Attacking BlindspotsAttacking Blindspots
Teenagers in drivers training classes learn not to lurk in the “blindspot,” that area beside and slightly behind a vehicle that is hard to see with conventional side-view mirrors.
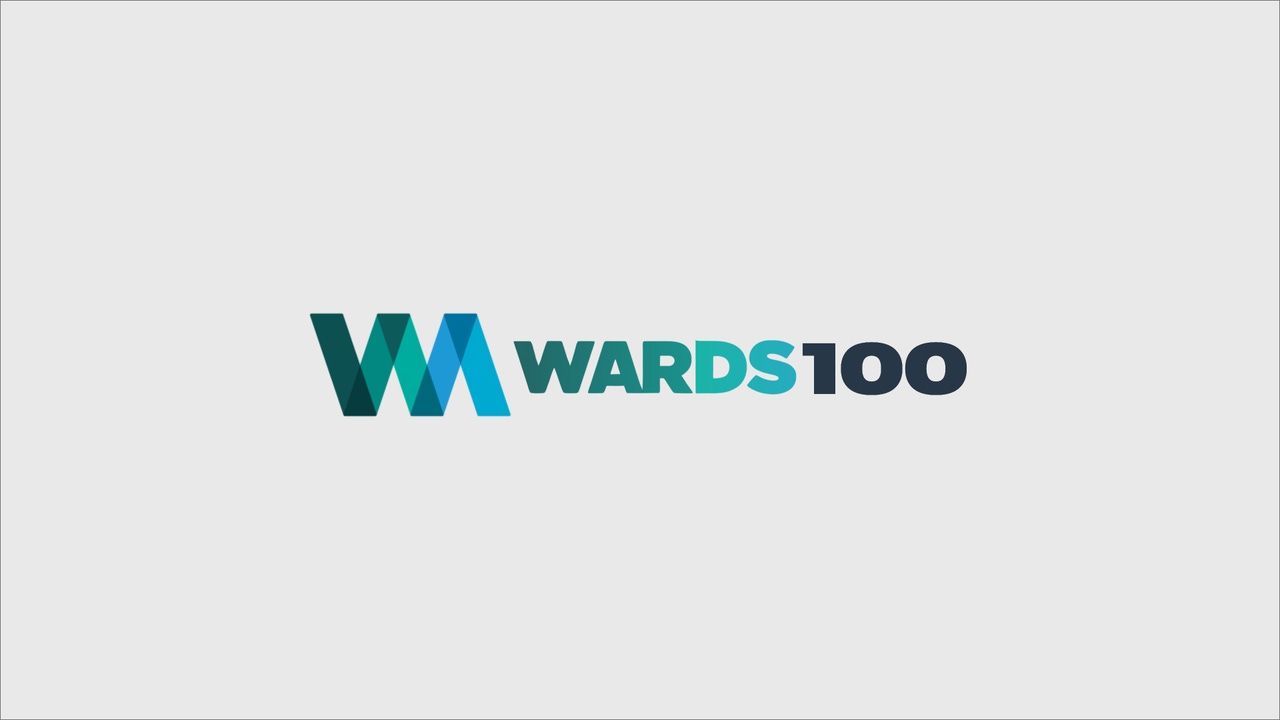
Teenagers in drivers training classes learn not to lurk in the “blindspot,” that area beside and slightly behind a vehicle that is hard to see with conventional side-view mirrors.
A sudden maneuver by a driver who thinks the lane is clear and the neighborhood bump shop wins some new business, not to mention the potential for injuries.
Magna International Inc. is attempting to redefine the blindspot, as today's larger vehicles present unique vision challenges for drivers. Behind, beside, in front of and even inside the vehicle are “blindzones” the driver never sees.
The supplier from Aurora, ON, Canada, has a new, multi-faceted product strategy that offers new vision options for drivers who are increasingly challenged to keep their eyes on the road ahead, while being aware of their surroundings.
In January, Magna introduced its Total BlindZoneManagement (TBZM) suite of products at the Consumer Electronics Show in Las Vegas. The strategy springs from the company's electronics unit and from Magna Donnelly, the industry's No.1 mirror producer. Magna acquired Donnelly Corp. of Holland, MI, in 2002.
Crash statistics confirm the need for TBZM, Magna contends. Every year, children are injured or killed by vehicles that are backing up. With the proliferation of pickups and SUVs, the problem has grown worse. Non-crash accidents have killed more than 1,000 children since 1999, the National Highway Traffic Safety Admin. reports.
Ultrasonic and radar sensors placed in the rear bumper are commonly used to detect objects behind a vehicle.
But the systems are not failsafe. Snow and ice can activate the sensors, which trigger an audible alarm, says Charon McNabb, senior product manager-Mirrors Americas at Magna Donnelly. Drivers in a hurry may ignore the alarm and assume the sensors are merely covered with snow or ice.
The only way to know for sure if an object is behind the vehicle is for the driver to see the area. Magna refers to NHTSA comments that the primary responsibility for object detection rests with the driver. Drivers need “visual confirmation that the pathway is clear,” a NHTSA spokesman says. “Non-visual systems, by their nature, cannot provide such confirmation.”
A growing number of vehicles, including some of General Motors Corp.'s new fullsize SUVs, offer camera-based rear-vision systems to address the problem.
A camera in the liftgate scans the area behind the vehicle, and the wide-angle image appears on a liquid crystal display (LCD) screen on the instrument panel.
Magna's solution uses a CMOS (complimentary metal-oxide semiconductor) image sensor, while others in the marketplace use CCD (charge-coupled device) sensors.
CCD sensors have been around longer but consume more power than CMOS sensors and are more expensive to manufacture. A growing number of consumer electronic products, namely digital cameras, are using CMOS sensors.
Likewise, Magna is banking on the auto industry to migrate toward CMOS imaging technology for camera-vision systems in the future, and the supplier says it has several customers that plan to use its solution.
For '07, Magna began supplying its CMOS system for the Hummer H2 SUT, housed in the rear bumper. The device is optional on the H2, and a 3.5-in. (9-cm) full-color display is integrated in the rearview mirror.
When the driver shifts into reverse, the video display automatically deploys from the side of the mirror, giving the driver a view behind the vehicle, both day and night. Once the vehicle is shifted into drive, the video display retracts back into the mirror.
Magna also supplies the rear vision system for the Fiat Ducato work van. The CMOS camera is packaged in one of the rear cargo doors, and the display folds down from the overhead console.
Magna Electronics produces the CMOS cameras for both the Hummer and Fiat programs.
Display options are numerous. Besides folding down from the overhead console or from behind the rearview mirror, Magna's rear-vision system also can be displayed on LCD screens, which are becoming common in vehicles for controlling audio, climate, navigation and other functions.
A fourth option — a clever way to add value to its Magna Donnelly product line — is Display on Demand, which overlays the image on a small portion of the rearview mirror.
Research by Magna suggests the vast majority of drivers prefer the display in the mirror, McNabb says.
Rear-vision systems are designed to enhance safety, but they also can instill a false sense of security.
Recent test drives by Ward's editors of production vehicles equipped with rear vision systems, including the GM SUVs, have caused near accidents because the view projected on screen suggests drivers have more room to back up than they actually have.
This distorted perspective results from the “fish-eye” effect that auto makers and suppliers struggle to correct with the new optical devices.
Dan Harris, director-Driver Assistance Business Line at Magna Electronics, says the supplier's latest iteration of rearview camera vision corrects much of the fish-eye effect by flattening the image to make it appear more natural and truer to perspective.
The new system also uses a smaller camera, is less expensive and allows for graphical elements to be laid on top of the image, such as guide lines to aid in parking, Harris says.
Magna has a Mazda CX-7 demonstration vehicle, with a factory-installed CCD rear-vision system. The image is displayed in the center console. For comparison, Magna engineers installed their own latest-generation rear-vision system in the vehicle as well.
In a test drive, the Magna CMOS system provides a slightly clearer, more realistic view of the area behind the vehicle, but the perspective still appears a tad askew.
Beyond rear vision, Magna uses other solutions as part of TBZM.
Its BlindZoneMirror has a special convex lens attached to either side-view mirror to expand visibility of the traditional blindspot area beside the vehicle. While radar-based lane-change sensing systems can cost $500 or more, McNabb says the BlindZoneMirror would be available at a fraction of the price.
Inside, the BabyVue camera system allows drivers to see infants and toddlers in rear car seats. Donnelly first showed the device at the Specialty Equipment Market Assn. show in Las Vegas in 2000.
In front of the vehicle, Magna offers its CornerVue camera system, integrated in the bumper to let drivers see around corners. The device, well suited for urban areas, helps drivers creep forward from between two parked cars and through narrow alleys.
Magna's predictive front lighting also uses a forward-facing CMOS camera to help headlights anticipate and respond to curves in the road at night. Headlights also switch automatically to high beams when opposing traffic is absent.
Magna begins production this year for three intelligent headlamp control programs. The system works with headlamps from Magna or any other lighting manufacturer.
Breed reborn, profitable as Key Safety Systems
Breed Technologies had one foot in the grave in 1999 when it landed in bankruptcy well before it became a widespread trend among automotive suppliers.
Company founder Allen Breed pioneered the mechanical crash sensor that gave rise to airbags, but the Lakeland, FL, supplier could not invent its way out of trouble.
Breed stumbled badly under a heavy debt load after its 1997 acquisition of AlliedSignal's safety restraints business, for $710 million. Creditors and customers called for change. At one point, Breed tried to reform itself as a minority enterprise to take advantage of new funding sources.
A group of creditors eventually rescued Breed from Chapter 11 in 2000 by exchanging debt they held in Breed for equity ownership until Carlyle Management Group, led by businessman B. Edward Ewing, acquired the Breed operations in 2003, restructured and renamed the company Key Safety Systems Inc.
Today, Key has a new lease on life, a new headquarters in Sterling Heights, MI, a sharp focus on engineering innovation and a global strategy bolstered by new manufacturing operations in low-wage regions of the world.
“The company has changed quite a bit,” says Ronald Feldeisen Jr., Key Safety's vice president of North American sales and marketing. Feldeisen speaks from experience, having spent 20 years with the operations, dating back to AlliedSignal ownership.
“We have a cost-management focus today,” Feldeisen says, “and we have filled out our product portfolio, invested significantly in new operations and improved dramatically on customer satisfaction.”
Key Safety remains privately held, and Carlyle has since changed its name to Ewing Management Group. Without disclosing details, Feldeisen says Key Safety has been profitable each year since the 2003 acquisition, and he is upbeat about the future.
The former Breed relied heavily on Detroit auto makers for airbag and seatbelt sales, but today Key Safety has 150 customers and 10 that Feldeisen describes as “significant.” No single customer represented more than 20% of Key's $1.1 billion in 2006 sales.
Since the 2003 acquisition, Ewing Management has invested about $250 million in new facilities and product development for Key Safety, Feldeisen says. In 2006, the company invested 5% of revenue in product engineering and research and development.
Before the deal, Breed had 32 facilities globally. Today, Key Safety has 36, including new low-cost manufacturing plants in China, Mexico and Romania, and 9,000 employees.
Feldeisen estimates 50% of the company's products come from low-cost manufacturing facilities. The manufactured cost at each of the three new facilities is virtually identical.
“If the labor cost is about the same, then it comes down to, where is the end customer for a new product program and where is our available capacity?” he says.
In 2004, Key Safety formed a manufacturing joint venture with Yanfeng Visteon Automotive Trim Systems Co. Ltd., based in Shanghai and one of China's largest producers of steering wheels and interior trim.
Last year, the relationship was expanded to include Key Safety's new manufacturing and technical center near Shanghai in the Pudong region. Plant managers plan to produce 5 million airbag modules, 2 million seatbelt assemblies and 2 million steering wheels per year.
About 90% of output is for the Chinese market, with the remainder exported to other Asian markets, Feldeisen says. The supplier is in talks with potential U.S. customers interested in sourcing components from Key Safety's Chinese operations.
The technical center at the Pudong campus employs 200 people, many of them dedicated to helping Asian auto makers comply with crash standards in European and North American markets.
Last year, Key Safety formed a strategic partnership with Chery Automobile Co. Ltd. to design and develop safety systems for Chery vehicles so they can be exported to North America and Europe.
Like its technical centers in Sterling Heights and Frankfurt, the Pudong facility has a “HYGE” (hydraulic-controlled gas-energized) dynamic sled for crash testing.
Key Safety intends to produce its most advanced products in China, including the company's latest-generation knee airbag, which began production at the Pudong plant last May for the Audi TT, with three more platforms launching this year, says Robert Block, vice president-engineering and program management.
Some first-generation knee airbags, which have been on the market for about two years, have integrated hard plastic trim that separates from the lower section of the instrument panel at the time of deployment.
Although designed to keep the driver from slipping under the steering wheel, Block says the hard plastic trim can cause leg and knee injuries, rather than prevent them. Key Safety's new knee airbag has soft surfaces all around.
Knee airbags are important because they help keep the driver in an upright position, making for better contact with the deploying front airbag, which comes from the steering wheel.
Potential customers are clamoring for the devices in their next-generation vehicles, and Block expects volumes to be significant by about 2009. “We're getting a lot of RFQs (requests for quotation) from OEMs right now,” he says.
As a bonus, the new knee airbag is less expensive for auto makers than the first-generation devices, Block says.
Additional investment now allows for Key Safety to produce internally all the inflators necessary for every airbag the company sells. In the past, the supplier had to purchase many inflators.
A pyrotechnic inflator is a small device that fills an airbag with hot gas in a split second, providing a soft cushion for an occupant subjected to extreme crash forces. Block estimates the inflator makes up about 50% of the value of an airbag module.
Despite the upbeat countenance of its management, Key Safety remains the No.4 player in the global safety systems market, behind Autoliv Inc. (which holds about 35% of the market), TRW Inc. and Takata Corp. (each holding about 25%), Feldeisen says.
He estimates Key Safety has between 8% and 10% of the sector.
Despite winning new business, Key Safety also has failed to retain contracts for new vehicles, soon to launch, including the Chevy Malibu and Chrysler Group minivans.
“Incumbency is not high in safety restraint systems,” Feldeisen says. “There's a lot of moving around in terms of business. Technology changes from generation to generation,” leading auto makers to shop regularly for something better, or less expensive.
“We're all quoting new business,” Feldeisen says of safety suppliers.
— By Tom Murphy
About the Author
You May Also Like