Workers’ Role Expanding as Wages ContractWorkers’ Role Expanding as Wages Contract
“We assume that the best executives cost a lot more money, and the best workers we get for a lot less money,” says labor expert Harley Shaiken. “There’s something wrong with that logic.”
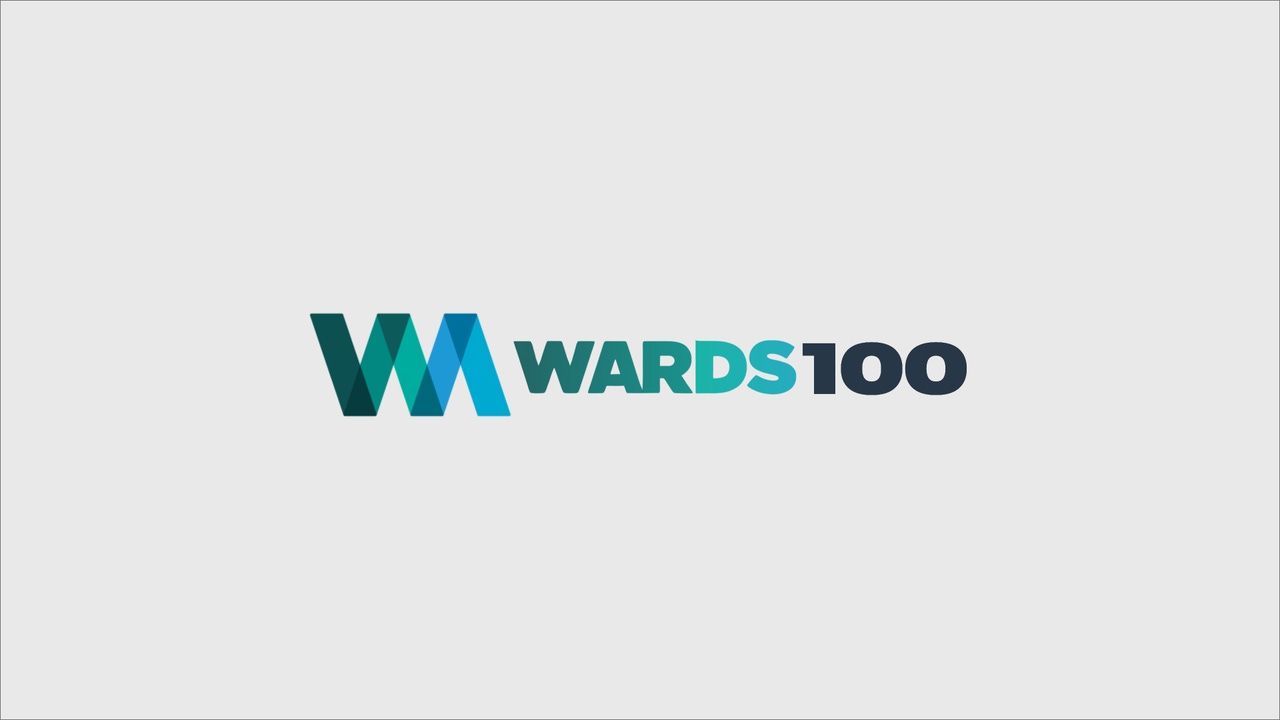
Special Coverage
State of the Industry: North America

Bargaining between the United Auto Workers union and Detroit auto makers routinely is heralded with hyperbole.
But when the two sides sit down next year to negotiate a new collective agreement, it may be impossible to overstate the event’s significance.
UAW members must have “major share” of employers’ success, Bob King says.
New tensions are emerging as a downward trend in wage and benefit packages belies the increasing contributions hourly workers make to improve product quality – efforts that are paying off on influential third-party report cards.
Detroit auto makers now are openly and formally engaging hourly workers to affect process improvement in a manner long embraced by high-quality, non-union transplants, where lower labor costs are celebrated.
“There’s sort of an odd paradox here,” says Harley Shaiken, noted auto industry labor expert and professor at the University of California, Berkeley. “We assume that the best executives cost a lot more money, and the best workers we get for a lot less money. There’s something wrong with that logic.”
Next year’s UAW talks with General Motors Co., Ford Motor Co. and Chrysler Group LLC will unfold against the backdrop of a new reality.
Ford enters 2011 solidly in the black, while GM and Chrysler, still shackled by the remnants of landmark bankruptcies, are flirting with profitability as the once-frosty economic climate shows signs of gradual warming.
Meanwhile, the U.S. industry is a shell of its former self.
Memories of annual sales in the 17 million-range are distant and fuzzy as volumes slowly ratchet up toward 2011’s forecast range of 13.2 million, according to Ward’s.
The industry landscape is home to 42 assembly plants today, compared with 62 just 10 years ago.
Saying their names evokes a solemnity reserved for war dead. Norfolk. Janesville. St. Louis North. St. Louis South. NUMMI.
Also gone are the paychecks of some 209,000 production workers, according to the U.S. Bureau of Labor Statistics.
Hourly workers at GEMA must have advanced education.
Including parts suppliers, the auto sector employs about 666,000 people, down from 875,000 in 2008 and well off 2000’s total of 1.3 million, the U.S. industry’s peak.
The situation’s gravity is not lost on Chrysler’s Sergio Marchionne. The affable CEO grows quiet when asked if his company has any wiggle room to boost the fortunes of its workers, who, like their cross-town counterparts, have sacrificed wages and benefits to ensure their employer’s competitiveness.
“It is premature to have this discussion,” Marchionne says on the sidelines of the recent L.A. Auto Show.
But the union, under new leadership, is not so reticent.
“Our members have made huge sacrifices to keep these companies viable,” says UAW President Bob King. “Companies are doing really well. Our members have to have a major share.”
King succeeds Ron Gettelfinger, who retired in June after presiding over one of the most tumultuous periods in the UAW’s storied history. Among the concessions made to keep assembly lines humming for Detroit auto makers was the establishment of a lower wage tier for new hires.
It is a pay structure that has been used effectively at non-union U.S. plants such as Nissan North America Inc.’s Canton, MS, assembly site and Hyundai Motor America’s facility in Montgomery, AL.
But as UAW members come closer to a day of reckoning, when theory becomes practice in the form of smaller paychecks, there has been a backlash.
Workers at GM’s plant in Orion Township, MI, future production site of two breakthrough small-vehicle programs, recently protested after learning they have been targeted for second-tier wages to preserve margins on the pending Buick Verano and Chevrolet-brand platform-mate.
Job preservation is the payback. But King suggests there are limits to such a tradeoff.
“What guarantees future product commitments in my mind is having a total cost analysis of making the best product at the best price for consumers; understanding who your competition is; understanding you have to provide vehicles to the consumers that are competitive,” he tells Ward’s in an exclusive interview.
King also tackles the prevalent belief workers, not management, caused the collapse that compelled the Bush and Obama Admins. to rescue private industry with taxpayer money.
“The main reason for the demise of the auto industry was poor product decisions, poor quality, not giving the customer the best product at the best price,” he says. “Had we continued to do that we wouldn’t have been in the crisis.
“There’s so much knowledge and experience and skill in our membership, the smart people in companies realize they want to tap into that,” he adds, recalling a legendary tale from the annals of UAW bargaining.
Irving Bluestone, UAW vice president in charge of the union’s GM bargaining unit, suggested in the 1970s that auto makers enlist workers to help improve product quality.
“The company said, ‘That’s none of your damn business,’” King says.
“Fortunately, employers are more enlightened. They understand if they want to be viable they’ve got to (build) the best-quality product. And they understand the best way to do that is with a fully engaged workforce.”
Ford agrees. “Our conversations all focus around keeping Ford competitive,” Mark Fields, president-The Americas. “We’re always making sure we communicate with our entire workforce around our plans, our challenges and our status against the plan (while) engaging the workforce.”
Shaiken cites Ford’s success in recent third-party vehicle testing among the benefits of tapping the shop floor for ideas. Some 90% of its Lincoln and core-brand models recorded at least average reliability scores in Consumer Reports’ 2010 auto survey.
Two of its products, the Ford Fusion Hybrid midsize sedan and Ford Flex cross/utility vehicle, achieved the top spot in their respective segments.
“When we talk today, it isn’t the conversation of five years ago when the perception was Toyota was at one end of the scale and the domestic industry was hopelessly behind,” Shaiken says, noting an even more pragmatic reason for leveraging the institutional knowledge of workers.
“If you’re managing $400 million worth of equipment, the role of a worker is critical,” he says.
With the production launch of its new Pentastar V-6, Chrysler for the first time enlisted hourly personnel to participate in the program’s Process Failure Effect Mode Analysis.
The result? A discovery that bolts could, during the assembly process, fall into the engine block and go undetected, meaning shoddy vehicles could fall into customers’ hands.
Solution? An hourly worker designed a shield that now is fitted around the block to protect it from mishaps during a particular assembly phase.
“Our members take tremendous ownership and pride in the quality of the vehicles that we’re building,” King says. “If a company starts to get off-track or a local manager starts to get off-track and (starts) to push quantity over quality, our members push back really hard. They consider themselves partners in making sure we have the best quality.”
And as vehicles get more sophisticated, so do the tools used to assemble them, prompting the question: Will OEMs demand more of future workers in terms of education or skills?
Chrysler requires workers at its Global Engine Mfg. Alliance plant in Dundee, MI, to have a degree or skills certificate. Tom Zimmerman, UAW chairman at the site, tells Ward’s he sometimes feels like he’s “part of an all-star team.”
The plant now is building the Fiat-designed 1.4L 4-cyl. FIRE engine with advanced MultiAir valve-actuation for the Fiat 500 minicar due out in January.
King is cool to the notion that GEMA-like employment requirements should become the norm instead of the exception.
“There are very knowledgeable, very smart, very skilled people working in our facilities – some who, because of family situations, weren’t able to get a formal education,” he says. “What you want is a workplace (where) people are motivated and want to build the best product at the best price and really have a voice in decision-making.”
Such compassion hints at an ideological bent that runs counter to contract negotiations, an exercise rigidly focused on cost vs. benefit.
King admits it’s a tightrope-walk, and he does not apologize.
“The UAW’s going to be very active in helping workers around the world improve their wages and benefits,” he says. “What you really want to do is take wages and labor costs out of competition. You want every employer to pay the same. Then your members can have a decent standard of living.
“Companies can be profitable and viable. When you have someone you’re competing with paying far lower wages and benefits because they’re coming from an undeveloped (region), then that can create really unfair competition, and we have to deal with that. And we are.”
King’s counterpart, Canadian Auto Workers President Ken Lewenza, echoes this sentiment.
“Historically, the auto industry provided good wages and good benefits, and $14 an hour doesn’t allow you to buy the vehicle you manufacture,” Lewenza says, referring to the hourly wage OEMs have pegged for new hires.
The CAW dodged a UAW-style 2-tier wage settlement in its bargaining, but it made other concessions to secure job-saving OEM investments. The CAW’s agreement expires in 2012.
Might transplants lower their wage rates further to maintain the labor-cost gap that gave them a competitive advantage for so long?
“The UAW concessions are no doubt a factor, but the forces that could depress transplant wages more directly are the new low-wage plants the transplants have built,” Shaiken says, referring to Toyota Motor Engineering & Mfg. North America Inc.’s new plant in Blue Springs, MS.
Production at Blue Springs is set to begin next year. Media reports say pay rates are expected to range from $15 to $25 an hour, which is higher than the area’s average manufacturing wage of $13 an hour.
Despite the conflicting forces confronting workers and their employers – the challenging economy, ever-increasing competition, wider shop-floor accountability – King is confident in the future.
“I am optimistic,” he says. “We know the formula. When you build a global middle class, people buy products and goods and services. That’s a society that you want to be part of building.”
Read more about:
2010About the Author
You May Also Like