Battling steel: plastics fight uphill battle against more traditionalexterior materials.Battling steel: plastics fight uphill battle against more traditionalexterior materials.
First there was David and Goliath on a Biblical battlefield, then the U.S. and the Soviet Union on an Olympic hockey rink in 1980 and now plastics vs. steel on automotive exterior panels.Steel is entrenched in automotive exteriors because of its history, low cost and ultimate recyclability. Plastics, on the other hand, have weight advantages and certain cost attributes for lower-volume projects. They
September 1, 1996
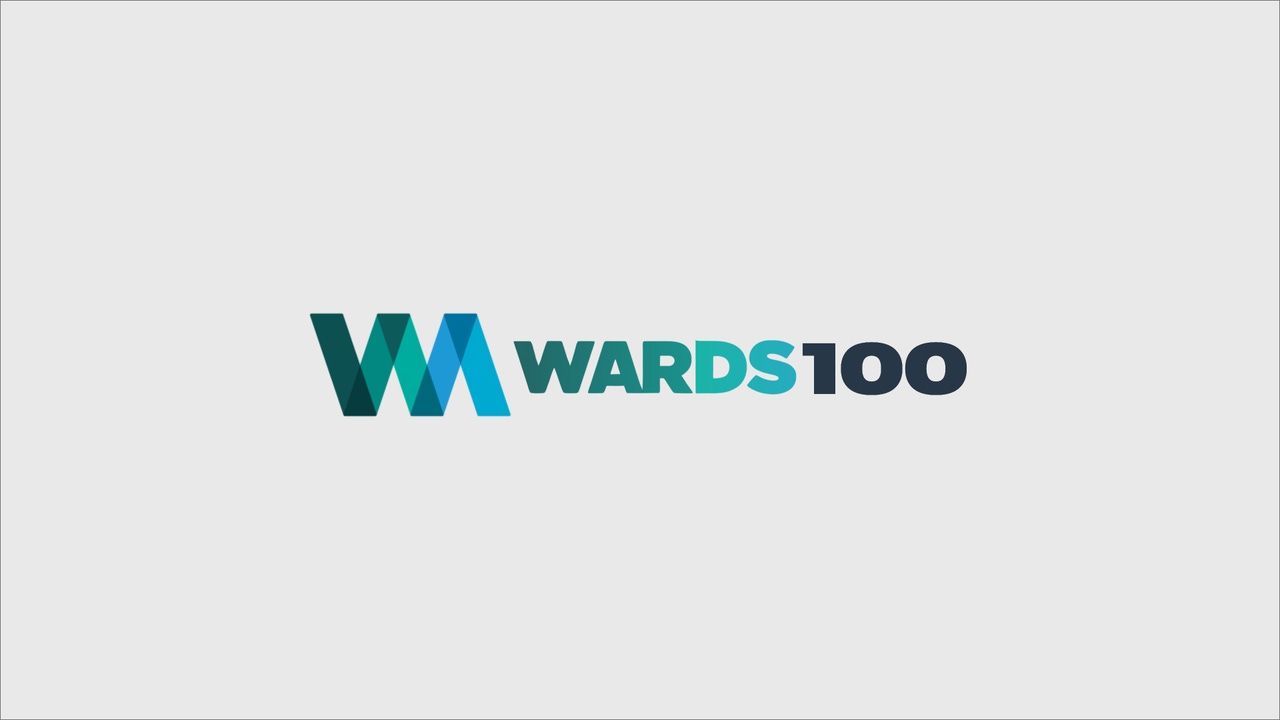
First there was David and Goliath on a Biblical battlefield, then the U.S. and the Soviet Union on an Olympic hockey rink in 1980 and now plastics vs. steel on automotive exterior panels.
Steel is entrenched in automotive exteriors because of its history, low cost and ultimate recyclability. Plastics, on the other hand, have weight advantages and certain cost attributes for lower-volume projects. They also don't rust and are fairly resistant to dents from parking lot altercations. Still, steel is expected to be the dominant material for automotive exteriors through the first decade of the 21st century, accounting for more than 98% of consumption by weight.
So the producers and molders of sheet molding composite (SMC) and thermoplastics do battle in this market against overwhelming odds.
"Right now the biggest change (in exterior plastics) is the growing popularity of the thermoset SMC material, which is primarily because of its dimensional stability compared to thermoplastics," says James R. Best, president of Toledo-based Market Search Inc.
The SMC Automotive Alliance (SMCAA) reports there are more than 90 new SMC components on 29 of the '97 model year cars and trucks, a 29% increase compared with the '96 model year. SMC already is used for more than 375 components on nearly 130 domestic and import vehicles produced by 29 automakers.
Even with General Motors Corp. moving from SMC to steel for 1997 minivan body panels, SMC producers project a 5% jump in the pounds of material used by automakers in 1997. Much of the increase is in heavy duty trucks, which represent 31 million lbs. (14,000 t) -- more than half of the total. Some 10 million lbs. (4,500 t) of SMC are used on passenger cars and approximately 5 million lbs. (2,300 t) on light trucks, vans and sport/utility vehicles (SUVs).
Some early predictions from the trade group show that about 250 million lbs. (114,000 t) of SMC will be used by automakers in 1997, up from 240 million lbs. (109,000 t) in 1996. And if 1997 sales targets are met, SMC use for automotive applications will have increased 65% since 1993. SMCAA predicts that the auto industry will increase its use of SMC at a 3.4% a year clip to 300 million lbs. (136,000 t) by 2000, with exterior applications accounting for a high proportion of total. New applications are expected to more than offset any losses to steel.
"Much of this growth is because SMC has experienced a dramatic increase in both part size and the number of new structural components during the past two years, combined with an increase in its traditional body-panel market," says Jim Grzelak, SMCAA's chairman and a sales engineer at Eagle-Picher Plastics Div. "Most of the new applications are exterior panels."
Notable new SMC components on '97 models include significant content on vehicles touting their use of aluminum. The hood, doors and decklid assemblies, roof (30% of the panels), drain-channel surround and roof side rails for GM's EV1 electric car are made of a new low-density SMC. The Plymouth Prowler has SMC rear quarter panels, front fenders, front quarter extensions, windshield surrounds, rear valance panels and fuel-filler doors.
Also, the first use of colored SMC, which eliminates the need for paint, is featured on the Jeep TJ's roof assembly. GM's next-generation Corvette will have rear fenders and door panels made of GenCorp's Flexion flexible SMC, a first for the automaker.
Other new SMC parts in 1997 include:
* Grille-opening reinforcements for Ford Contour/Mercury Mystique, Buick Regal/Oldsmobile Cutlass Supreme and Ford Windstar;
* Valve covers for 5.4L Ford F-150/250 pickups;
* Fender extensions and a rear applique on Ford Escort/Mercury Tracer.
"SMC is more dimensionally stable (than thermoplastics) and has come from behind in fender applications," says Mr. Best.
Thermoplastics, however, did have a major victory at GM's Saturn Corp. The new Opel Vectra-based Saturn set to debut in '98 will have fenders made of General Electric Plastics' nylon-modified PPO, and its doors will be of Dow Chemical's polycarbonate ABS. The decision to stick with thermoplastic resulted from consumer research indicating that the dent-resistant material is a key selling point.
"This is the first time an automaker has made a decision on a body panel material because consumers have shown a preference for plastic," Mr. Best observes.
The decline in the use of thermoplastics for exterior panels from 1994 to 1996 reflects Chrysler Corp.'s switch from DuPont Bexloy K to steel for its LH fenders due to higher-than-anticipated volumes. Other losses can be attributed to thermoplastics' tendency to expand and contract in extreme temperatures.
"Once burned, engineers are going to be slow to go back to it," explains Mr. Best, adding that the difficulties with thermoplastics can be fixed by paying attention to design details such as shaping, fastening and gap tolerances. Another problem with nylon-modified materials, says Mr. Best, is that components stored for several weeks absorbed moisture that contributed to problems going through high-temperature paint ovens. "These factors are known now and can be controlled, but at an increase in cost and complexity," he says.
Read more about:
1996About the Author
You May Also Like