Have We Not Learned Our Lesson?
Industry analyst Michael Robinet says automakers once again lack enough flexibility, only this time it’s for cars and CUVs.
August 4, 2015
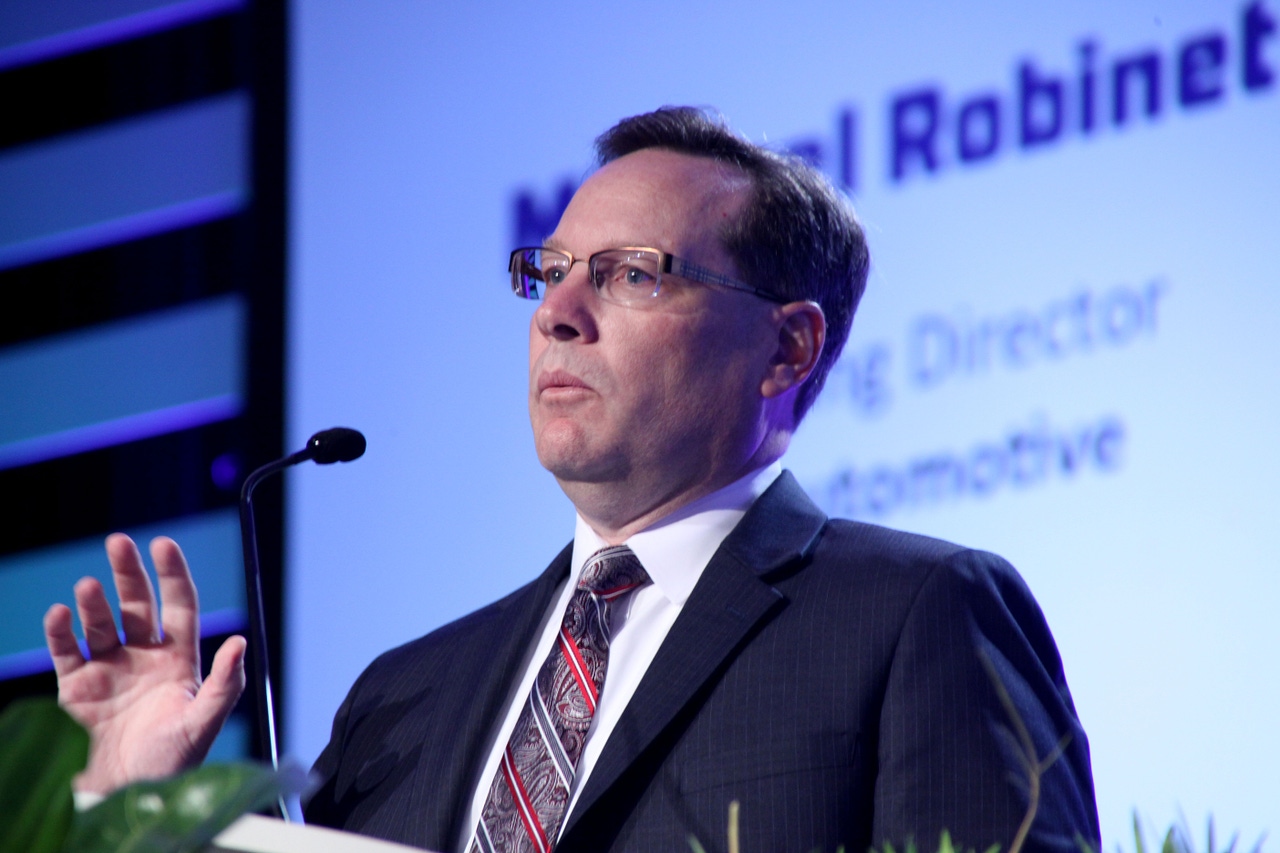
TRAVERSE CITY, MI – You know the saying about those who forget history being doomed to repeat it? Well, it might be happening right now in the North American auto industry.
With CUV sales soaring and car sales slipping, a leading industry analyst is worried automakers have forgotten their past.
“I can count on one hand the number of facilities that build sedans and crossovers off the same line. Have we not learned our lesson in this industry?” Michael Robinet, managing director-IHS Automotive Advisory practice, tells attendees on the second day of the 2015 CAR Management Briefing Seminars here.
And this time, lack of production flexibility is not just a Detroit Three problem.
“It’s also a little bit of a Japanese problem,” Robinet tells WardsAuto after his speech. “If you think about it, Nissan just brought Rogue and Murano (production from Japan) to this market. It took them forever to figure it out.”
Nissan had not built a CUV at its Canton, MS, plant prior to Murano’s Job One last fall, although its Smyrna, TN, plant now building the Rogue compact CUV already was assembling the 3-row Nissan Pathfinder and Infiniti QX60 CUVs at the same time as Altima, Maxima and Leaf cars.
Hyundai assembles its Sonata and Elantra midsize and compact cars at a plant in Montgomery, AL.
Several Toyota plants also build only one vehicle type, including the automaker’s Blue Springs, MS, facility (Toyota Corolla) and San Antonio plant (Tundra and Tacoma pickups).
However, the issue of building cars in one plant and light trucks in another is most acute at GM, Ford and FCA facilities.
For instance, GM has slowed or shut down assembly lines this year at its Orion Twp., MI, plant due to slowing demand for the subcompact Chevy Sonic and Buick Verano cars built there.
WardsAuto data shows 11 GM plants alone will be assembling only one vehicle type in the years 2015 through 2021.
“I can only think of one facility at Ford and maybe one to two at (General Motors) that actually build CUVs and sedans on the same line,” Robinet says. “In this market, with fuel prices that have switched back and forth, it’s surprising the lack of inter-plant flexibility.”
Inflexibility About Flexibility
WardsAuto data shows 40 out of 74 North American plants in 2015 are building just one type of vehicle. However, this doesn’t necessarily mean all 40 cannot build another vehicle type.
For instance, Honda previously has assembled cars and CUVs (Civic and CR-V) in the same plant in Alliston, ON, Canada, and Mitsubishi has as well at its soon-to-close Normal, IL, plant.
Robinet says automakers are suffering from decisions made at an earlier time, when there was more of a balance between cars and CUVs. Now the latter vehicle type makes up a third of all new vehicles sold in the U.S. this year, while car sales have flattened or fallen.
WardsAuto data shows cars were down 1.6% through July, while light trucks rose 10.2%. CUV sales jumped 13.7% within the light-truck category.
Robinet uses his podium at MBS to warn suppliers they may not be ready for the near-term future, given shorter product lifecycles and the increasingly global nature of the industry.
“In some respects, we’re going to ask you to change your business model, because you’re almost going to need to,” he tells supplier attendees in the audience.
Hardware and Hard Choices
U.S. vehicle sales will grow modestly for another two to three years, but stabilization will occur as new-car prices rise due to added content and demographic factors such as aging Baby Boomers and younger buyers not yet in their prime earning years.
At the same time, automakers are refreshing or revising their vehicles more often, as well as dealing with regulatory pressures to build safer, more fuel-efficient vehicles, the latter affecting material choices and, as a result, tooling.
“The new cadence today is, ‘I’ve got a build process, especially with all these new multimaterials, that’s probably got to last me 10 years, and out of that I need to get two platforms” for either two major changes or all-new vehicles, he says of modern product lifecycles.
Slow or unsuccessful product launches also should be a worry point for suppliers, with Robinet noting automakers typically sell highly contented vehicles at the beginning of a launch cycle and offer fewer or no incentives.
“If (as a supplier you) had a (contract for parts for a) 7-year vehicle and it took you three months to launch it, you figured, ‘Well, I’ve lost some capacity but I’ve got another 6.5 years to make this up, no problem.’ In the era of a 5-year cadence, if you have a poor 3-, 4-month launch, that’s a problem,” Robinet says.
He also warns suppliers aren’t prepared for the current and coming Mexico assembly boom.
“By the end of the decade, 42% of the launches are going to be in Mexico,” he says. “Are you ready for that? Do you have personnel? I would hasten to say that most of you don’t.”
Read more about:
2015You May Also Like