Compact Power Nailing Down More Business, Site for U.S. PlantCompact Power Nailing Down More Business, Site for U.S. Plant
CEO Prabhakar Patil is optimistic his company can continue to drive Li-ion battery costs down by a factor of two within five to 10 years.
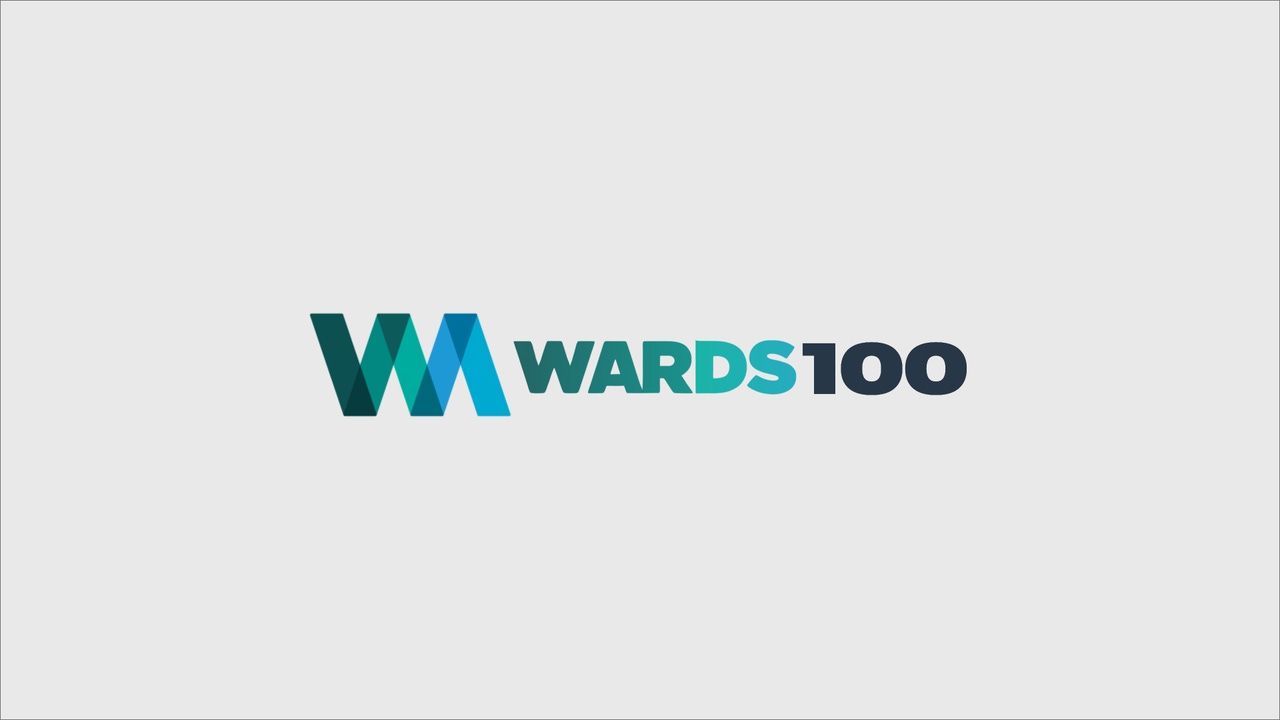
TROY, MI – Compact Power Inc. CEO Prabhakar Patil says the battery-cell manufacturer will ink a deal next month to supply its technology to additional customers and soon reveal the location of its first U.S. plant.
Patil, whose firm has won the contract to supply battery-cell technology to General Motors Co.’s Chevrolet Volt extended-range electric vehicle, says CPI is working on “a couple of items” with other auto makers that he declines to name.
“Next month they should be settled,” Patil says of the future contracts.
In addition to the Volt, CPI will supply pack technology to GM’s second-generation 2-Mode Hybrid system, which originally was scheduled to appear in the Saturn Vue CUV. When the auto maker decided to sell the brand, it moved the new 2-Mode to an upcoming small, Buick CUV that since has been cancelled. The technology now will end up on another product and within the original 2010 timeframe.
Juggling the hybrid application has not affected development work at Compact Power, Patil says.
“The pack doesn’t get affected significantly,” he tells Ward’s during an event at the supplier’s research and development facility here to celebrate receiving a $151 million grant from the U.S. Department of Energy.
In addition to the GM business, CPI announced earlier this month a contract to provide batteries to parts-supplier Eaton Corp., which is taking part in the largest deployment of commercial hybrids to date as part of a $45.4 million plug-in hybrid-electric-vehicle federal grant.
CPI CEO Prabhakar Patil, left, and Engineering Director Martin Klein show Michigan Gov. Granholm a battery-cell module to appear in Chevy Volt.
“Business is good, very good” Patil says, noting employment at the supplier’s site here in Troy has grown from five workers in 2005 to 100 today. “More importantly, we’re securing these production contracts, which help make us a sustainable business.”
Without the recent DOE grant, a slice of the $2.4 billion in federal funding set aside for advanced battery development, Patil says CPI still would have moved forward on R&D in southeast Michigan, albeit at a slower pace.
“This is helping us jump-start the process,” he says, noting the supplier has narrowed the number of sites for its first U.S. lithium-ion battery plant to three Michigan locations.
However, Patil declines to reveal whether the site will be close to GM’s new $43 million battery-pack assembly plant in Brownstown Twp., which is some 20 miles (32 km) south of where the Volt will be produced at the auto maker’s Hamtramck facility near Detroit.
At Brownstown, GM will assemble CPI’s Li-ion cells into a battery pack specially designed for the Volt, due in late 2010 as an ’11 model. Until the facility comes on line in second-quarter 2010, Compact Power will continue to import the packs from parent LG Chemical in South Korea.
Patil says Compact Power would like a centrally located cell-making facility capable of supplying GM and other auto makers. Compact Power’s site will have the capacity to supply between 50,000 and 250,000 vehicles annually.
The plant’s initial customer – the Volt – will only sell about 60,000 units annually during the first generation, so Patil admits it may take some time eat up the plant’s capacity.
Patil says a final decision on the location will come by the end of October. When at peak production, it will employ 400 people.
In the future, he says, Compact Power could supply its own fully assembled battery packs to auto makers from sites co-located with vehicle assembly plants.
“If the volume is more than 50,000 units we will co-locate it with the vehicle assembly plant,” he says. “If it’s less than that we will do it in a central location.”
Patil remains optimistic his company can continue to drive Li-ion battery costs down. When the Volt comes to market, GM hopes to sell it for less than $40,000, but has admitted it will probably take a loss on the vehicle during its first generation because of costly battery technology.
According to the DOE, Li-ion technology costs about $1,000/kWh, which means the 16 kWh battery pack in the Volt would run roughly $16,000.
“I expect to get down by another factor of two in the next five to 10 years,” he says, adding that Li-ion pack costs have dwindled by a factor of 14 since their introduction in 1991. “You can’t keep going down at the same rate, but I’m optimistic we can go down another two factors.”
Michigan Gov. Jennifer Granholm, who is pushing to make her state the center of battery expertise in the world to make up for year dwindling factory jobs in the region, joins Patil and other executives, dignitaries and Compact Power employees to celebrate the grant in Troy.
Afterwards, Granholm’s team left for a clean energy conference at Down Chemical Co. in Midland, MI, roughly 100 miles to the north of Detroit.
About the Author
You May Also Like