Oscars and Accountants Don't MixCost savings shouldn't be criteria forinnovationOscars and Accountants Don't MixCost savings shouldn't be criteria forinnovation
Imagine if a film couldn't win an Academy Award unless it provided the studio with a major cost savings. Sound ridiculous?Sure. Oscar winners frequently are big money makers, but ultimately - despite all the hype, politics, and high-level maneuvering - the judges reward quality acting and filmmaking. Movies that go horribly over budget and are dogs at the box office still win Oscars.Even in shallow,
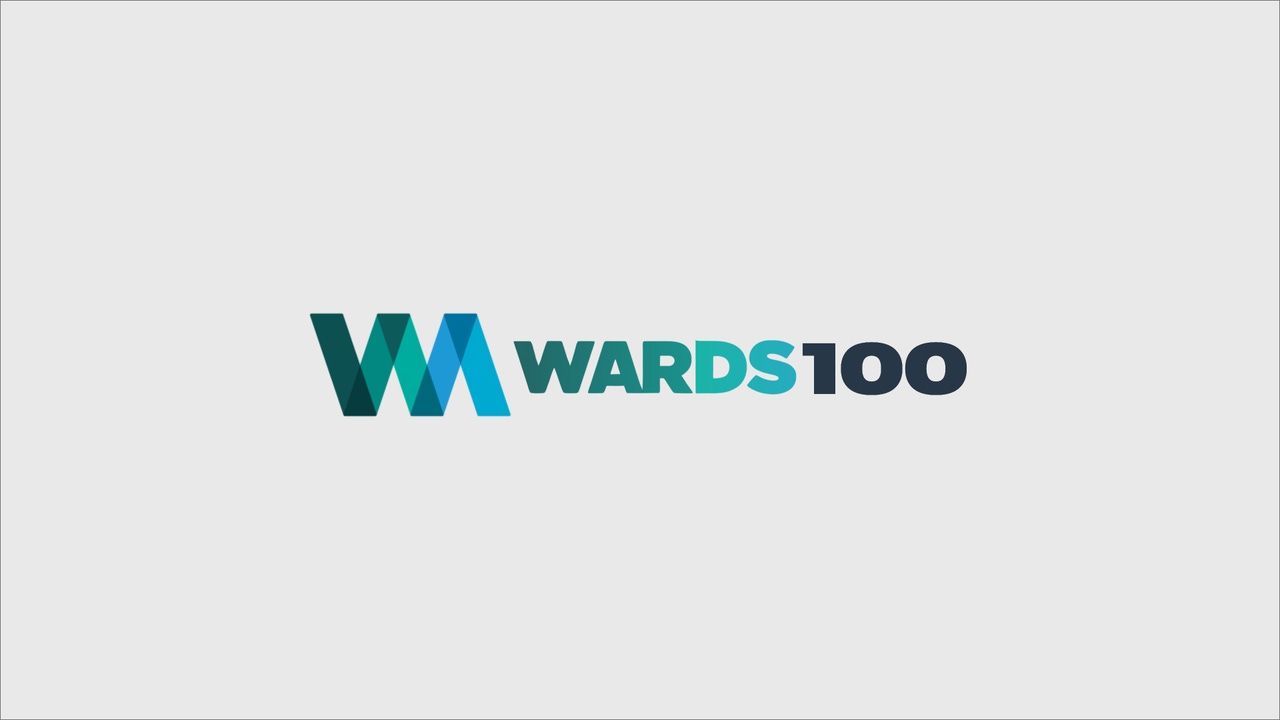
Imagine if a film couldn't win an Academy Award unless it provided the studio with a major cost savings. Sound ridiculous?
Sure. Oscar winners frequently are big money makers, but ultimately - despite all the hype, politics, and high-level maneuvering - the judges reward quality acting and filmmaking. Movies that go horribly over budget and are dogs at the box office still win Oscars.
Even in shallow, venal Hollywood, quality and integrity count for something once a year.
If bean counters handed out Oscars there would be no lavish Academy Awards ceremony, only a few "suits" congratulating each other. Not long thereafter all good movies would be foreign-made and have subtitles.
I bring this up because I think another wonderful event, the annual Society of Plastics Engineers awards banquet - sometimes called the "Oscars of the plastics industry" - seems in danger of falling prey to the cost-cutting fervor overrunning the automotive industry.
I have been judging these awards since the mid-1980s and I have seen them slip down this slope before during the era of infamous cost-cutter Jose Ignacio ("Inaki") Lopez. I remember one marathon judging session in particular where the only "innovation" of almost 30 finalists was a cost reduction of some kind. Sorry if I sound idealistic, but I think cost savings should be a fringe benefit of true innovation, not the sole purpose. Fortunately real innovations in automotive plastic parts have made a comeback.
I'm certainly not trying to diminish the achievements of this year's winners. I'm just trying to prevent the specter of Dr. Lopez from haunting these awards once again. Please, let's not consider innovation that doesn't pay for itself somehow less worthy.
Here's a brief rundown of this year's winners:
n A new composite bumper I-beam used in the '99 Mitsubishi Galant won the exterior category and the SPE's Grand Award. It replaces roll-formed steel used by most automakers and is claimed to be 35% to 45% lighter than conventional steel bumper beams. It's also said to be 25% less expensive to produce because the design integrates mounting tabs for fascia and attachment stays that slide into the car's frame rails, lowering tooling costs. The bumper beam also doesn't permanently deform like steel when it's rammed into a pole. Developed by Azdel, a joint venture company formed by GE Plastics and PPG Industries, the part is compression molded by Continental Structural Plastics.
n Chassis: (two-way tie) A steering column support bracket made of glass reinforced nylon is the first ever such application for plastics. It replaces a magnesium part on Chrysler minivans. The support bracket is 10% lighter than even lightweight magnesium and saves the OEM $3 million per year plus an initial $150,000 in tooling costs. It's made of DuPont Zytel and molded by InMold Corp.
The clutch pedal and bracket assembly on the new GMT 800 light trucks is the other winner in the chassis category. It replaces stamped steel parts, and offers a cost-efficient snap-fit assembly of the pedal and bracket by merely depressing the pedal when the truck is ready to be driven off the assembly line. The first such component used in North America, it is manufactured by Florida Production Engineering from BASF's Ultramid nylon 6 resin. The molded-in color nylon pedal assembly offers lower pedal movement free-play than metal assemblies and 65% weight savings.
n Materials: If you thought there was something different about the leather-like covering on the instrument panels of the Chrysler Concorde and LHS/300M models, you're right. The material is a new patented polymer developed by Textron Automotive and Bayer Corp. after eight years of research. An aliphatic thermoplastic urethane called Texin, the material - unlike vinyl - does not use chlorine in its manufacture, reduces window fogging and offers better resistance to heat and sunlight. It also allows for the latest seamless passenger side air bag door design.
n Process: Molding complicated parts with long glass reinforcement fibers that add strength always has been difficult because the fibers usually break during the rigors of molding. Composite Products Inc. impressed the judges with its new process that disperses long glass fiber bundles into the resin without breaking them for optimum part strength, good appearance and lower costs. The process makes possible a new disappearing door frame rail design for Jeep TJ soft top door rails that allows them to be less conspicuous when the top is folded down, and provides a better fit when the vinyl top is up. Montell supplies the polypropylene resin. Magna Decoma supplies the finished part.
n Powertrain: The all-plastic integrated air induction system for the 7.4L diesel on Ford Motor Co.'s '99 F350 light truck won praise from the judges for its novel design. The part incorporates an air cleaner tray and cover, resonator and clean air tube, and routes clean induction air around the battery case to keep it cool. This extends battery life without using separate air cooling ductwork. Developed by Visteon, it's made of polypropylene supplied by Ferro Corp. and is expected to save Ford more than $2 million a year in manufacturing costs.
n Interior: A double-walled blow-molded polypropylene load floor and spare tire cover for the '99 Jeep Cherokee conceals the spare tire for greater usable cargo space. Compared with wood, metal and injection molded plastic alternatives, the single blow-molded reinforced polypropylene part allows molded-in attachments on the bottom side while preserving a smooth and flat exposed surface. Carpet is molded onto the surface and trimmed during the molding cycle. The double-wall structure muffles noise and damps vibration. The part is made of PolyCom's Spartech 30% glass reinforced polypropylene. Freemont Plastic Mold designed the tooling and Lear Corp. supplies the final parts to Chrysler.
n Environment: A new process for removing paint from plastic developed by American Commodities Inc. enables Visteon to recycle painted scrap parts and turn used thermoplastic olefin bumpers into new bumper fascia. The reclaimed material is reused in production at blends ranging from 20% to 100%. Visteon now is recycling 1 million lbs. (454,000 kg) of painted TPO parts a year, which saves $250,000 in new material and landfill disposal costs.
Read more about:
1998About the Author
You May Also Like