Auto Plastics Supplier Expanding in Mississippi
Hyundai and Mercedes-Benz are among auto makers in the U.S. currently using Sabic polymers and composites in production at their vehicle assembly plants in Alabama.
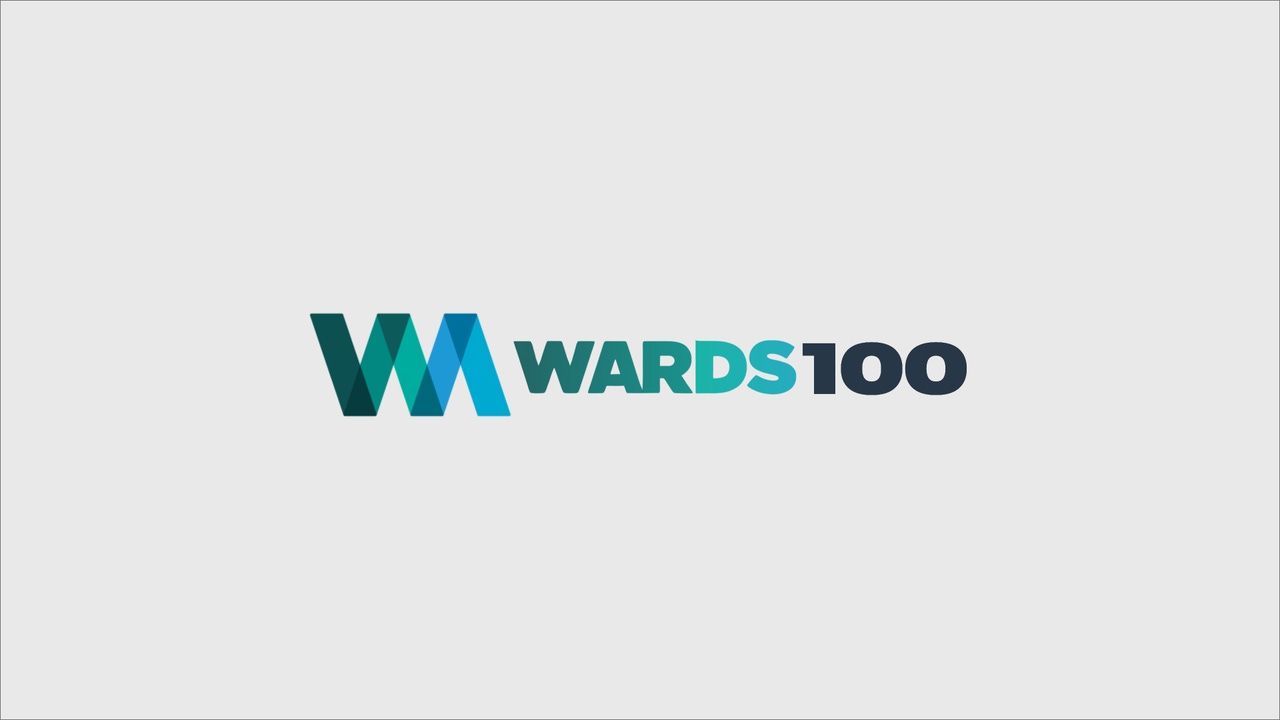
WIXOM, MI – In another sign the U.S. auto industry is creeping into recovery, Pittsfield, MA-based Sabic Innovative Plastics announces this week it is adding capacity at its Bay St. Louis, MS, plant early next year.
Advanced automated processes for producing polypropylene (PP) compounds and long-glass reinforced composites currently produced in Europe will be installed at the facility, although additional bricks and mortar will not be required. Some new jobs will be added, but officials decline to say how many.
A typical light vehicle has 331 lbs. (150 kg) to 364 lbs. (165 kg) of plastic, and PP’s share is growing because designers are becoming more familiar with its special capabilities, says Greg Adams, Sabic vice president-Automotive.
Tough new carbon-dioxide emissions standards in Europe and corporate average fuel economy rules in the U.S. also are sparking OEM interest in all types of lightweight materials.
Adams says PP compounds increasingly are being used in place of other types of resins for bumper fascias, instrument panels, door panels, interior trim and other applications, while so-called long-glass reinforced PP composites are growing because of their combination of strength, dimensional stability and ability to be molded into thin-wall structural parts.
Long-glass reinforced structural composites are made by combining PP base resin with glass fibers that are much longer than conventional glass reinforcement fibers, which are chopped up and less than 1-in. (2.54-cm) long.
The longer reinforcing fibers provide higher strength and 10% to 25% lower density than traditional short-glass materials. They also provide a better surface finish and permit better flow during molding, which allows thinner-wall parts and permits color to be molded-in rather than painted on.
Long-glass structural composites are gaining acceptance for use in front-end modules, instrument-panel carriers, door modules, tailgates and seating systems, Adams says.
Sabic ships polypropylene polymers and composites to Mercedes-Benz plant in Alabama for use in ML350.
Hyundai Motor Co. Ltd. and Mercedes-Benz are among the auto makers in the U.S. currently using Sabic PP polymers and composites in production at their vehicle assembly plants in Alabama.
Making the plant-expansion announcement at Exatec LLC, Sabic’s wholly owned subsidiary here in suburban Detroit, Adams and other Sabic executives also tout the benefits of replacing conventional car and truck windows with polycarbonate (PC) plastic glazing, which Exatec produces.
Exatec is developing plastic sunroofs and rear windows that weigh 50% less than comparable glass windows. Exatec CEO Dominic McMahon says the insulating properties of PC also can improve fuel efficiency significantly by reducing air-conditioner use on hot days.
PC glazing’s insulating capabilities are significant enough to increase the range of an electric vehicle up to 5%, McMahon says.
Despite the benefits of PC glazing, auto makers still have concerns about weatherability, scratch resistance and noise, vibration and harshness issues. Acceptance has been slow.
Sabic Innovative Plastics is a wholly owned subsidiary of Saudi Basic Industries Corp. and was founded in 2007 with the acquisition of the former GE Plastics.
About the Author
You May Also Like