Day Pushes Lean to Lower TiersDay Pushes Lean to Lower Tiers
You know lean manufacturing initiatives still have a long way to go when a respected practitioner can identify $100 million of waste within his own company. Joseph Day, chairman and chief executive of Freudenberg-NOK, can even break down the waste: $30 million of it from five companies acquired in the past three years, $20 million still on the shop floor, $10 million in administration and product
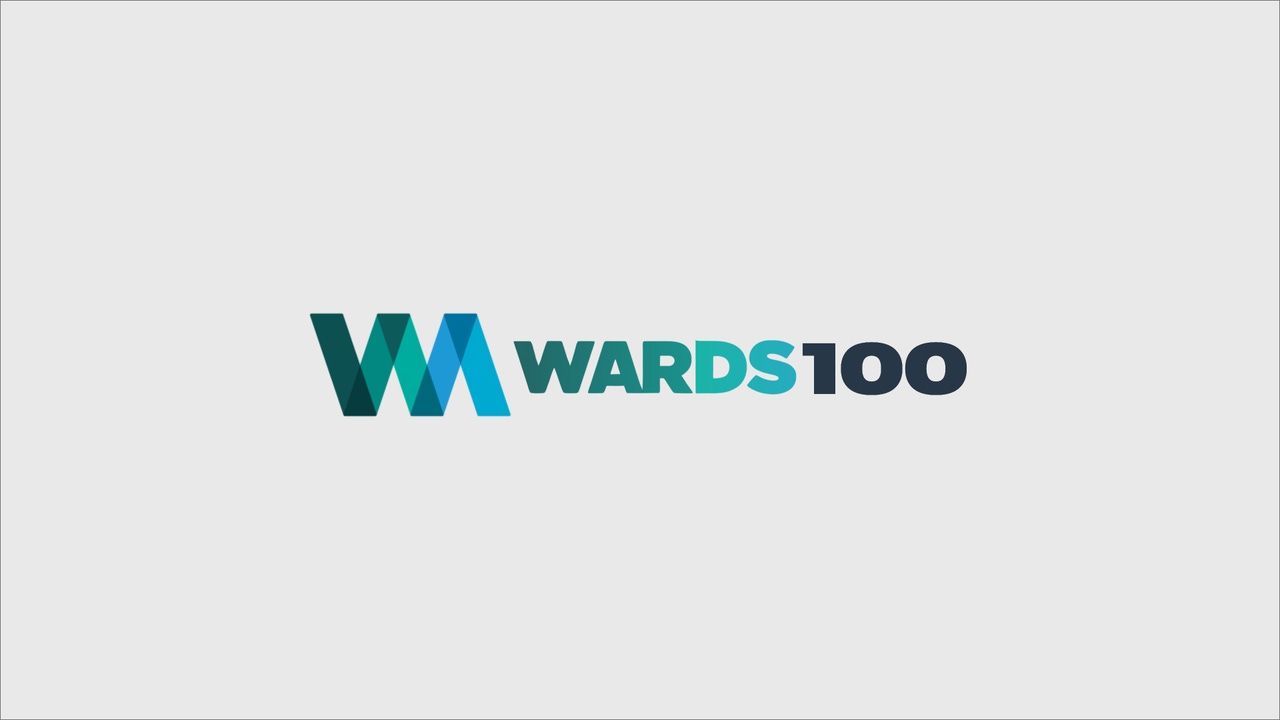
You know lean manufacturing initiatives still have a long way to go when a respected practitioner can identify $100 million of waste within his own company.
Joseph Day, chairman and chief executive of Freudenberg-NOK, can even break down the waste: $30 million of it from five companies acquired in the past three years, $20 million still on the shop floor, $10 million in administration and product development activities and $40 million from its own suppliers.
It’s this “vendor-influenced” waste that Mr. Day finds particularly troubling, so he’s working on a “cost-effective, viable model to teach lean to the sub-tier community.” An announcement is expected next month.
In his speech here earlier this week at the World Class Manufacturing session, Mr. Day says the industry can use the millions of dollars in waste caused by the sub-tier suppliers as the bank account to fund their lean transformation.
“Considering the constant price-down hammering from our customers, I don’t know how some suppliers are surviving without lean systems in place,” Mr. Day says. He says sub-tier suppliers are responsible for tens of billions of dollars of waste, and that 5,000 defective parts per million is not unusual for some suppliers.
Without an aggressive lean training program, Mr. Day says the “North American auto industry will make little progress over the next five years.”
He does not say that lean initiatives should be mandatory across the industry, but he supports the SAE J4000 lean standards to spark the supply chain into action.
Mr. Day says this waste can be tackled through continuous improvement kaizen exercises, and that there is perhaps another $90 million in “systemic waste that we’re attacking through other means.”
Freudenberg-NOK also reports impressive results with two other lean initiatives: “focused factories” and 3P.
Between 1997 and 1999, the company converted 14 of 21 North American plants to focused factories with a narrow product mix, highly predictables processes and a strong culture of continuous improvement. So far, Mr. Day is pleased with the results: labor productivity up 200% and floor space productivity up 400%.
3P, an acronym for Production Preparation Process, is Freudenberg-NOK’s attempts to shift the lean focus from the shop floor to product development. The initiative, beginning in 1998, has generated annual savings of $30 million.
“We’re finding it to be one of the most powerful weapons in the entire Toyota Production System arsenal,” he says.
About the Author
You May Also Like