Coming Up ShortComing Up Short
It sounds almost nonsensical, but even though the U.S. auto industry leads all industries in layoffs, it soon may face an acute labor shortage. The problem: There is a huge gap forming between the kind of workers and skills currently available and those that will be needed in the future. Some companies already are struggling to find the appropriate skilled workers for their facilities, and the problem
October 1, 2005
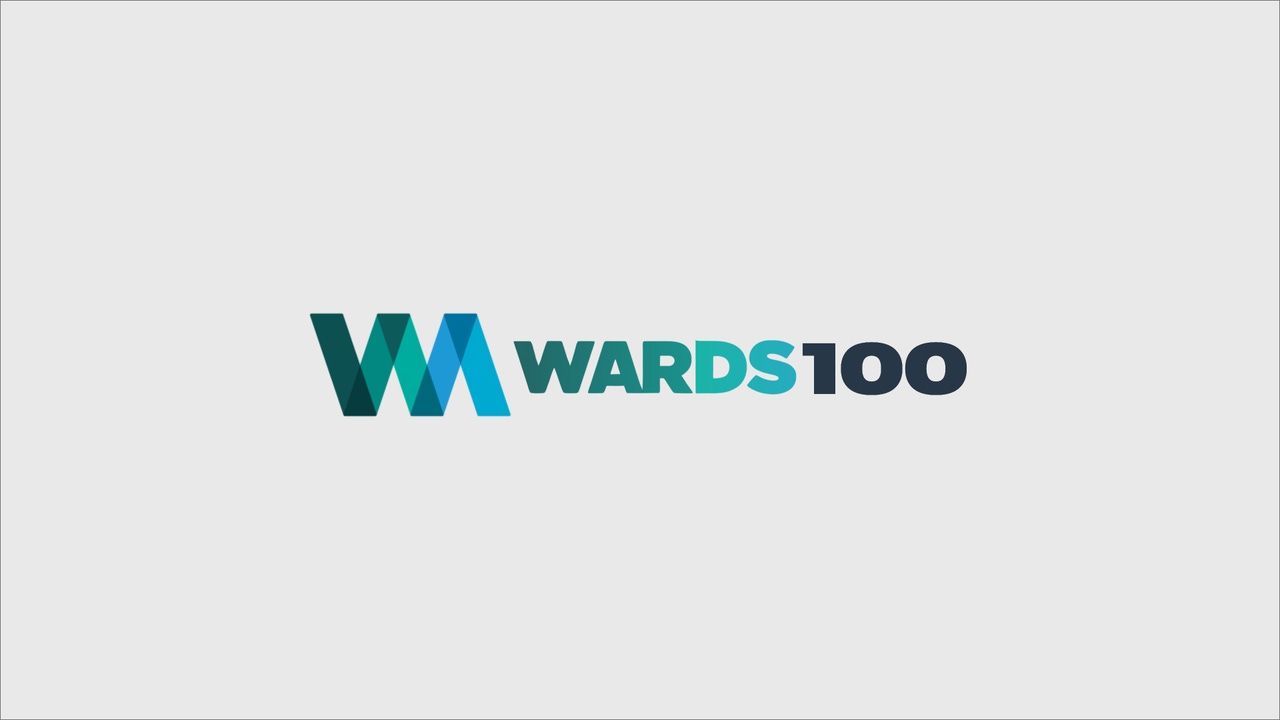
It sounds almost nonsensical, but even though the U.S. auto industry leads all industries in layoffs, it soon may face an acute labor shortage.
The problem: There is a huge gap forming between the kind of workers and skills currently available and those that will be needed in the future.
Some companies already are struggling to find the appropriate skilled workers for their facilities, and the problem only shows signs of intensifying.
Even the largest OEMs and Tier 1 suppliers — those that can afford to offer top wages and benefits — are not immune, and the problem promises to become more troubling farther down the supply chain, where companies already are struggling to compete against low-cost rivals offshore.
Negative perceptions about manufacturing jobs, the availability of low-cost student loans for 4-year college degrees and the migration of a new generation away from blue-collar jobs all are factors forcing the industry to think about courting skilled manufacturing workers instead of just taking their availability for granted.
The burgeoning shortage is crucial enough to prompt new studies by numerous groups, including the National Assn. of Manufacturers (NAM), the Automotive Parts Manufacturers' Assn. and Deloitte & Touche USA. All three have surveys scheduled for release later this fall.
“From plant engineering to tool-and-die workers, the type of skills needed are in short supply,” says Dave Andrea, vice president-business development at the Original Equipment Suppliers Assn. The days of a high school graduate coming out ready for line work are over, he adds.
“There is more initial screening in terms of testing for different types of job skills,” Andrea says. “They want to know overall potential, so these new required skills will be a combination of a high school diploma, proficiency in English, math and general job skills. And employers, both auto manufacturers and suppliers, will want to see strong aptitude for learning.”
Even though new auto-related plants are sprouting in the South, Canada and a few spots in the Midwest, there is little reason for a young person to seek a manufacturing job. There are almost daily media reports on companies eliminating jobs.
According to the outplacement firm Challenger, Gray & Christmas Inc., the auto industry led all business sectors in layoffs with 72,598 expected job cuts through July.
Despite the reductions, the American industrial worker is crucial to boosting the nation's growth far into the future, Andrea says. “The higher value-added jobs will still be here in America,” he says. “Those jobs will have higher skill levels and higher wage levels as well. But there will be fewer of them.”
The new breed of worker is college-trained and has skills that are highly valued on modern production lines. They are comfortable working with robots, sophisticated computerized concepts and complex quality-control systems.
“The key thing is that the definition of a production worker is changing,” says Dave Cole, chairman of the Center for Automotive Research. “When you look at, for example, the DaimlerChrysler (Corp. Global Engine Mfg. Alliance) world-engine plant (in Dundee, MI), the minimum requirement to be employed there is a 2-year degree.”
Richard Kleinert visited factories frequently 20 years ago as director of employee benefit administration at General Motors Corp. But he was shocked at the advances in manufacturing when he toured an auto plant this summer.
“This plant was cleaner, lighter, and most of the jobs relied heavily on technology in one way or another,” says Kleinert, now a principal at Deloitte Consulting. “And the implication is that these workers now have to be tech savvy and have a basic mathematical capability to read diagrams.”
Long gone are the pedestrian skills of line workers past. So too is the vision of a secure 30-years-and-out job. The threat of outsourcing to low-wage countries ended all that.
Like much of the nation's manufacturing sector, the auto industry is predicted to be threatened by a lack of properly trained and educated blue-collar workers.
The market will determine wage rates, Andrea says, with the continued competition between auto makers and suppliers. As heavyweights such as Delphi Corp. continue to slide, “the suppliers will still have to be more flexible in terms of pay.”
For years, manufacturers have warned of 2008 as the year when the first Baby Boomers turn 62. NAM, in an oft-cited report, says during the post-Sept. 11 recession, 80% of manufacturers actually endured a shortage of production workers, machinists and semi-skilled laborers.
“It may seem odd to speak of a manufacturing labor shortage when we have lost millions of manufacturing jobs in recent years,” NAM President John Engler told an audience in February. “But the reality is that our members are telling us they have jobs going begging because they cannot find qualified workers.”
For the auto industry, the shortage is especially tricky due to the age of the industry itself and reliance on old-school methods and talents.
“The younger companies are less concerned about (a worker shortage),” says Kleinert. “I think the Big Three are very mindful of the fact that they will have a lot of people eligible for retirement and leaving in the next five years.”
The potential shortfall of skilled workers is news to some auto makers.
“We have no shortage of workers,” says a GM spokesman. “We pay good wages, and that makes these jobs very attractive. We do all of our training in-house, and (a worker shortage) is not an issue.”
Chrysler CEO Tom LaSorda says his company is working with educational groups as worker demand moves into more technical areas such as robotics and calibration, but adds that the shortage of workers has more impact in regions without a history of manufacturing.
At Ford Motor Co., though, Phil Martens, group vice-president-product creation, says there is a need to invest in and improve the quality of education to ensure there are enough qualified employees “especially in math and business.”
Apprenticeship programs, in-house training and manufacturing vocational programs at community colleges can help fill the void for both regular line workers and skilled tradespeople.
The reduction of employees promoted to company-run apprenticeship programs, which draw their numbers from the ranks of floor workers, has become a negotiating point between the Big Three and the United Auto Workers union.
“Since the companies have been downsizing since the 1980s, they have also cut back on apprenticeships,” says a UAW spokesman. “And at the same time, a lot of the trades people are becoming eligible for retirement.”
Studies show 10 million of these better-educated workers will be needed by 2020 as many retire and few enter the field.
When Toyota Motor Corp. decided to locate its seventh North American plant in Woodstock, Ont., Canada, a contributing factor was the highly praised vocational training programs available in the province.
“Ontario is ahead of the U.S. in these state-sponsored training programs, and that was a huge reason that Toyota recently located in Woodstock,” says Gerry Fedchun, president of the Automotive Parts Manufacturers' Assn. in Toronto. “We have the highest level of education of the states that would compete for something like this, opposed to, for example, Michigan.”
Canadian suppliers have in the past turned down contracts due to a waning workforce, although not as much recently. But even today, overtime is often required to fulfill contracts, Fedchun says.
The new plant, which is slated to open in 2008 and will build the RAV4, also can mine a trained workforce from a Toyota facility in nearby Cambridge, Ont., that will help get the plant going.
“It's about being in the right place,” Ray Tanguay, president of Toyota Motor Mfg. Canada Inc., said last year when the plant decision was announced.
Toyota, however, dismisses claims the auto maker chose Woodstock because the company has struggled to find skilled labor in the southern U.S.
“Canada is a good place to locate, but we have a great workforce everywhere we operate. We located in Woodstock because of its proximity to Cambridge,” says James Wiseman, vice president-corporate affairs at Toyota Motor Mfg. North America Inc.
Wiseman admits his company has witnessed the shortage in skilled labor. “It's becoming more and more severe,” he says.
Toyota is hiring 2,000 people to staff its new pickup truck plant in San Antonio, TX, and its suppliers for the factory will hire some 15,000 workers, Wiseman says.
“So far, Toyota has brought on 60 skilled workers that we found in Texas for San Antonio, and we need to find 40 more,” he says recently. “We're pretty sure we'll have to go nationwide with our search.” Production begins in fall 2006.
Ontario's ability to land Toyota speaks well of the importance of training and how a well-trained pool of workers can benefit a region. The blue-collar worker still must combat a problem of image, which portrays manufacturing as decidedly uncool and unstable.
“These jobs are essential to the economy,” says David Kusnet, a senior fellow at the Economic Policy Institute. “These jobs require great skill, from the production worker to the tool-and-die worker.
“And to not have enough of these people,” he says, “will lead the country to a place it doesn't want to be.”
— with Alisa Priddle and Tom Murphy
About the Author
You May Also Like