Mazda Rethinks Manufacturing Process
Mazda says using CNC machines for engine production allows it to be competitive with larger automakers that enjoy better economies of scale.
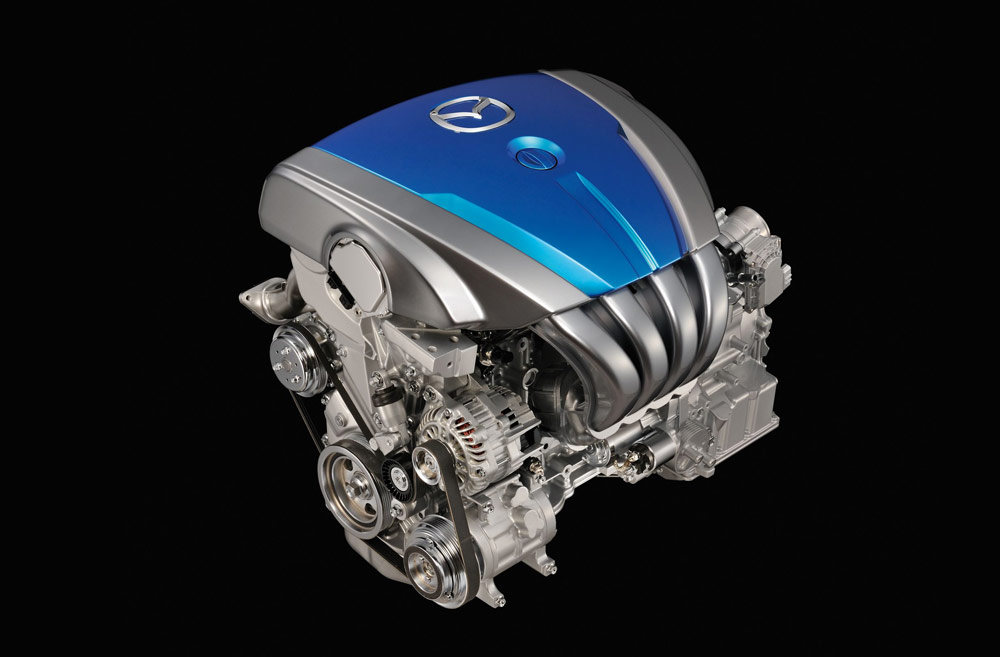
SAN DIEGO – Tiny Mazda believes it may have found the secret to competing effectively against such automotive behemoths as General Motors and Toyota that enjoy huge cost advantages inherent with mass-producing millions of vehicles annually.
Hiroshima, Japan-based Mazda churned out only 1.4 million vehicles last year on a global basis, according to WardsAuto data, only a fraction of the 9 million-plus cars and trucks built yearly by each of the world’s biggest auto makers.
“We needed to approach that fundamental truth (of economies of scale) and find out if it’s still fundamentally true, or is there a way to engineer our way around it,” Dave Coleman, vehicle development engineer-Mazda North American Operations, says during a media backgrounder here. “And it turns out there is a way to engineer around it.”
Severing its engineering partnership with Ford has allowed it to have total control over its vehicle-development programs. The result is Skyactiv, the name given to a suite of components including powertrain, suspension and chassis.
“We’re not sharing anything with Ford anymore,” Coleman says. “It’s a completely clean sheet and we turned what could have been adversity into an opportunity.”
Typically, low-cost manufacturing requires a single machine to make a particular part in high volume. The more that machine produces, the quicker the automaker can amortize equipment cost.
But Coleman says modern technology enables Mazda to bypass the core principle of economies of scale, and save money in the process.
“It turns out there are much more efficient manufacturing processes available now that allow us to design things more flexibly,” he says. “It lets us spend less on the initial investment in the factory, but also lets us design the car more efficiently.”
Key are the Computer Numeric Control machines Mazda is using in manufacturing its Skyactiv engines.
“We’re building with flexible CNC machines that can make a lot of different parts,” Coleman says. “We don’t need to make all of the same thing. As long as we’re running the machine all the time, we’re getting our value out of that machine.”
Coleman points to Mazda’s line of MZR engines, which preceded the new Skyactiv mills.
MZR came in four different displacements. But because Mazda wanted each engine to share as many parts as possible, the mills were the same size, with only the bore and stroke changed to allow the differing displacements.
The engines were built by a series of specialized machines, each performing a specific task.
Although engines have been made that way for decades, and is the way most large automakers still manufacture engines, it’s not an ideal solution, Coleman says.
“When you change the bore in an engine, you change the combustion dynamics, the way the air flows and the combustion happens,” he says. “When we tune that engine, it’s a lot of work to make it run right and as efficient as possible. As a result, with the old engine family, we had 177 different calibrations to maintain.”
With the new Skyactiv mills, each engine is calibrated to best suit its architecture and displacement. And with the CNC machines, different types of engines, including gasoline and diesel mills, can be built at the same time, creating the flexibility needed to respond to customer demand.
Perhaps most importantly is the amount of money Mazda saved switching to the new process. Coleman says CNC machines not only are more efficient than the old specialized machines, but also are much cheaper.
“The cost is 70% less with the new machines and a hell of a lot faster,” he says, noting the time to machine an engine is now one and a half hours, compared with six hours using the old method.
“The actual machining time on one of the old machines is less than half the time spent on actually machining something, because the rest of the time is spent putting things on, taking things off and moving around and waiting,” Coleman says.
The new process is up and running in Mazda’s Hiroshima and Fuchu, Japan plants, and plans call for CNC machines to be added at other facilities, including the new assembly and engine plants now under construction in Salamanca, Mexico.
“Everything is built first in Japan to make sure it gets all sorted out, and then we’ll just duplicate the same process over there,” Coleman says.
Mazda is one of the first major automakers to employ CNC manufacturing on a large scale, but it likely won’t be the last, Coleman says, noting its small size made the transition easier than it will be for its larger competitors.
“There’s no question everyone is going to follow us down this path,” he says. “But we were able to get there first because we don’t have millions of dollars invested in these factories all over the world that we’re still trying to amortize.”
About the Author
You May Also Like