Productivity Not Pink SlipsProductivity Not Pink Slips
U.S. productivity is soaring, but many believe it's only because workers now are doing the jobs of laid-off co-workers in addition to their own. That's certainly the case in many instances, but some companies have figured out ways to coax higher productivity from their workforces without making them work harder or eliminating jobs. An example is Johnson Controls Inc.'s Automotive Group, which in December
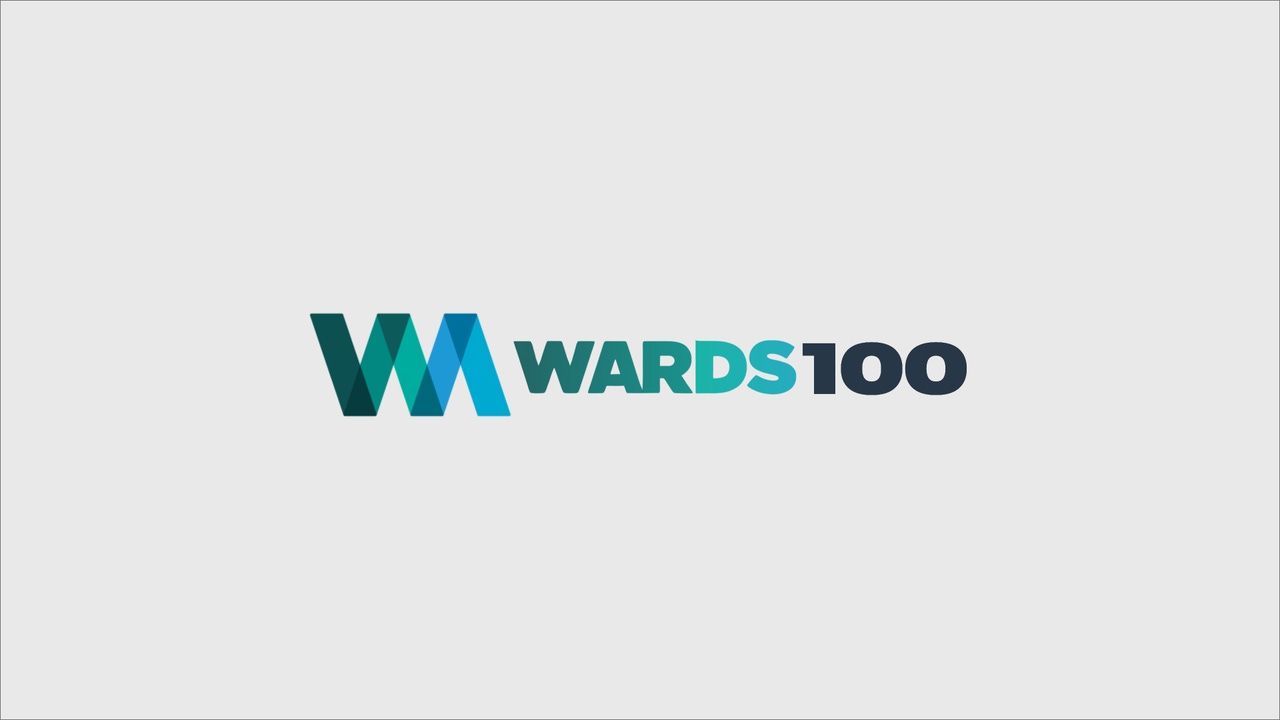
U.S. productivity is soaring, but many believe it's only because workers now are doing the jobs of laid-off co-workers in addition to their own.
That's certainly the case in many instances, but some companies have figured out ways to coax higher productivity from their workforces without making them work harder — or eliminating jobs.
An example is Johnson Controls Inc.'s Automotive Group, which in December wrapped up its annual Team Rally event at Disney World in Orlando.
After competing on a regional level, 15 team finalists, composed of about 10 plant-floor workers each, were flown in from as far away as South Korea and Eastern Europe to compete in a day-long event where they vie to win top honors.
The teams then stay the weekend at a resort hotel and are given free passes to Disney World — courtesy of their employer.
With music blaring and a strict time limit, each team runs through an elaborately choreographed — and often humorous — skit detailing how they used sophisticated lean manufacturing and Six Sigma quality-control techniques to solve productivity, safety, quality or cost issues.
Like the United Nations, presentations are translated in eight languages via headphones.
Each ends with a summation of benefits and cost savings, and a listing of contact names. That's because “shareability” of benefits is key to winning.
Such an event seems extravagant in an era when many automotive suppliers say pricing pressure from OEMs is driving them out of business — that is, until you feel the electricity in the air and see JCI's results: $500,000 or more in annual savings per team, millions overall.
The ideas then are spread throughout the company's 265 worldwide engineering and manufacturing facilities, JCI officials say. But guess what — none of the improved productivity came from layoffs.
Getting plant-floor workers involved in teams to do double duty as efficiency experts is something every corporation dreams about. Most fail because they can't get employees to buy into the process. And that's because they don't offer a big enough reward.
Through 10 years of consistent effort and putting its money where its mouth is, JCI has managed to demonstrate to employees that it is empowering them to use lean manufacturing methods and tools such as Six Sigma not just to save the company money, but to improve the quality of their own work life — and in some cases save jobs.
Improving work life and job security were the motivational factors I saw operating in Orlando last month. A free trip to Disney World was just icing on the cake.
“The companies making the biggest complaints about OEM givebacks are probably the ones that are not making this kind of investment in their people,” says Jerry Beaubien, vice president and general manager of JCI's Mercedes-Benz business unit.
Whether or not that's true, corporate America needs to take a close look at JCI's Team Rally before it hands out its next round of pink slips.
Read more about:
2004About the Author
You May Also Like