Bioplastic Research AcceleratingBioplastic Research Accelerating
Making cars truly sustainable means developing not only new energy sources, but also finding a replacement for petroleum-based plastics. To strengthen plastics, Europeans have been at the forefront of using hemp and linen fibers, among others, to replace glass fibers in composite panels. The two trends came together at the recent JEC European composites show in Paris when CRST SA, a small French research
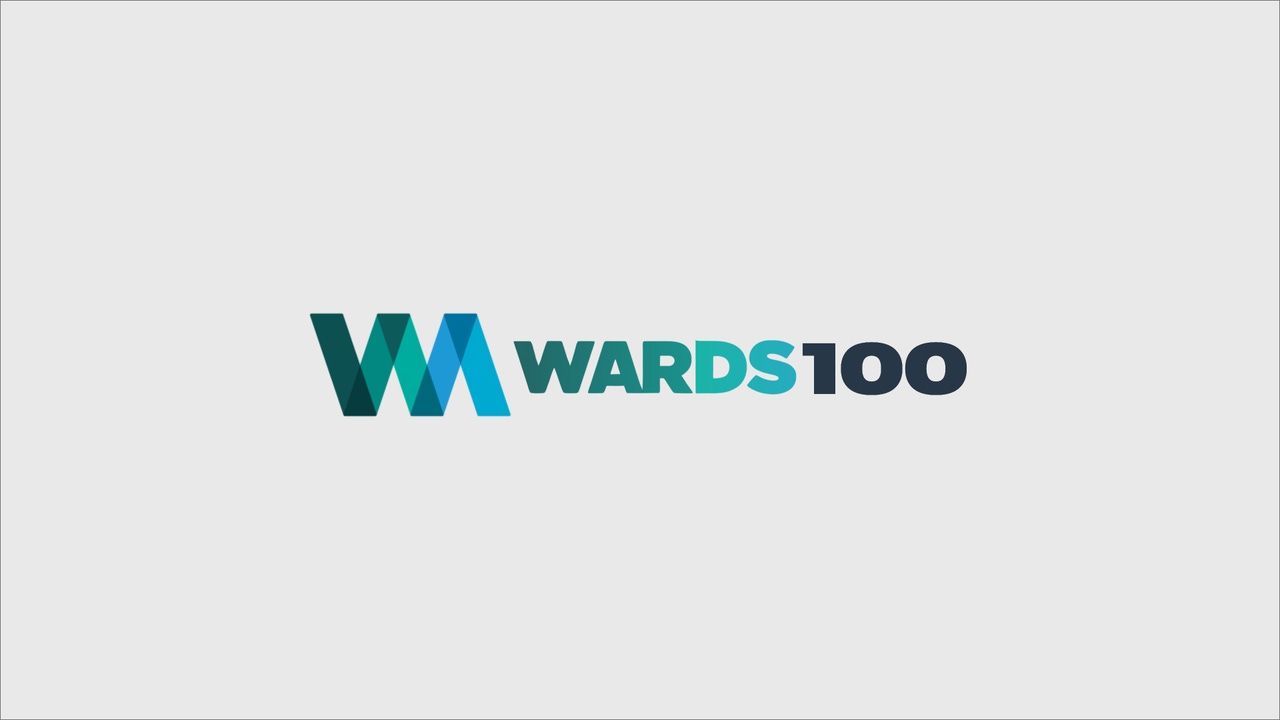
Making cars truly sustainable means developing not only new energy sources, but also finding a replacement for petroleum-based plastics.
To strengthen plastics, Europeans have been at the forefront of using hemp and linen fibers, among others, to replace glass fibers in composite panels.
The two trends came together at the recent JEC European composites show in Paris when CRST SA, a small French research company, introduced an automotive composite in which a thermoformable plastic derived from corn stalks is mixed with linen fibers to make a 100% biological composite panel.
The material has “nearly the same characteristics as a glass-filled composite,” says Tristan Mathieu, research and development director.
CRST is a specialist in aligning fibers for strength, and its composite panel material uses 40% linen and 60% poly lactic acid. PLA is made by the polymerization of lactic acid produced by fermentation of corn starch, and linen is a fiber of growing importance to French farmers, who supply 75% of Europe's linen crop and about half the hemp crop.
Mathieu says CRST has been in talks with PSA Peugeot Citroen and BMW AG, as well as suppliers Valeo SA, Faurecia SA and Treves Group, about using the material in applications not exposed to high heat.
Natural fibers are becoming more common in automotive production. Faurecia, the PSA parts subsidiary, has used natural fibers with normal polymers in compression processes since 1993.
Faurecia says it is the leader in making panels of wood fibers. The company supplies door-panel carriers, for example, for the Peugeot 607; Volvo S60, C70 and V70; Mercedes-Benz CLK and S-Class; and Opel Astra.
At a JEC seminar, Faurecia's Claire Peyrelongue and Laurence Dufrancatel say two improvements are likely this year and next: using natural fibers with plastic injection and improving the natural-fiber mats used in the compression process to be lighter and presentable enough for application in visible parts.
In 2010 or 2011, they say, bioplastics should be ready to pair with natural fibers in both injection and compression processes.
Faurecia is involved in a 4-year project subsidized by the French government to develop renewable composites.
The Matoria project is led by PSA and includes parts makers Valeo and Visteon Corp., as well as material suppliers, universities and research laboratories. France is providing E2.4 million ($3.2 million) or 30% of the project's budget.
“The automobile industry has two challenges to surmount: that of guaranteeing the availability of plastic material while reducing their environmental impact,” writes one of the members of the project, the Institut Superieur de Plasturgie d'Alencon, an engineering university.
“The replacement of fossil resources by renewable resources is one of the options for reducing the impact of polymers.”
The goal is to develop renewable plastics to account for 25% of automotive plastics, aiming mainly at large parts such as instrument panels and bumpers.
The Ecole des Mines at Douai, another engineering university participant in the project, is working specifically with nano materials to improve the properties of bioplastics used in plastic injection.
At the Sustainable Planet trade show in Paris, PSA announced its 10 objectives for sustainable development, of which the second involves using more green materials in the design of Peugeot and Citroen vehicles.
The Group wants to raise the amount of green materials to 20% of polymers by 2011. The average amount of recycled matter or materials of renewable origin was 6% in 2007.
The new Citroen C3 Picasso is the leader so far in the PSA range, with 12% of its material classified as green.
“The double major of agriculture and chemistry is going to be essential in the future,” says Sandrine Raphanaud, director-innovation projects at PSA, including the Matoria project.
Bioplastics have been present for many years in the auto industry, and research is accelerating, especially in Asia and Europe. Henry Ford made steering wheels and experimental body panels from a soybean plastic, and Ford Motor Co. today uses seat foam produced by converting soybean oil to polyol.
The hood and interior parts in the Hyundai BlueWill concept displayed at the recent Seoul Motor Show uses plastics made from plants. Japanese researchers at Toray Industries Inc. and Teijin Group have developed PLA, and Teijin says its version can withstand heats to 410°F (210°C), which gives it more flexibility in automotive processes.
In France, the BIC company has just launched a line of disposable razors using biodegradable bioplastic, and Rouen, a town in Normandy, is spending E1 million ($1.3 million) on a study to develop a Europe-leading 1,200-acre (485-ha) industrial park dedicated to bioplastics with a goal of creating 4,500 jobs in 15 years.
The current economic climate in the auto industry has moved many projects on the shelf for companies trying to conserve cash. But in France, the exceptions are those aimed at sustainable development, Mathieu says.
Renault has not slowed spending on its electric-car projects, and PSA has not backed off its green-car investment.
“The crisis will be over one day, and when it is, a strong point of the market will be sustainable development,” Mathieu says. “We want to be there then.”
About the Author
You May Also Like