GS Yuasa Ready to Enter Li-Ion BattleGS Yuasa Ready to Enter Li-Ion Battle
CEO MakotoYoda admits many unanswered questions remain regarding electric vehicles, including the minimum range drivers will accept. “Even if we develop a battery that can run 300 km, will that be enough?”
June 4, 2009
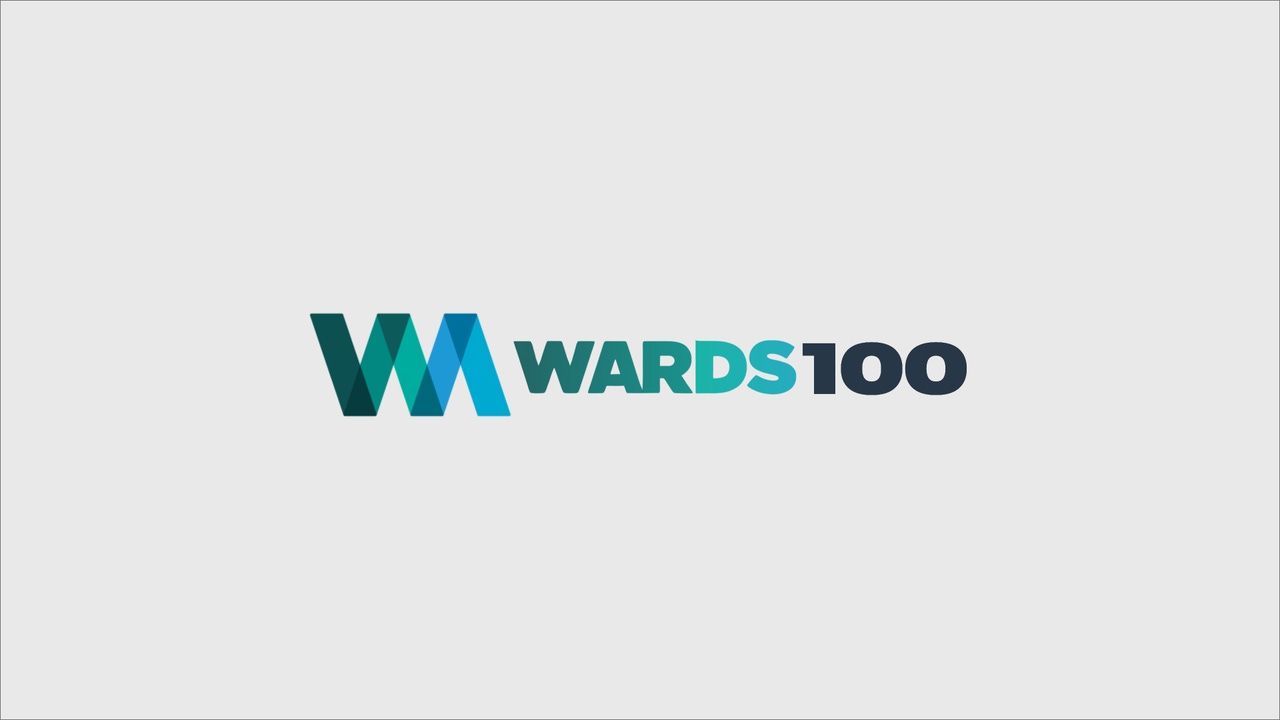
KYOTO, Japan – It is a convergence of old and new, where Japan’s past meets its future. Kyoto, the historic capital and center of arts and culture, is home to some of the most advanced technologies ranging from sensors to nanomaterials.
The city is also home to GS Yuasa Corp., one of the country’s leading automotive battery makers.
This July, it will begin providing its LEV50 lithium-ion battery for Mitsubishi Motors Corp.’s i-MiEV electric vehicle.
A new line inside the supplier’s Kusatsu plant, 12 miles (19 km) east of Kyoto, has capacity to make 200,000 cells per year, enough for battery packs for 2,000 cars. The line is being operated by Lithium Energy Co. Ltd., a joint venture between GS Yuasa, Mitsubishi Motors and Mitsubishi Corp.
Management has set a third-year target of 10,000 units to be divided between the i-MiEV, which by then will be sold in Europe and North America as well as in Japan, and a still-to-be-named small commercial vehicle for the Japanese market.
How big and how fast the EV market grows – and by extension the demand for Li-ion batteries – remains to be seen.
Analysts are pessimistic. Battery costs remain high, and there is little incentive for auto makers to convert to all-electric powertrains as long as gasoline prices remain under $2 per gallon in the U.S. and global new-vehicle demand continues down more than 15% from 2007 levels.
But GS Yuasa President and CEO Makoto Yoda remains optimistic.
“We have resolved most technical issues,” he tells Ward’s in an interview. “Cost remains a major hurdle, as does infrastructure.”
Yoda does not envision an overnight industry transformation by any means. GS Yuasa’s 2011 sales plan calls for only 10,000 battery packs. And if that target proves unreachable, contingencies are in place to divert part of its production to the aerospace industry.
Yoda: Cost, infrastructure hurdles remain for EVs.
Even in its main battery business, GS Yuasa has built flexibility into its business plan to deal with sudden market fluctuations. In addition to batteries for cars and trucks, where the supplier holds an estimated 40% share in Japan, it produces batteries for motorcycles, forklifts and other industrial products.
In fact, non-automotive batteries now account for more than 35% of sales. Including motorcycle batteries, penetration exceeds 40%.
Meanwhile, GS Yuasa on April 1 entered into a joint venture with Honda Motor Co. Ltd. to develop and manufacture Li-ion batteries for hybrid-electric vehicles. The new company, Blue Energy Co. Ltd., is scheduled to begin production on a new ¥25 billion ($250 million) line inside the supplier’s Osando plant in Fujiya, a northern suburb of Kyoto, in fall 2010.
GS Yuasa currently makes conventional lead-acid batteries at the facility.
The JV, owned 51% by a GS Yuasa subsidiary and 49% by Honda, aims to develop HEV applications using GS Yuasa’s EH6 battery. The unit is rated at 6 Ah with energy density of 67 Wh/kg.
There’s no word yet on which Honda model will get the battery first. Next up in the auto maker’s hybrid lineup is the CR-Z sports car due in 2010. A senior Honda research official indicates the CR-Z will adopt the same Sanyo Electric Co. Ltd. nickel-metal-hydride battery developed for the new Insight and Civic Hybrid.
This means the Fit Hybrid, due out early in the next decade, could be the first to get the new JV’s Li-ion pack.
At present only one Honda, the fuel cell-powered FCX Clarity, employs a Li-ion battery. The auto maker declines to disclose the name of the supplier.
Yoda admits many unanswered questions remain regarding EVs, including the minimum range drivers will accept. He notes Mitsubishi’s i-MiEV has a 100-mile (161-km) range, meaning it is limited to trips of no more than 50 miles (80-km) one way.
“Since Mitsubishi is initially targeting fleets, this won’t be a serious problem,” he says. “But if and when the auto maker enters the mass market with the car, this could become a major impediment. We won’t know how serious until we receive customer feedback.
“Even if we develop a battery that can run 300 km (188 miles), will that be enough? Would it enable Mitsubishi to sell more cars? We simply don’t have answers yet.”
Production of i-MiEV batteries begins in July.
GS Yuasa and Mitsubishi opened their JV plant last month. They foresee second-year production more than doubling to 500,000 cells, or 5,000 battery packs.
Yoda regards the third-year target of 10,000 packs the threshold for mass production, at which time pack costs should be about ¥1.5 million-¥2.0 million ($15,000-$20,000). Through process improvements and increased volumes, he believes it may be possible to lower pack costs to ¥1.0 million-¥1.5 million ($10,000-$15,000) by 2015.
But even if his company can hit those 2015 targets, it still leaves motors and inverters, which Yoda estimates add another ¥1 million-¥1.5 million to EV powertrain cost.
This is clearly more than the average consumer will be willing – or able – to pay. Ultimately, EVs must be priced competitively with gasoline-powered cars, Yoda says, suggesting government subsidies will be needed to promote sales at the outset.
He also advocates some sort of battery-leasing scheme by power utilities that would allow battery costs to be spread over a longer period of time.
Meanwhile, Yoda says any subsidy program the U.S. government introduces should be open to all battery, motor and inverter suppliers regardless of nationality.
“We can supply (Li-ion) batteries today,” he says. “If U.S. car makers turn to domestic suppliers, it could take five years to ensure battery safety and performance and gear up.
“I truly believe – not just because we have a business interest – the quickest and most realistic way for car makers who don’t already possess these technologies (motors, inverters and batteries) is to purchase them from existing suppliers.”
He says his company “will go to the U.S. or Europe if there is an opportunity.”
For the i-MiEV, the supplier will deliver a version of its LEV50 battery that has cell capacity of 50 Ah and energy density of 110 Wh/kg, according to Yoda.
That is less than the 160 Wh/kg for the Li-ion battery developed by Nissan Motor Co. Ltd. and NEC Corp. But Yoda says GS Yuasa has the knowhow to raise density to 250 Wh/kg, currently the highest density levels found in Li-ion batteries for cell phones.
At the outset, Mitsubishi will target the i-MiEV at short-range fleet operators, possibly including taxi services.
“For these, infrastructure will not be a serious problem,” Yoda says. “But once the auto maker begins mass-market sales, a battery recharging network will be necessary.”
Meanwhile, he confirms GS Yuasa has begun development of a battery for application in a plug-in HEV.
“We can make one,” Yoda says. “Since we already have 50-ampere and 5-ampere units in our lineup, there will be no problem in producing one with 25-ampere capacity,” the amount needed for a PHEV.
In a related development, the supplier announced this month it had delivered a 12-volt, 48-Ah battery to Toyota Motor Corp. for its Aurus model built in the U.K. with a stop-start system. The compact battery is lead-acid, unlike the battery for the “intelligent idle-stop” system on the Vitz (Yaris), which is Li-ion.
Available in Japan, the Vitz system reportedly cuts fuel consumption 8.5%. Toyota has not revealed the name of the battery supplier.
Yoda sees great potential for such micro-hybrid applications.
“No one should expect all gasoline-powered cars to disappear and be replaced by hybrids and EVs,” he says. “In order to reduce fuel consumption and lower (carbon-dioxide) emissions, idle-stop is one of the best solutions currently available.”
Comparing GS Yuasa Li-ion cells with the laminate technology of the Nissan-NEC batteries, Yoda acknowledges laminate’s ‘broad surface’ structure enables the battery to cool down more easily. But he cautions that laminate cells must be encased, adding weight to the vehicle and canceling some of the performance advantage.
“I believe that our technology is more robust and more durable,” he says.
What comes after Li-ion? Yoda believes it will be some new combination of manganese, cobalt and nickel, implying a smaller percentage of cobalt. Another possibility is iron.
GS Yuasa, just beginning its sixth year of operation since the April 2004 merger of Japan Storage Battery Co. (GS) and Yuasa Corp., ranks a distant third among global automotive battery makers, though it is No.1 in Japan and Southeast Asia.
In 2007, according to company estimates, it ranked No.1 globally in motorcycle batteries.
Not surprisingly, almost all of its 33 plants are in the Asia/Pacific region, with no automotive battery plant in North America or Europe. It operates one motorcycle battery plant in the U.S.
In the fiscal year ended March 31, 2009, the company reported ¥14.3 billion ($142.8 million) in operating profit, up 20.1%, on a 6.7% decline in sales to ¥283.4 billion ($2.8 billion). In the current fiscal year, it is projecting a 51% decline in profits to ¥7 billion ($70 million) on sales of ¥240 billion ($2.4 billion).
Both JV partners, Japan Storage and Yuasa, have been working on Li-ion batteries since the early 1990s.
“I never thought that the EV world would come into existence so soon,” Yoda says. “In fact, until 2002 or 2003, I felt that hybrid cars would be an intermediate step to electric vehicles. I now feel that hybrids and EVs can coexist. This is why we entered into a joint venture with Mitsubishi.
“The ultimate solution to global warming and reducing CO2 emissions might still be the fuel cell,” he notes. “But when we consider the high costs and various infrastructure-related problems, I believe EVs powered by lithium batteries are a more realistic solution.”
About the Author
You May Also Like