Organizing vs. Outsourcing UAW achieves modest gains in '97Organizing vs. Outsourcing UAW achieves modest gains in '97
With prostate cancer surgery behind him and a re-election campaign ahead of him, Stephen P. Yokich is laying the groundwork from which the United Auto Workers union will seek to reverse the steady erosion of its active membership ranks.UAW membership is now about 750,000, or roughly half where it was 20 years ago.Globalization and outsourcing virtually guarantee that hourly employment among the Big
December 1, 1997
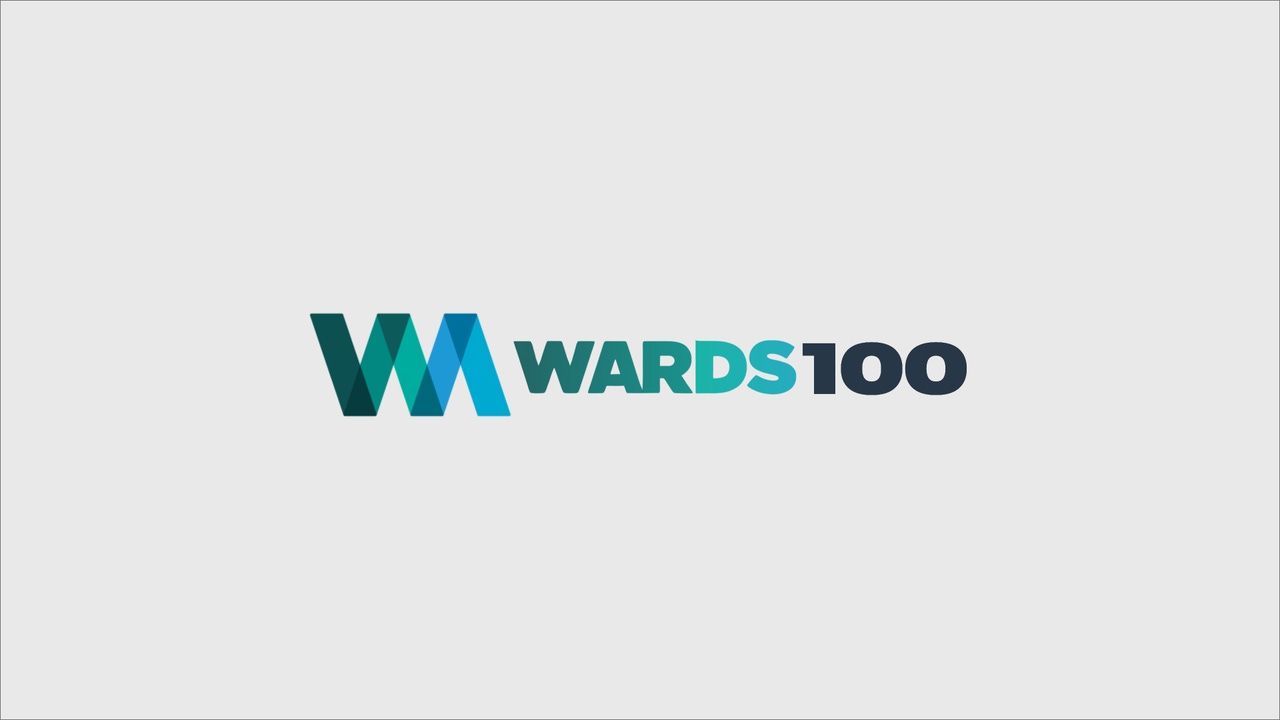
With prostate cancer surgery behind him and a re-election campaign ahead of him, Stephen P. Yokich is laying the groundwork from which the United Auto Workers union will seek to reverse the steady erosion of its active membership ranks.
UAW membership is now about 750,000, or roughly half where it was 20 years ago.
Globalization and outsourcing virtually guarantee that hourly employment among the Big Three automakers will continue to fall. Consequently, organizing previously non-union suppliers who are taking on more engineering and production responsibility is more important than ever.
"Even though many people thought we would be dead by the 21st century, the new energy throughout the AFL-CIO under John Sweeney's leadership has shown that we will be around for the 22nd century, too," says the one-time tool and die maker who turns 63 next August. "As our numbers have declined, our popularity among Americans has never declined. Even if they won't vote for you, between 70% and 80% of those asked think there's a place in society for organized labor."
Among this year's victories:
After a three-week strike against Johnson Controls Inc., during which Ford Motor Co. refuses delivery of seats made by replacement workers, UAW Regional Director Bob King negotiates a contract giving workers raises of $3.50 an hour over three years.
In October, the UAW gains 357 new members at a JCI plant in Suwanee, GA, after a 2-to-1 vote in favor of UAW representation. A contract has yet to be negotiated
Other favorable certification votes are won at Phillips Products Inc., a South Carolina parts supplier; Reynolds Aluminum Wheel in Beloit, WI; and DuPont Automotive's Mount Clemens, MI, plant.
After a 28-day strike at a Chrysler Corp. engine plant in Detroit, the company agrees to invest $100 million to modernize for future engine block production, and the union accepts Chrysler's decision to outsource driveshaft production to Dana Corp.
But strikes at General Motors Corp.'s Oklahoma City and Pontiac, MI, assembly plants dragged on for two and three months, respectively. While the company agreed to hire some workers to relieve overtime pressures in the short term, management also held its ground that new products with simpler designs will require fewer people in the long run.
And Mr. Yokich pulled the plug on a renewed effort to organize Nissan Motor Co.'s Smyrna, TN, assembly plant workers when UAW representatives failed to secure signatures from more than 65% of the workforce. It was the second time the UAW failed at the second oldest of the Japanese transplants in the U.S.
"They're still a union in decline," says Sean McAlinden, a labor economist at the University of Michigan and a long-time observer of the UAW. "The question is whether their new commitment to organize will be backed up by enough spending to succeed."
This month the union's administrative caucus will vote to create a new vice president position for organizing, for which Mr. Yokich has selected Mr. King.
Organizing a dozen small suppliers won't get half as many headlines as one defeat at an assembly plant, but it will begin to change the UAW's image, which is sometimes skewed by the needs and influence of its growing ranks of retirees.
"We had a great year in organizing smaller suppliers, but why beat your head against the wall with a large assembly plant?" Mr. Yokich asks. "It doesn't make sense if you get 45% of the people signing up, or even 55%. You go to an election and it's very difficult to win."
Another area of opportunity will be Delphi Automotive Systems' ongoing restructuring in the U.S. Four years after Delphi sold its gear and axle operations to American Axle & Manufacturing Inc., the UAW not only has negotiated its first contract with American Axle management, but it has seen the number of workers increase.
"Here's a company that moves in and takes over a dilapidated GM plant in a delapidated neighborhood (Hamtramck, MI), cleans it up, hires over 1,000 new employees and still makes quality production," he says. "I think that's a good example."
Delphi now is seeking buyers for seven seat plants, two of which are in the U.S.; a coil spring operation in Livonia, MI, and lighting plants in Anderson, IN, and Monroe, LA. Magna International Inc. is interested in the seating plant, as are Lear Corp. and JCI.
Could the UAW build the same kind of relationship with someone like Magna as it has with American Axle?
"I don't know," Mr. Yokich says. "I don't know that much about the company. I don't really know their management."
In his spare time, the UAW president will push ahead with George Becker and George Bournias, his counterparts at the United Steelworkers and International Association of Machinists, to consummate the unification, announced more than two years ago, of what will be the largest industrial union in the Western Hemisphere, with at least 2 million active workers and 1.5 million retirees.
"Our hit date is 2000," says Mr. Yokich.
Only time will tell whether the move will stanch the gradual decline of union membership as a percentage of the total U.S. workforce, which has fallen to 13% from about 30% in the 1960's.
"You will add more muscle," he says. "Let's not kid ourselves. The input we're talking about is in Washington, making sure your members are politically active. Making sure people get out and vote. As a union, if you're good at that, you carry more weight in the decisions that help us or harm us."
Read more about:
1997About the Author
You May Also Like