PM Industry Looks to New Transmissions for GrowthPM Industry Looks to New Transmissions for Growth
New advanced transmissions with six speeds will provide the powder metal industry the most near-term opportunities for growth.
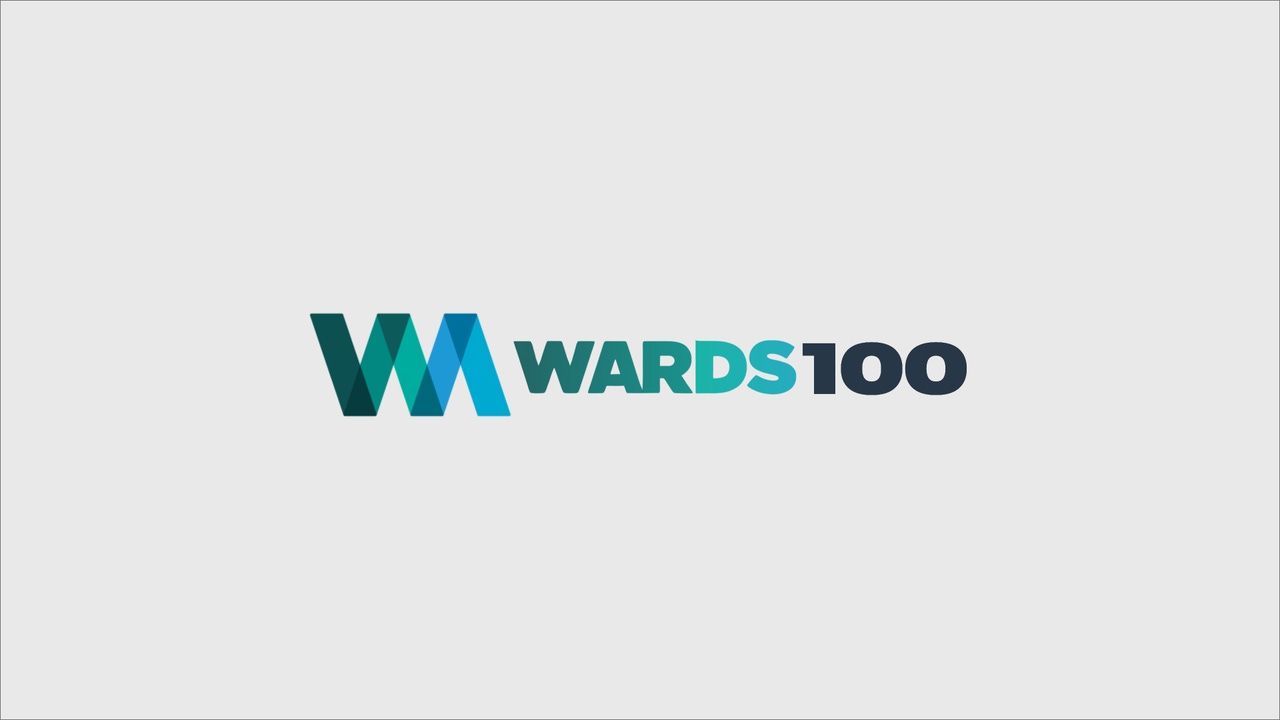
DETROIT – Squeezed by rising costs and falling production volumes at General Motors Corp. and Ford Motor Co., North American powder metal producers and fabricators are looking to new 6-, 7- and 8-speed transmissions to help boost their fortunes in the auto industry.
Analysts at Swedish powder metal producer Hoeganaes Corp. expect per-vehicle use of their specialized parts to increase steadily in the North American Free Trade Agreement region through 2010, but the falling market share of the world’s two biggest users of the technology – GM and Ford – is slowing overall poundage growth.
Typical U.S. Big Three cars contain about 43 lbs. (20 kg) of PM parts, while vehicles designed in Europe and Japan contain about 20 lbs. (9 kg) and 18 lbs. (8 kg), respectively.
PM parts are made by pouring metal powder into molds and then squeezing and heating the material in special presses to create a solid metal part with very precise dimensions.
The process is used most often in automotive to produce complex gear or bracket designs to reduce the high degree of secondary machining operations required when using conventional materials.
Detroit’s Big Three have embraced the process because parts can be produced so close to the final shape and dimensions. It eliminates manufacturing steps that require extra manpower and equipment. This is particularly advantageous components with many complex parts, such as automatic transmissions, that also are manufactured in high volume.
Powder metal is suited for complex gears and brackets.
Eric Boreczky, manager, market development-Hoeganaes Corp., tells Ward's during the SAE World Congress here that Asian auto makers have been slower to adopt PM parts because they are reluctant to move away from their well-established base of keiretsu suppliers and because of limited availability of powder metals and high-quality PM part fabricators in the region.
European auto makers have been slower to transition because they traditionally have considered intricately machined parts superior to PM parts, an impression that no longer is accurate, Boreczky says.
New material and processing technologies are enabling PM producers to make denser, stronger parts more cost-effectively, and that is creating more opportunities among both Detroit-based and foreign-based auto makers, Boreczky says. Indeed, he is predicting PM parts to make big gains in Asia and Europe after 2010.
But the biggest near-term PM growth is in the area of transmission carrier frames, parts that strengthen the transmission case structure and weigh several pounds apiece. Typically, there is one carrier frame for each gearset, so the trend to 6-, 7- and even 8-speed transmissions is a welcome development, Boreczky says.
GM and Ford are collaborating in the development of one 6-speed automatic transmission, for front- and all-wheel-drive drivelines, and both are transitioning to a variety of new 6-speed automatic transmissions, which eventually will amount to millions of units of production annually.
Likewise, the increasing popularity of continuously variable transmissions in Japan and so-called automated manual transmissions in Europe are good growth opportunities for PM parts in the future, Boreczky says.
Read more about:
2006About the Author
You May Also Like