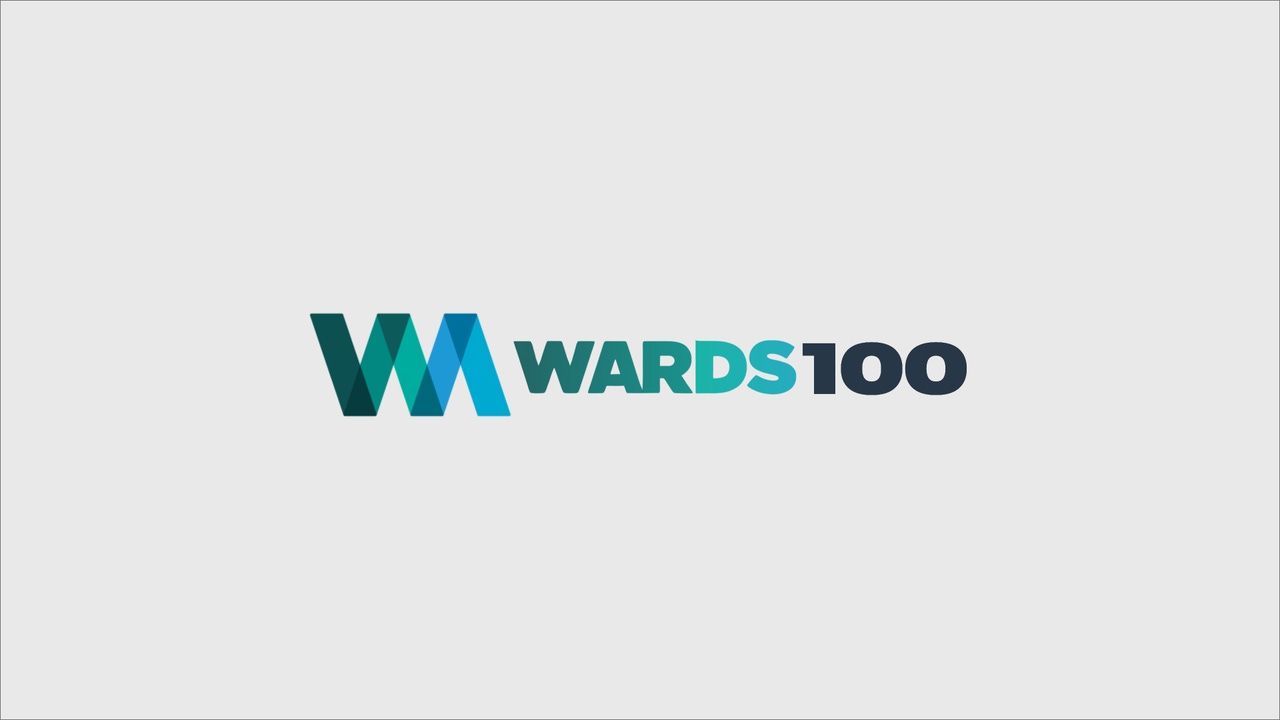
MARYSVILLE, OH — Competing auto makers may begin to shake in their boots when they hear about Honda of America Mfg. Inc.'s next manufacturing strategy.
Called BN20, it stands for “better in the next 20 years” — an extraordinary statement from the company whose flexibility and efficiency puts others to shame.
Honda, which established its first U.S. plant here 20 years ago, readily admits there was “nothing wrong” with manufacturing practices before. Indeed, Honda's North American plants boast high rates of efficiency and are among the world's most flexible.
But with kaizen, an ethic of constant improvement, as a company mantra, a vision for the future always is in place. This vision starts with its New Manufacturing System (NMS), which makes further strides in flexibility, low-cost production and faster line speeds.
Honda's global NMS — which reconfigures the assembly process and incorporates a completely new, highly efficient weld system — isn't a new thing. NMS appeared in North America about two years ago — with the opening of Honda's second plant at its Alliston, Ont., Canada, complex and changeover to the current-generation Civic at the East Liberty, OH, plant. Honda's plant in Lincoln, AL, which began building the Odyssey minivan last November, also has incorporated the new system.
Marysville's time finally came as the plant readied to begin production of a new-generation Accord for '03.
“These major changes will take flexibility to a new level,” says John Adams, senior vice president and general manager of the auto business unit at Honda of America Inc. “We will have the ability to introduce new products more quickly — and at a lower cost — as the needs of our customers change.”
But in converting Marysville to NMS, Honda saved the oldest and therefore most difficult North American auto manufacturing facility for last. It also is the largest, with annual capacity of 440,000 units.
Both time and space proved to be major constraints at Marysville. Honda vowed to pull off the job — which included a complete reconfiguration of the assembly layout and replacement of all welding robots — without ever ceasing production of the '02 Accord.
Another self-imposed mandate: no unnecessary expansion of the already-tight facility, which now registers 3.5 million sq.-ft. (325,150 sq.-m).
“Continuous expansion has taken up most of the space in the plant,” says Randy Shiplett, Marysville's BN20 project leader. In the end, the only new construction was for a bumper paint shop.
Shiplett calls the scope of the project huge, involving 55 major tasks and relocations, performed in the 2-line plant over the last two years. Many of the tasks prompted Honda to get more innovative, creating space by reducing inventories, rearranging things, combining processes and shortening reaches. An old conveyor was modified to move instrument panels, and one underutilized stamping line was sold to create more floor space.
Much of the work focused on the weld lines, which now are standardized at Honda facilities across the globe. The new weld procedure involves programmable electric, non-hydraulic robots. These robots can be “re-taught” with software instead of retooled when new models are involved, greatly reducing time and capital investment.
The new system required an installation of four new major welding zones on the plant's two weld lines and modifications to the door weld lines. Because there was no room for expansion, Honda took an alternating “build and scrap” approach to changes within the weld department.
Honda admits to taking an unconventional approach when it came to pouring concrete. Aisles were too narrow for cement trucks, so Honda settled on using a bucket brigade, carrying small quantities of cement via skid loaders equipped with buckets — which allowed the auto maker to maintain production of 1,800 cars daily.
The plant also was rearranged into a 5-zone “global standard layout,” which lumps similar manufacturing processes for all models into certain areas. This increases flexibility, enables vehicles to be built at any number of Honda plants and puts into effect a new quality gate system — one at the end of each zone.
Making room for the quality gates required extending the lines by 400 ft. (122 m), which Honda officials still view as a near-impossible feat. The final 100-ft. (30-m) stretch, which involves three levels of conveyors, had to be achieved during the 9-day window of Honda's December shutdown in order not to impact production.
“Gossip started circulating in the surrounding communities that (Marysville) might not resume production on Jan. 2 as scheduled,” Shiplett says. “Some area businesses were telling their customers that they were anticipating a few extra days of business from an extended shutdown.”
Despite the time crunch, the new car body conveyor was functional by 4 p.m. on New Year's Eve.
Honda officials say the implementation of NMS is just one key step in their plan to be “better in the next 20 years.” Changes will be made in coming years to the main paint lines and door sub-assembly areas and to add more points of delivery.
Says Shiplett: “We are on our way to achieve our goal of becoming better in the next 20 years. But we are not done yet.”
Read more about:
2002About the Author
You May Also Like