Labs 'Demystifying' Ceramics ManufacturingLabs 'Demystifying' Ceramics Manufacturing
The Department of Energy's Sandia National Laboratories, five commercial ceramic manufacturers, and Los Alamos National Laboratory are studying methods to bring true "science" into ceramics production in an effort to create better products and slash costs."We are demystifying ceramics manufacturing," says Sandia scientist Kevin Ewsuk, who is spearheading the project. "In the past, new ceramic component
June 1, 1999
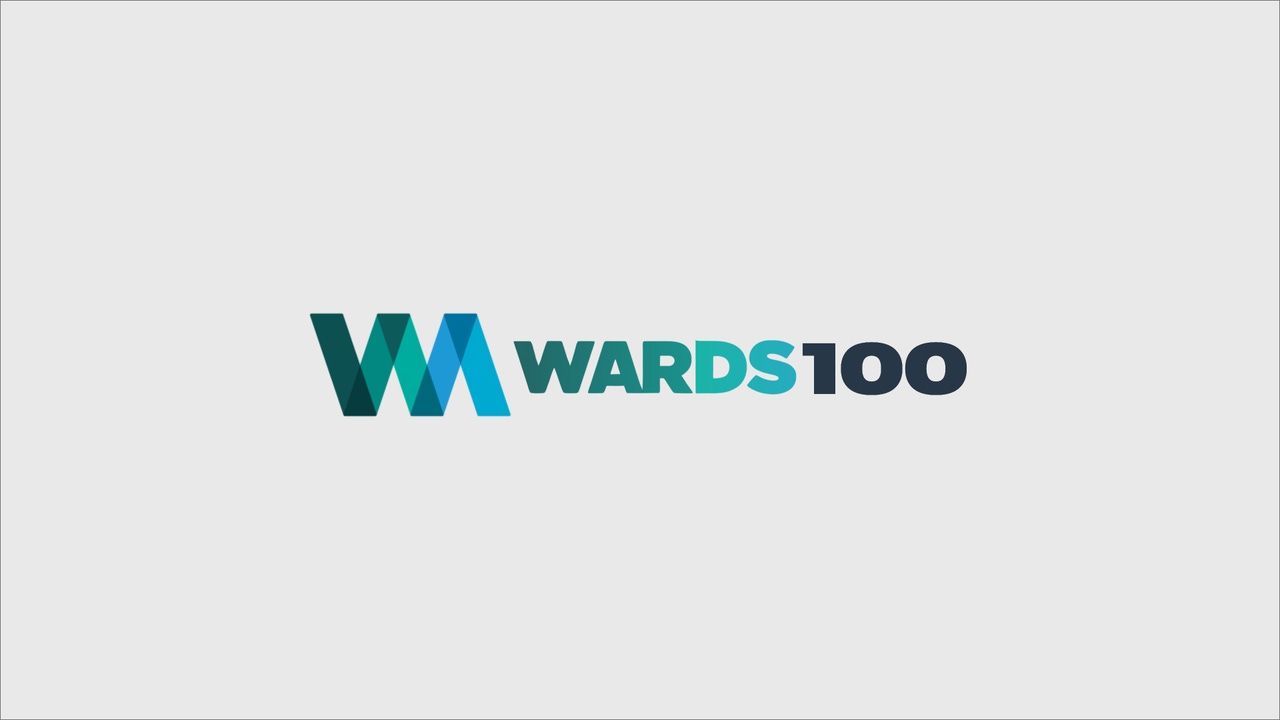
The Department of Energy's Sandia National Laboratories, five commercial ceramic manufacturers, and Los Alamos National Laboratory are studying methods to bring true "science" into ceramics production in an effort to create better products and slash costs.
"We are demystifying ceramics manufacturing," says Sandia scientist Kevin Ewsuk, who is spearheading the project. "In the past, new ceramic component production involved trial-and-error refinement of die designs. We are developing a systematic approach to manufacturing that involves parts being designed, manufactured, and tested in a predictive mode."
Automakers and suppliers continue to exhibit more than a passing interest in ceramics; the material holds promise for a wide range of applications, from internal engine components like valves to electrical and chassis improvements. But manufacturing difficulties always have been a thorn in ceramics' side.
For the past three years, the entities have worked together under a cooperative research and development agreement (CRADA), exploring new and better ways of manufacturing advanced ceramic components. It is the first time that competing ceramics companies and national laboratories have joined forces for research and development.
The agreement remains in effect for two more years between Sandia, Los Alamos, and five ceramics manufacturers making up the Assn. of American Ceramic Component Manufacturers Consortium Inc. (AACCMCI). The companies are Delphi Energy and Engine Management Systems of Flint, MI; Advanced Cerametrics of Lambertville, NJ; CeramTec North America of Laurens, SC; Superior Technical Ceramics of St. Albans, VT; and Zircoa Inc. of Solon, OH.
The ceramics CRADA already has made several significant strides. One of the participating companies saved $50,000 in six months on a line of pressed ceramic materials; another estimates a $100,000 savings from process improvements. Still another cut manufacturing costs by 20% while simultaneously reducing production time.
A primary goal of the research was to develop a ceramic part-forming model on a personal computer in order to employ the model to determine if the design has flaws. The manufacturer can then make a die from the model and be guaranteed that it will work.
Ultimately, computer modeling could replace the current ceramic-making method - a process that relies as much on artisanship as it does on genuine manufacturing technique.
The manufacturer designs a part, anticipating from experience that it will function, makes the die, and then builds a prototype part. If the prototype has problems, the die has to be redesigned and retooled. But ceramic component dies can cost $5,000 each, and when one is flawed and has to be modified, the cost goes up.
Mr. Ewsuk says the CRADA has allowed the participating companies to learn more about why some powders are difficult to press, supplied answers to why poor pressing occurs, and provided insight into what to do to improve powders and the conditions for pressing.
"As the CRADA has evolved, the participating companies have received the benefit of obtaining new characterization, design, and process tools to optimize the manufacturing techniques and performance of pressed ceramics - resulting in savings and more dollars earned," Mr. Ewsuk asserts.
About the Author
You May Also Like