We're No.2!We're No.2!
Materials experts saw it coming for years, but the Aluminum Assn. presented new research recently that confirms the lightweight metal has displaced iron as the second most intensively used material in vehicle production worldwide. The study, commissioned by the Aluminum Assn., finds an average 280 lbs. (127 kg) of aluminum per vehicle produced in the world's three major markets: North America, the
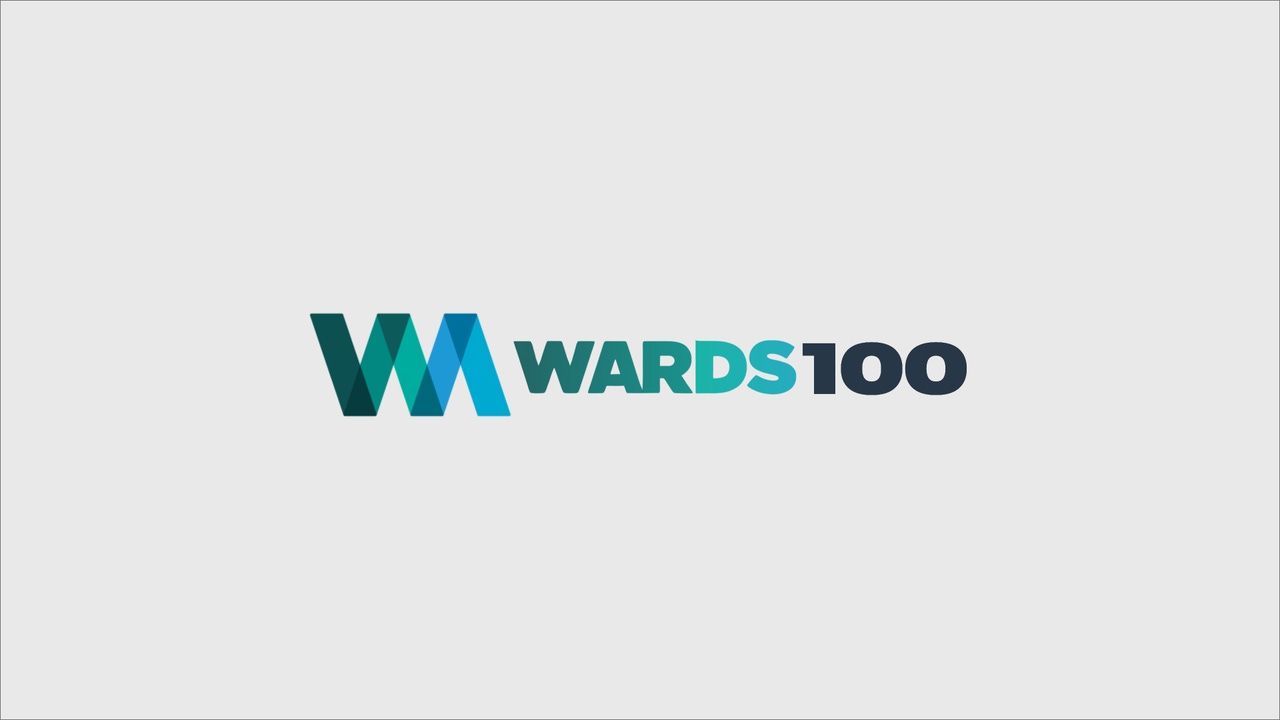
Materials experts saw it coming for years, but the Aluminum Assn. presented new research recently that confirms the lightweight metal has displaced iron as the second most intensively used material in vehicle production worldwide.
The study, commissioned by the Aluminum Assn., finds an average 280 lbs. (127 kg) of aluminum per vehicle produced in the world's three major markets: North America, the European Union and Japan. Together, the regions represent about 75% of global output.
In North America, which has the largest light vehicles, the average aluminum content per vehicle is slightly higher, at 319 lbs. (144 kg), representing 16% growth since 2002.
Consultant Richard Schultz, who conducted the research for Ducker Worldwide, a market intelligence firm, estimates iron content in North America averages about 300 lbs. (136 kg) this year, down from 308 lbs. (139 kg) in 2004.
For every new application for aluminum, Schultz says an iron or steel component is displaced. Aluminum is posting its gains in engine blocks, wheels, suspension control arms and steering knuckles.
On a global average, aluminum 4-cyl. engine blocks weigh about 44 lbs. (19 kg), compared with 66 lbs. (30 kg) for a V-6 and 88 lbs. (40 kg) for a V-8, Schultz says.
In iron, the same blocks weigh roughly twice as much but are half the price.
In North America, Schultz estimates 52% of blocks are aluminum, with the remainder iron. Some 85% of North American cars have aluminum engine blocks today, a figure expected to reach 90% penetration within five years, Schultz says.
Likewise, 25% of light trucks have aluminum blocks, and Schultz estimates that number will reach 55% within five years.
But iron, the bedrock material for automotive powertrains for a century, continues to hold fast to its share of the massive North American light-truck sector.
Iron blocks are used for most of Ford Motor Co.'s 4.6L and 5.4L V-8s, most of General Motors Corp.'s 4.8L, 5.3L and 6L V-8s and all of Chrysler Group's 5.7L Hemi V-8s, although certain versions of the Ford and GM blocks are made of aluminum.
Since 1973, when aluminum content averaged 81 lbs. (36 kg) per vehicle, the metal has enjoyed more than 30 years of uninterrupted annual growth in terms of automotive usage in North America.
By unit volume, wheels are the most prevalent aluminum automotive component, as the world's three major markets will use some 98.5 million of them this year, compared with 54.5 million cylinder heads; 43.4 million suspension arms and links; 42.9 million transmission cases; and 22 million engine blocks.
With aluminum cylinder heads, blocks and other ancillaries, engines are, by far, the most aluminum-intensive component on vehicles today.
Aluminum content on engines averages 114 lbs. (52 kg) in North America, 89 lbs. (40 kg) in Europe and 101 lbs. (46 kg) in Japan, according to the study.
In Europe, about half of all new vehicles are sold with diesel powerplants, and most diesel engine blocks continue to be manufactured in iron because of inherently high combustion pressures. Still, Schultz says about 24% of European diesel engine blocks are made of aluminum.
This year, some 12 billion lbs. (5.4 billion kg) of aluminum will be used in vehicle production, including 570 million lbs. (258 million kg) of sheet aluminum for auto bodies, instrument-panel structures and closure panels, the study says.
Aluminum industry executives play up the fuel-economy benefits for auto makers choosing lightweight aluminum.
A 10% weight savings, for instance, translates into a 9% improvement in fuel consumption, says Misha Riveros-Jacobson, president of Alcoa Advanced Transportation Systems.
And she says aluminum body structures, while lighter, do not compromise structural integrity and safety.
“Pound for pound, aluminum can be stiffer than steel,” Riveros-Jacobson says. In a collision, aluminum can absorb twice as much crash energy as steel, she says. For the foreseeable future, Riveros-Jacobson says aluminum content per vehicle should continue to climb by about 3% annually.
Because of the weight advantage, Martha Finn Brooks, chief operating officer of aluminum roller Novelis Inc., says she wants the Aluminum Assn. to conduct another study of the fuel-economy gains that can be achieved with an aluminum-intensive hybrid-electric vehicle (HEV).
The aluminum industry urges auto makers to consider its metal for future HEVs but often encounters resistance within OEM purchasing departments, because aluminum is much more expensive than steel.
Processed steel sells for about $0.37 per pound, compared with $1.50 per pound for processed aluminum.
But industry officials say aluminum-intensive cars and trucks can be economically viable because savings at the pump can offset upfront material costs.
The Jaguar XJ, with an aluminum-intensive structure, is longer, taller and wider than the model it replaced but weighs 400 lbs. (181 kg) less, Finn Brooks says.
Although aluminum has weight advantages, steel nonetheless is making significant gains through increased applications of high-strength formulations.
Still, Schultz, a former aluminum industry executive, says high-strength steels only go so far. “You can hit a lot of singles with high-strength steel, but you need aluminum if you want to hit doubles, triples and homers,” he says.
The steel industry need not worry about aluminum threatening its No.1 position in automotive materials anytime soon.
The average vehicle contains some 1,800 lbs. (816 kg) of steel.
About the Author
You May Also Like