New Coating Process Cuts Sludge 80% at CAMINew Coating Process Cuts Sludge 80% at CAMI
While zirconium has been used in other industries for corrosion protection, it has taken 13 years for PPG to develop it for the automotive industry.
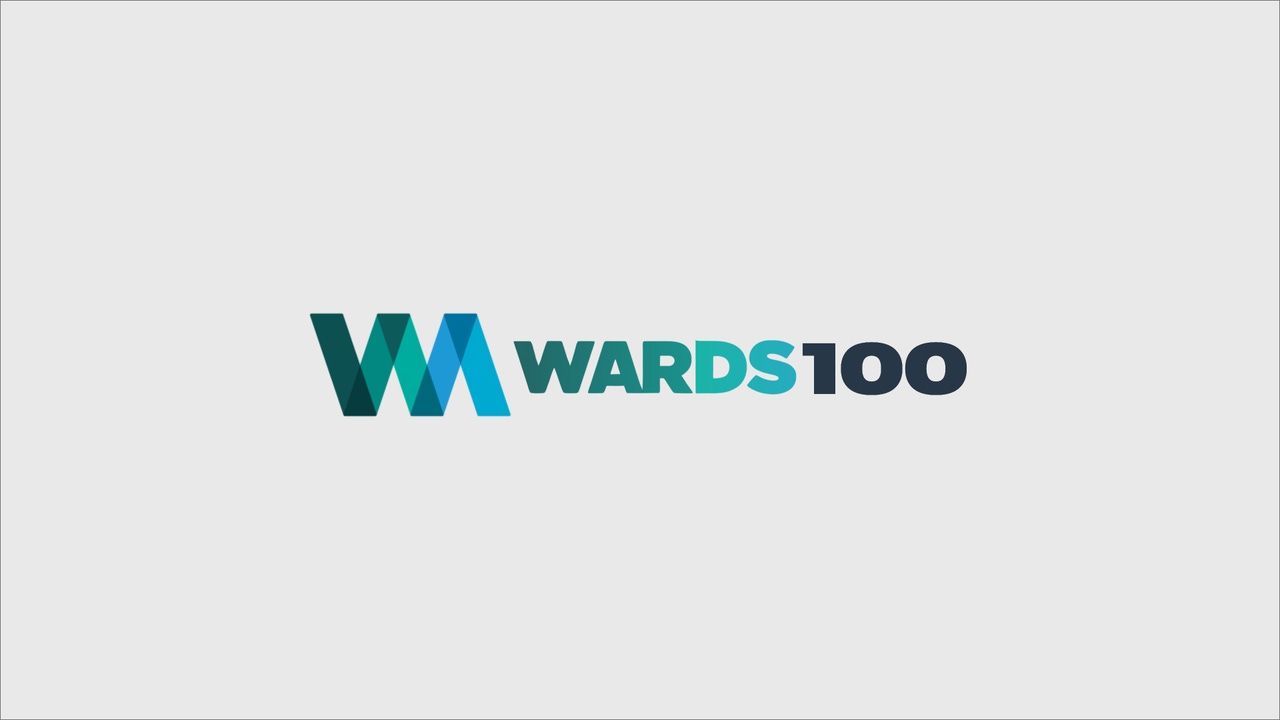
Special Coverage
North American Int’l Auto Show

DETROIT – A new paint pre-treatment process is expected to cut sludge 80% and save about $105,000 a year in energy and water at the General Motors Corp.-Suzuki Motor Corp. CAMI Automotive Inc. joint venture in Canada.
The process replaces the zinc-phosphate bath taken by car bodies to prevent corrosion with a zirconium-based product PPG Automotive calls Zircobond.
“Zircobond puts a thin film on the steel and provides the same corrosion protection” as zinc phosphate, Ray Schappert, director-global innovation for PPG, says at a presentation of the process at the North American International Auto Show here.
Operational savings result from its environmental friendliness, because the process involves less rinsing and dipping and fewer disposal requirements. In a greenfield plant, he says, Zircobond pre-treatment would require less space and fewer operations, resulting in capital expense savings of as much as $2.6 million. CAMI, the first Zircobond customer, is using the process in its existing facility.
PPG and CAMI workers filled pre-treatment tanks with the zirconium liquid Jan. 6 and production began with the night shift Jan. 13. First-quarter production plans at CAMI call for 47,000 units of the Chevrolet Equinox, Pontiac Torrent and Suzuki XL7, a 14% increase over like-2007.
While zirconium has been used in other industries for corrosion protection, it has taken 13 years for PPG to develop it for the automotive industry, says Rich Moyle, who was among the PPG workers who assisted with the product launch in Canada.
The proprietary formulation has a higher pH than zinc phosphate, Moyle says. Traditional zinc baths etch the steel, which results in more sludge that requires disposal. He says the zinc-phosphate system also results in a crystalline coating that can be chipped by stones when driving, while the zirconium treatment provides a thinner, amorphous coat that adheres better to the steel.
CAMI PPG's first Zircobond customer.
While no other contracts for the process have been signed, PPG is talking with other companies, and GM “is aggressively pursuing global implementation opportunities,” says GM global process pretreatment lead Kevin Cunningham. “Continued leadership in the use of environmentally friendly technologies is imperative at General Motors.”
CAMI has been a leader in paint-shop quality and environmental activity.
According to its website, it won the J.D. Power “Best in Segment - Paint” award for compact SUVs, beating out competitors such as the Ford Escape, Kia Sorento and Toyota RAV4, and it landed a GM North American Operations award for achieving a warranty claim rate of less than 1%.
CAMI recycles everything from cardboard to pop cans, and the Regional Council of Ontario has cited the plant for “a series of highly innovative programs (that) have…resulted in a 94% diversion of waste from landfill for a yearly total of 19,800 tons (18,000 t),” even before the Zircobond initiative on sludge.
The CAMI paint shop uses a closed-loop system to capture all the paint line purge solvents, recycling 6,341 gallons (24,000 L) of solvent every month.
CAMI was established in 1986 in Ingersoll, ON, Canada. Production was launched in 1989, and the plant has built more than 2 million vehicles to date.
About the Author
You May Also Like