Kaisen Cuts Costs GROWTTH pays big dividends at Freudenberg-NOKKaisen Cuts Costs GROWTTH pays big dividends at Freudenberg-NOK
CLEVELAND, GA - Tim Stickles and Gary Chastain knew it was possible.They knew that if their kaizen - or "continuous improvement" - team cut the time it takes to change over a valve stem seal press at the Freudenberg-NOK General Partnership (FNGP) plant here, the company would save money and employees could once again spend weekends with their families.Currently, machine operators spend 37.5 hours
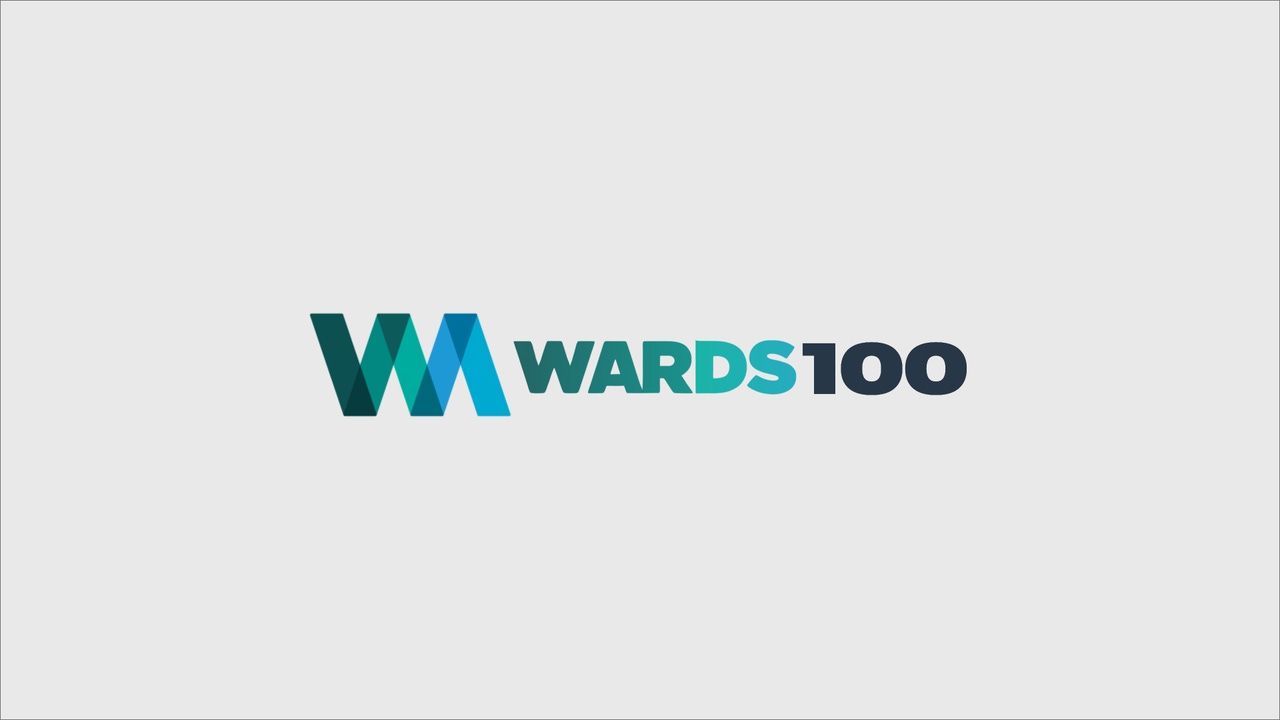
CLEVELAND, GA - Tim Stickles and Gary Chastain knew it was possible.
They knew that if their kaizen - or "continuous improvement" - team cut the time it takes to change over a valve stem seal press at the Freudenberg-NOK General Partnership (FNGP) plant here, the company would save money and employees could once again spend weekends with their families.
Currently, machine operators spend 37.5 hours a week doing 25 such setups, an average of 1.5 hours per changeover. That's 37.5 hours of lost production.
So FNGP took the problem to a kaizen team to conceptually tear apart the setup process and try rebuilding it to eliminate wasteful or unnecessary steps.
The team consisted of two Cleveland employees (Mssrs. Chastain and Stickles), two workers from the FNGP plant in Scottsburg, IN, a manager from a safety valve manufacturer in Oklahoma, a contract employee and a Detroit journalist. The last three members knew little about valve stem seals beforehand, which is precisely what the kaizen organizers wanted.
"People coming in from the outside look at a process and question why we do things in a certain way," says Melissa McCoy, a kaizen leader at FNGP. "We discuss better ways to do things because those of us who work there look at it and accept it as the only way to do something."
Kaizen is not a new concept for employees at FNGP, a partnership between Germany's Freudenberg & Co. and Japan's NOK Corp. to make seals, vibration dampers and plastic components for the North American automotive market.
The partnership was launched in 1989 but ran into trouble early on. Layoffs were inevitable as the company was losing $15 million a year. A new strategy was needed - fast.
President and CEO Joseph Day began studying the successful Toyota Production System and determined it was just what his company needed. He created a program in 1992 and named it GROWTTH, an acronym for Get Rid of Waste Through Team Harmony.
All employees could leave their normal duties for a week to serve on a kaizen team focusing on a particular problem. Participation is not mandatory, but frequently the best ideas come from the front-line plant workers who struggle with certain issues every day.
After five years, GROWTTH has paid considerable dividends. The 2,340 kaizens held across 17 North American facilities resulted in total net savings of $24 million, a reduction in the cost of quality from 9.5% to 4.3%, a drop in defective parts per million from 850 to 132 and an increase in sales per employee from $99 to $162.
That was as of 1996. So far this year, 775 kaizens have been held, yielding $18.2 million in estimated savings. The accelerated pace in 1997 is part of the company's GROWTTH "blitz," an intensive 10-week succession of kaizens in one facility.
In the valve stem seal cell at Cleveland, the team begins its work by videotaping an employee doing a changeover. The plant makes seals for Ford Motor Co., General Motors Corp, Chrysler Corp. and transplants. FNGP makes 80% of the valve stem seals in North America, about 140 million a year.
The employee doing the changeover, Elizabeth Knight, says the job normally takes over an hour. But she is the only operator running 10 or more machines in her cell, so if something goes wrong with one of them, she has to stop the changeover to fix it. On a bad day, changeovers can take three hours or more. This particular changeover takes her 1:12:53. The team's goal is 30 minutes.
The kaizen team finds several problems in the changeover. The tooling and heavy metal platens necessary for the setup are poorly labeled and poorly organized in three cabinets that sit on the far corner of the work cell. The team sets out to label each shelf in the cabinets and to move them to a more central location, saving considerable walking. They also consider push carts to save steps.
The team tries another setup using two workers, one on each end of the machine. Mssrs. Chastain and Stickles accept the challenge and are cruising right along, on pace to do a 15-minute changeover, when disaster strikes.
For some reason, the machine is not dispensing mold release, a spray that prevents the rubber from sticking to the mold. The machine is connected by a tube to a pressurized tank of mold release nearby, but the top of the tank has come loose and is now spewing mold release into the air, like a volcano. They hang their heads in disappointment, finishing in 38 minutes.
The next setup takes 28 minutes. But it's not good enough.
The team decides that perhaps two employees merely get in each other's way. So the team writes a standard procedure allowing one worker to do all the processes necessary, first on the back of the machine, then the middle, then finishing up on the front, eliminating a lot of walking.
On day four of the kaizen, the team hits paydirt. On his third try, operator Troy Vandiver completes a setup in 17:37, the manufacturing equivalent of running a four-minute mile. The team rejoices.
The key time saver was cutting down on steps and having the necessary tools ready. In the first setup, Ms. Knight walked 1,608 feet. The new procedure requires only 172 feet of walking. Within a day, plant managers were adopting the team's findings as a standard procedure for all valve stem seal cells in the plant.
Mr. Chastain, an eight-year employee, says he is confident employees will be able to learn the new procedures, although it will be difficult at first. "It will the first time they do it because of old habits, but old habits can be broken and replaced with new good habits," he says.
About the Author
You May Also Like