ZF Launches Energy-Saving InitiativeZF Launches Energy-Saving Initiative
The German supplier is taking action now as it anticipates rising energy prices and more-stringent environmental regulations.
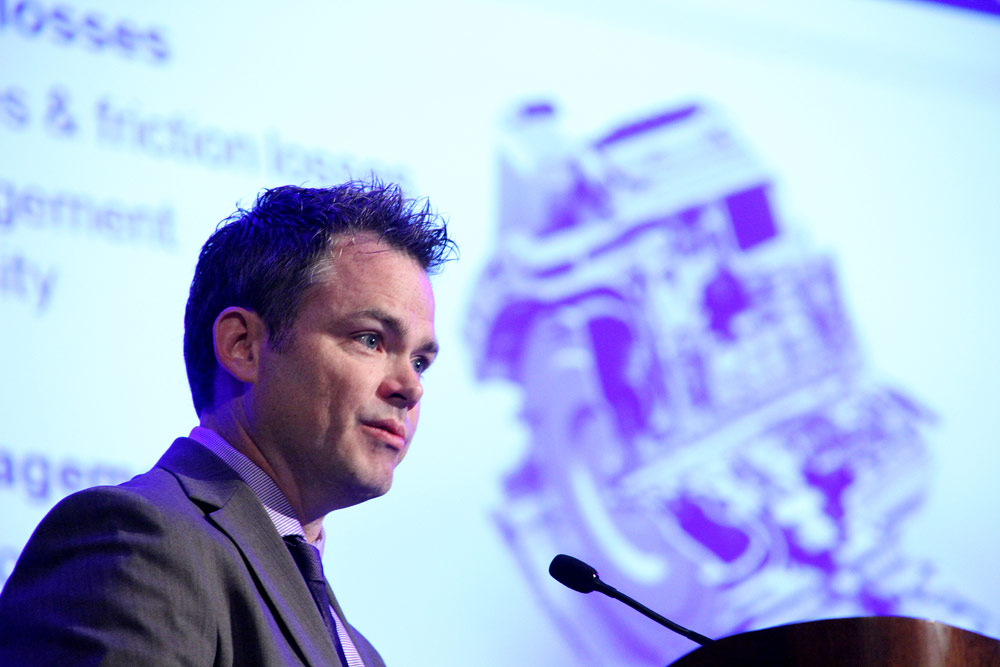
TRAVERSE CITY, MI — ZF Friedrichshafen is in the midst of its Sustainable Reduction Plan, with the goal to reduce energy consumption at its global facilities 20% by 2015 compared with 2010.
The German supplier last year decided energy consumption not only was a sound business strategy to reduce cost, but also a social responsibility, says Kelly Biers, director-continuous improvement, ZF North America.
“The business environment of that time led us to be more energy-conscious,” he says during the CAR Management Briefing Seminars here.
Biers says ZF wants to stay one step ahead of constantly changing laws and legislation dictating energy usage and output of harmful emissions, noting increasing rates also played a role in the supplier’s decision to reduce power consumption.
Natural resources such as water and oil will become increasingly expensive, and in some nations, such as China, energy is scarce.
“Sometimes (in China) they give you a call a day ahead and say you need to shut down tomorrow due to an electrical power shortage,” he says. “That can obviously make your production schedule a little difficult.”
After the 2011 tsunami and earthquake that devastated portions of Japan, causing more than 15,000 deaths and severely damaging nuclear reactors, the island nation and others reevaluated their nuclear-power programs. That reinforced ZF’s dedication to reducing energy consumption.
“Germany had to take a hard look at their nuclear program, and when they did they decided to shut down eight plants immediately and are going to shut down all of them by 2022,” Biers says. “So ZF wanted to be ahead of the curve before that starts to happen.”
ZF’s OEM customers also are demanding reductions in energy and output of emissions, which Biers says sometimes is frustrating but ultimately beneficial.
In developing its energy-reduction strategy, ZF brass came up with 40 ideas, implementing 27 that were facility-related and six that were process-related.
The strategies were first employed at ZF’s Gainesville, GA, facility, which produces wind-turbine gearboxes. The plant was chosen because it’s one of ZF’s newest and smallest facilities, making it easier to test the energy-reduction ideas.
One strategy applied at the facility was an innovative way to test the wind-turbine gearboxes. Connecting two of the massive devices allows them to be tested simultaneously, resulting in 75% energy reduction.
“We load one up and call it the test unit, and the other is the slave unit,” Biers says. “When the test unit is testing, it’s driving the other one in the opposite direction. Then we flip them around and one becomes the slave unit and the other the test unit.”
Other energy-reducing steps taken at the Gainesville plant include installing more efficient lighting and low-flow toilets and pumping heat back into the facility rather than letting it escape outside.
The initiatives have resulted in cost savings. For example, the low-flow toilets will save about $8,000 annually. However, the plant employs only 120 people, so Biers says when it’s applied to all of ZF’s 121 global facilities, some of which employ thousands, the savings will multiply.
“The low-flow toilets (water savings) are the equivalent of seven homes,” he says. “When you spread these numbers out (across multiple facilities) you’re talking millions of dollars.”
But it’s the contributions to the environment Biers touts as the energy-saving initiatives’ greatest benefit.
ZF is working with its Tier 2 and 3 suppliers, many of which don’t have the German supplier’s financial means, to put their own energy-saving initiatives into action.
Read more about:
ZFAbout the Author
You May Also Like