Working Smarter, Not Harder to Optimize InventoryWorking Smarter, Not Harder to Optimize Inventory
One of the many benefits of digital transformation in the factory is the high-performance culture that using advanced technology can create. With the right tools, teams can stay productive and connected across factory operations as people continue to work remotely.
April 29, 2021
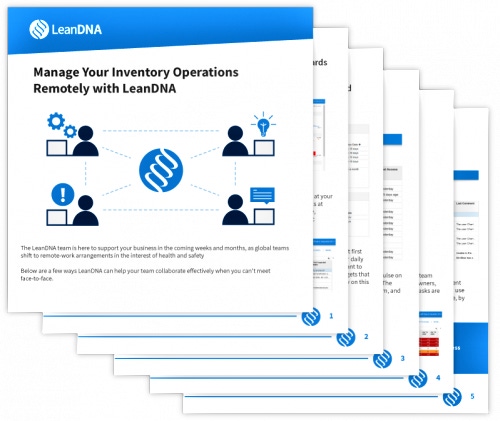
The pandemic has served as a catalyst for change for factories across the globe. As automotive and specialty transportation manufacturers continue to offer remote work to employees, factories are getting creative and transforming operations to ensure collaboration, continuity and resilience.
Whether through smart manufacturing technology or virtual reality, manufacturers are tapping into the value of automation and technology to create a contactless yet highly effective factory. One area that’s emerging as ripe for digital transformation: factory operations management. This is where manual activities and analysis can be automated to optimize inventory and improve on-time delivery.
Remote Work: Magnifying Factory Management Challenges
The concerns typically top of mind for automotive manufacturers are amplified when working with dispersed teams. Mass customization and a heavy reliance on global suppliers put agility, flexibility and visibility at the center of a strong inventory optimization strategy.
But remote working arrangements make it harder for teams to get quick insight into what is causing shortages, as well as other inventory and supplier performance issues. It’s also more challenging to collaborate both internally and with suppliers to handle unpredictable demand changes and stress on the supply chain.
Alignment prioritization and accountability are foundational for tackling these complex issues. Teams typically rely on offline, disparate data sources such as spreadsheets and manual reports to try and optimize inventory and manage shortages. These are inefficient and ineffective in traditional office environments, more so within a remote workforce.
The age-old problem of tracking down, sharing, reviewing and collaborating around inventory information is exacerbated. More time is spent on asking for the most recent reports and emailing back and forth than on addressing the root causes of inventory issues.
And when teams eventually get their hands on the right data, employees don’t always know which tasks to knock out first to achieve the biggest impact on excess inventory and customer delivery. Managers don’t always know if their teams, which may be located across the country, are executing on the right priorities.
Overseeing and tracking work processes, especially across large teams of 30 people or more, can be a constant struggle for even the most experienced and perceptive team leaders.
Industry-Voices-bug (002)_92
2021: Ushering in the New Digital Transformation ImperativeOne of the many benefits of digital transformation in the factory is the high-performance culture that using advanced technology can create. With the right tools, teams can stay productive and connected across factory operations as people continue to work remotely. In fact, McKinsey reports organizations with more advanced technologies have navigated the COVID-19 crisis better than their less tech-savvy peers.
Equipping teams with the technology to confidently act, adjust and decide on the fly is core to building agility, resiliency and accountability into factory operations, especially as permanent virtual work options become more likely.
Tapping tools that create a single, shareable view of supply chain information and standardize and automate work processes enables teams to streamline their efforts, focus and mobilize in stressful times. These advanced tools allow every team member to clearly understand the current state of inventory in the factory, critical shortages, supplier status and performance, the urgent actions they need to take to resolve issues, and more.
Every manager has more control over team performance with insight into wins, risks, results and progress on tasks and actions, where workloads may need to be rebalanced, which team members need support, and more.
Research shows productivity gains of 30%-40% await the companies that invest in digital infrastructure and data integration. The transformation also empowers employees to focus on more strategic work, which has a direct impact on manufacturing effectiveness, talent retention and business growth.
Richard Lebovitz-LeanDNA
Inventory Optimization Goes Virtual
With remote work here to stay in some capacity even after the pandemic lifts, automotive manufacturers can take comfort in the fact that operating with dispersed teams doesn’t mean sacrificing productivity, efficiency and performance. In fact, flexible work environments can be a differentiator for companies that have the right digital infrastructure.
By making investments incrementally – and in critical areas such as inventory optimization – the factory can find resilience and success while keeping their employees safe, supported and satisfied.
Richard Lebovitz (pictured above, left) is the founder and CEO of LeanDNA, a provider of factory-focused inventory optimization solutions.
About the Author
You May Also Like