Ford Ushers Assembly Into Virtual World
A new digital lab in Dearborn ramps up Ford’s ability to use virtual reality in solving problematic vehicle-assembly operations. Ergonomic issues are down 90%, and the number of days missed by injured employees has dropped 75%.
August 14, 2015
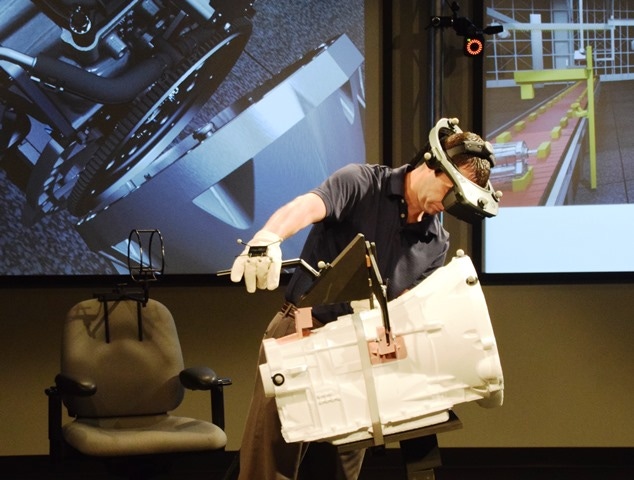
DEARBORN, MI – The human body can suffer enormous strain building a vehicle – bending, stretching, reaching, grabbing, twisting, carrying, pushing and pulling. Do it for 20 or 30 years, and the physical toll can be debilitating.
Ford has a new tool, its immersive virtual-reality lab that opened here in January, which leverages the application of infrared cameras and software to capture and digitally replicate every motion necessary for assembly workers to build a car.
Actually, Ford ergonomists primarily care about the procedures that can be problematic as an all-new vehicle is about to begin production: attaching hoses, mating a transmission to an engine and making electrical connections behind the instrument panel.
Some jobs easily performed by a 6-ft.-2-in. (188-cm) male might be a significant struggle for a petite female, and Ford now is gathering the necessary data through biomechanical modeling to ensure every job on the line can be handled by 90% of plant workers.
The dexterity needed at workstations explains why Ford ergonomists refer to workers as “industrial athletes,” and the virtual-reality lab is designed to help them the same way professional athletes such as struggling golfer Tiger Woods might seek scientific expertise in analyzing every aspect of his swing in attempting to regain his mojo.
“We want to give our industrial athletes the best opportunity for success,” Ford ergonomics engineer Marty Smets says in a recent demonstration for journalists.
That means using the virtual-reality lab to better plan every step in the assembly and installation process and calculating exactly how much force is necessary to install a particular part in the engine bay.
“Also, we know when that person retires, he will be able to swing his grandkids around just like they deserve to do,” Smets says.

Employee wears body suit with 52 markers. As she reaches into simulated engine bay, her motions replicated by digital human model on screen behind.
The benefits of such research can be enormous, says Allison Stephens, Ford’s technical leader for assembly ergonomics.
“We can plan a worker’s posture and movements. We can reduce the amount of prototype-vehicle builds. We can improve time-to-market, resulting in huge cost savings,” Stephens says. “We found that if we looked at stuff virtually and did a good job in the virtual environment, we would actually prevent the issues from showing up in the physical.”
Quantifying Stress on Human Body
Ford started studying closely the biomechanics of assembly jobs in 2003, and Stephens was one of the automaker’s first ergonomists. Well before the use of virtual reality, she would walk the plant floor and talk with workers about their daily tasks.
On a single vehicle program, she and her team would find up to 400 issues that needed to be fixed. Workers would demonstrate how far they had to stretch or how difficult it was to attach a certain part.
“We didn’t make a lot of friends back then because the design engineers were like, ‘What are you talking about? We are too far along (in production). We have 10,000 of these in the warehouse and a million-dollar tool to make them,’” recalls Smets.
The solution was to speak in engineering terms to engineers, and that meant easing into the world of virtual reality and creating digital human models to quantify stress on the human body. The ultimate goal was to get ahead of the process so a vehicle is designed for easier manufacturability.
Stephens has spent much of her time focused on hand clearance (whether there is room to reach into a crowded engine bay to perform what seems like a simple task) and insertion efforts (how difficult it is and how much force is necessary to attach an electrical connector, for instance).
Digital modeling has allowed Stephens’ team to use a 95th-percentile male hand – the biggest hand they could find – to predict a problem and devise a solution well before the vehicle is set to launch.
“We check to make sure our operators are not in an awkward posture, putting stress on their backs. We use digital modeling to detail how much stress will be on those joints,” she says. “A lot of companies use digital models to say, ‘OK, I can analyze an existing job.’ But we are using this to get ahead of it and use it as a planning tool.”

Ford's Allison Stephens shows how 3-D printing can simulate section of cramped engine bay.
Ford has established accepted limits for strain, and the goal is to have jobs that accommodate 90% of the workforce, thanks to the camera-based motion-capture technology now in place, Stephens says.
The digital tools from partner Siemens allow Ford to calculate the maximum strength of a 25th-percentile female in a certain posture. “We can calculate it through the computer and say, ‘Her shoulder will fail if this is a 15-lb. (7-kg) push in this posture.’
“I can talk to engineers and say, ‘That hose cannot go on with more than 15 lbs. of force.’ If it does, then we are at elevated risk of affecting quality. They may not be able to get it on consistently. We have higher risk of injury. It will fatigue that shoulder muscle at a higher rate.”
Digital Models Come a Long Way
Ten years ago, as the effort was just getting under way, the team relied on rudimentary digital human models resulting from a handful of cameras set up in a space too small for executives to come see demonstrations. They literally had to stand at the door to see the process at work.
The new lab has 23 cameras from Motion Analysis positioned on trusses overhead and near the floor, and the cell is meant to replicate the actual size of a workstation. There’s also plenty of room for engineers to observe tests, without interfering with the cameras.
Shooting video at 120 frames per second, the cameras bathe the cell in infrared light, which reflects off 52 markers attached to a suit worn by an employee replicating the motions associated with a certain job.
“As long as two or three cameras see each marker at a given point in time, I can triangulate its position, like the way GPS works. I can very accurately, down to sub-millimeter level, understand the position and rotation of whatever it’s attached to,” Smets says.
Ten years ago, Ford didn’t have advanced algorithms capable of predicting posture and performing up to a thousand checks for every new part and every new assembly process for a future vehicle program, he says.
The team learns much when assembly workers from the plant visit the lab. “Let’s say I put on the (radiator) hose of an F-150,” Smets says. “I’m on the job 10 years, I do it 300 times a day. I have inserted 750,000 rad hoses. That’s a lot of hoses. I need to be talking to that person. Their postural strategies are critical. They’ve absolutely become experts at that little task.”
That worker can come to the lab, put on the marker suit and a virtual-reality mask and then perform the same job virtually, for study purposes. An actual vehicle is not needed in the lab, because this is the digital world: Ford’s CAD files provide the framework necessary to simulate a given task.
“We can calculate a skeleton based on the orientation and location of those markers, and the skeleton is used to constrain a virtual avatar. As she moves around, she can go lean on the fender and try to insert that rad hose. I can use her real joint angles,” Smets says. “We are bringing in skilled people who do this every day and really leaning on their athleticism.”
The efforts in the lab have paid off: Over the past 10 years, Ford has reduced 90% the number of ergonomic issues arising when prototype vehicles are built – from hundreds a decade ago to a mere handful on the recently launched Ford Mustang.
Another important metric is the 75% reduction in the number of days an employee misses for ergonomic-related ailments.
Intervention as F-150 Prepares to Launch
A few years ago, as Ford was developing the all-aluminum ’15 F-150 pickup, manufacturing engineers came to the ergonomics crew with a concern about the mounting of the transmission to the engine.
The installer uses a hoist to guide the transmission, tilted back slightly, and join the two by mating up studs on the transmission with holes in the engine flywheel.
The new transmission was designed with studs 60% shorter than before, meaning the assembler would have a harder time mating the studs.
“When it hit the plant floor, a product specialist said, ‘This is a big deal. I use that every cycle to align and see that stud to the hole,’” Smets recalls.
The team laser-scanned the workstation and created a virtual environment of the plant, including the location of conveyors and dunnage bins, and even predicted the placement of shadows.
Jae Perry, a product specialist at the Dearborn F-150 plant, had flagged the concern and was called to the lab for virtual immersion. Her first day there, she felt like she had been beamed back to the plant, Star Trek style.

Ford engineer Marty Smets discusses how Dearborn Truck worker Jae Perry (right) helped evaluate assembly process as new F-150 neared launch.
“Once they put on the head-mounted display, I turned around, looked and said, ‘Oh my God, it’s like it’s right here,’” Perry says of her workstation. “I could go completely around the engine. The engine was virtually right here in front of me. I’m feeling around, there’s nothing there, but I can see it right here in front of me.”
With the test concluded, Perry says she could see the stud and determined it shouldn’t be a problem on the assembly line. She then returned to her plant to train other workers on the procedure.
In the past, it would take weeks to fix such problems after the fact. Now, by spending a half-day in the virtual world, she can contribute to a faster, simpler fix. She’s become a big fan of virtual reality. “This is wonderful,” she says.
Beyond vehicle assembly, Ford also is applying the process to address issues in transmission and engine plants.
This is the only Ford cell of its kind in the world. Workers have come from other North American assembly plants to solve similar problems, and those fixes are communicated to operations in other parts of the world.
Ford has applied its virtual analysis to 100 vehicle programs over the past decade, and the benefits are apparent both to workers and bean-counters in top management.
“It can’t be underestimated,” says Janice Goral, Ford’s chief engineer-vehicle assembly operations, “that when you are working comfortably all day long, then you’re going to do a good job.”
You May Also Like