Back to the Future And a glimpse at what's to comeBack to the Future And a glimpse at what's to come
The Woodward Dream Cruise that took place in August along metro Detroit's famous thorough-fare covered a wide spectrum of cars mostly built since the end of WWII.Looking at these cars as they passed, I got to thinking about the dramatic changes that have taken place in the building of cars.When I started in this business, almost 50 years ago, car bodies were assembled on body bucks fastened to dollies
November 1, 1999
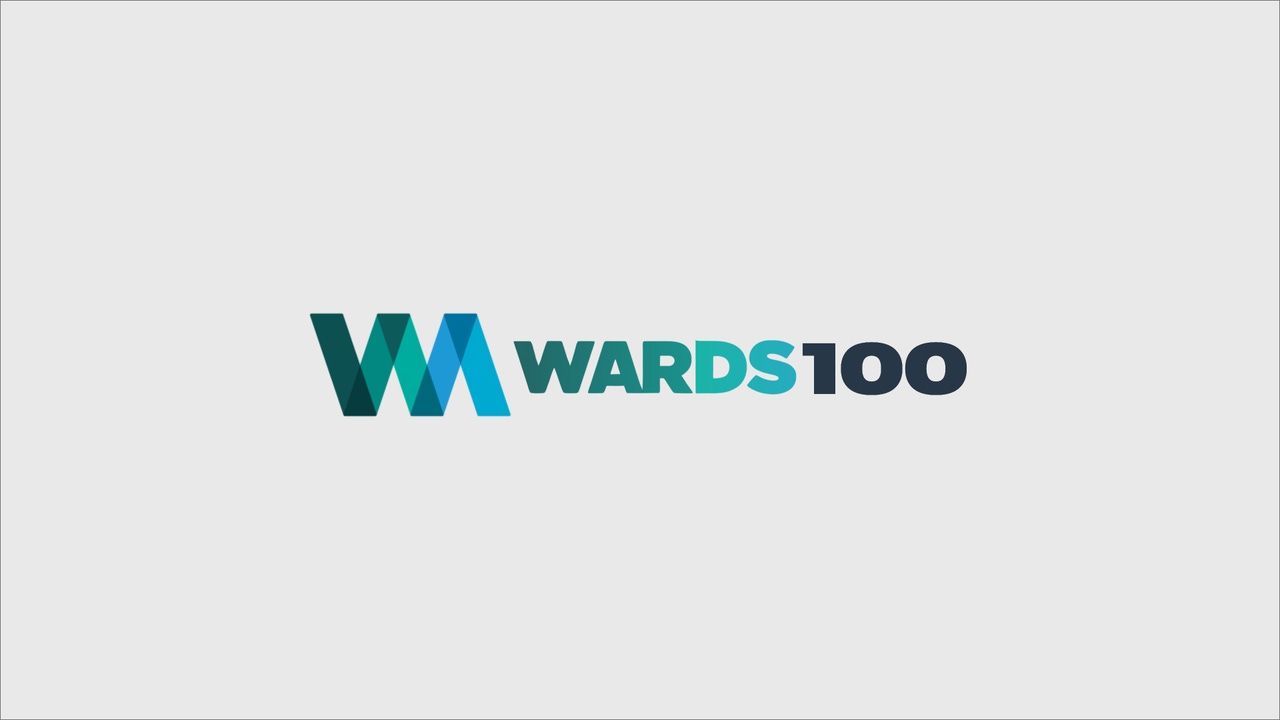
The Woodward Dream Cruise that took place in August along metro Detroit's famous thorough-fare covered a wide spectrum of cars mostly built since the end of WWII.
Looking at these cars as they passed, I got to thinking about the dramatic changes that have taken place in the building of cars.
When I started in this business, almost 50 years ago, car bodies were assembled on body bucks fastened to dollies dragged from station to station by a conveyor. Sheetmetal stamped parts were clamped in these bucks and welded together. Body openings, (for doors, hoods, deck lids) dimensionally, were very poor by today's standards, but at the time this situation was acceptable.
Body parts were welded using large heavy gunwelders maneuvered by big muscular men with sparks flying all around them. While this may have been very photogenic, it was hard, sweaty work.
Then there were the door hangers. They were artists with a mallet, and they all looked like weightlifters. Fitting a door to its opening required prying, wedging, hammering, twisting and cussing to get the door to fit.
Any imperfections, dents or scratches on the sheetmetal were filled in with hot solder and smoothed by filing and sanding.
The body-in-white then went into the paint facility. Here again, paint was sprayed manually, and the quality was very inconsistent.
In those days, making production had the highest priority. If there were problems, the bodies were shoved off into repair holes. Stopping the line was never an acceptable option. Cosmetic problems weren't given much attention unless they were really bad.
Powertrain items were built and installed with about the same degree of handwork. Each assembly plant subassembled its own doors, hoods, deck lids, seats, etc.
Back then, there was no real corrosion protection, and after four or five years most cars began to look like Swiss cheese.
By today's standards there weren't too many good things about this system. But there was one advantage: Since everything was largely manual, it wasn't difficult to make changes. Consequently, the system could easily accommodate front-end changes that were usually made every year.
Because changes were made that often, a plant manager really could make a name for himself by making a changeover with the minimum loss of production.
Minor problems were not a major concern during changeover, and for the most part they were passed on to the dealer to be corrected. The dealer only made fixes after the customer complained. Customers made a list of things for the dealer to fix, after the car had been driven for awhile. A while later it was time for another dealer visit with another fix list. This would go on until - hopefully - everything got fixed.
As time went on, automation and robots replaced the back-breaking manual labor.
This brought a large reduction in manpower, reduced costs, and a big improvement in quality. Today the quality is so good that a customer can pick up a car and not see the dealer again until he gets his first oil change.
Things will continue to improve for both automakers and customers. With an eye on the future:
n I think it's a safe bet that some kind of fuel cell eventually will replace the engine.
n Higher strength steel will be developed, making it possible to reduce the thickness of steel used in bodies, resulting in lighter cars.
n Aluminum and plastic components will continue to improve so that they can be used for hoods, decklids, and even underbody parts.
n Safety devices such as sensors will warn the driver to slow down if another car or object gets too close.
n More autonomy will be given to the assembly plants and divisions to operate like outside suppliers. This will reduce the stifling effect of the current bureaucratic corporate staffs. The responsibility to operate like entrepreneurs will free up component plants to become more innovative, creative and, consequently, more competitive.
In spite of all of the automation, robots and computers, to be successful in the future carmakers will have to allow their people to be free to be innovative and creative.
Read more about:
1999About the Author
You May Also Like