Waste-Heat Recovery System Wins Top Australian Honors
SAE-A says two patent applications have been filed for Over7 and one auto maker has adopted the technology for its next generation of engines.
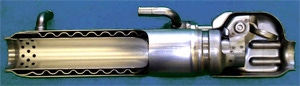
Technology that reduces the frictional losses of engines by redirecting exhaust heat and increasing heat transfer into the engine oil is the top winner at the 2011 Australian automotive engineering excellence awards in Melbourne.
The Society of Automotive Engineers-Australasia names Frank Will, senior lecturer at Deakin University, the gold medal winner for his Over7 waste-heat recovery system.
Over7 waste-heat recovery system.
Because the system greatly reduces warm-up time, it cuts engine wear by more than 96%. SAE-A says two patent applications have been filed for Over7 and the technology has been adopted by one auto maker for its next generation of engines and reviewed by other global vehicle manufacturers.
Tests confirmed fuel consumption reduction of more than 7% and emission reductions of up to 30%, the engineering group says.
“This modification of the lubrication system includes simple piping, a valve and a new heat exchanger, and will pay back the investment in less than one month if installed in the factory,” the SAE-A says in a statement.
“If the system is implemented in only 1% of the Australian passenger car fleet, 3.9 million gallons (15 million L) of fuel will be saved every year and carbon-dioxide emissions will be reduced by over 36,000 tons (32,650 t) a year.
“This system works even better as powertrains become more efficient, for example with hybrids, diesel engines (and) downsized turbocharged direct-injection engines.”
SAE-A judging panel chairman Bill Malkoutzis says the number and quality of entries increased this year as the shadow of the global finance crisis has passed over local vehicle engineering and new projects are moving forward.
The innovation and passion evident in the 2011 entries is reassuring, he says.
“We know the face of the vehicle industry is changing, with local manufacturing shrinking and imports increasing to over 80% of Australia's 1 million vehicle sales a year. Even imports of components have now increased to 44% of all parts used in Australian-made vehicles.
"Growth in demand for more environmentally friendly vehicles presents opportunities and challenges for Australian automotive engineers,” Malkoutzis adds. “The correlation between the consumers' demands and the engineering projects entered in the awards this year was clear to see.”
The silver award goes to SMR Automotive Australia and the University of South Australia for a lightweight integrated plastic rearview mirror.
The market-ready mirror is expansion-compression molded polycarbonate with a multi-layer nano-engineered thin film coating system creating the reflective surface.
Elimination of the glass reduces mirror reflector weight by 50% and results in a reduction in greenhouse-gas emissions of up to 440,924 tons (400,000 t) of CO2 over five years, and reduces overall mass of the mirror assembly by 15%.
The technology also cuts the number of components in the mirror assembly and simplifies the manufacturing process, while allowing greater freedom of mirror design. It improves safety in a crash situation because the polycarbonate does not shatter like glass.
The integrated plastic mirror has been approved by a North American customer for launch in 2012 and is being marketed to SMR customers in Asia/Pacific, Europe and the U.S., the SAE-A says.
GM Holden Virtual Manufacturing Engineering Manager Gregory Linke wins the bronze award for his bottleneck indicator tool (BIT) software system for manufacturing optimization.
BIT builds on the theory-of-constraints concept to identify bottlenecks in complex manufacturing processes. The BIT algorithm and processing methodology is based on real-time computer analysis of the workflow through the system's workstation buffer areas where one process is completed and another begins.
The BIT requires only easily validated buffer contents data, making data acquisition and calibration readily achievable. The benefits of BIT include accuracy, ease of calibration, low deployment cost and negligible maintenance.
The BIT package identifies hidden bottlenecks missed by other systems and includes a toolbox of reports that deliver high levels of detail in a user-friendly Web browser visual format.
During the initial 3-month deployment at GM Holden's South Australian vehicle assembly plant, volume increased by 60 units a day. The BIT software has been identified as a Best GM Practice and is being considered for global deployment.
About the Author
You May Also Like