Something In Common
Automotive interiors giant Johnson Controls Inc. says about 80% of the seats it has produced for multiple auto makers over the past four years have a common bond: They all share the same guts. JCI's MS seat frame an acronym for Master Plan Structure is part of an industry-wide push by component makers to commonize parts whenever practical. JCI has been pushing its standardized seat frame for a number
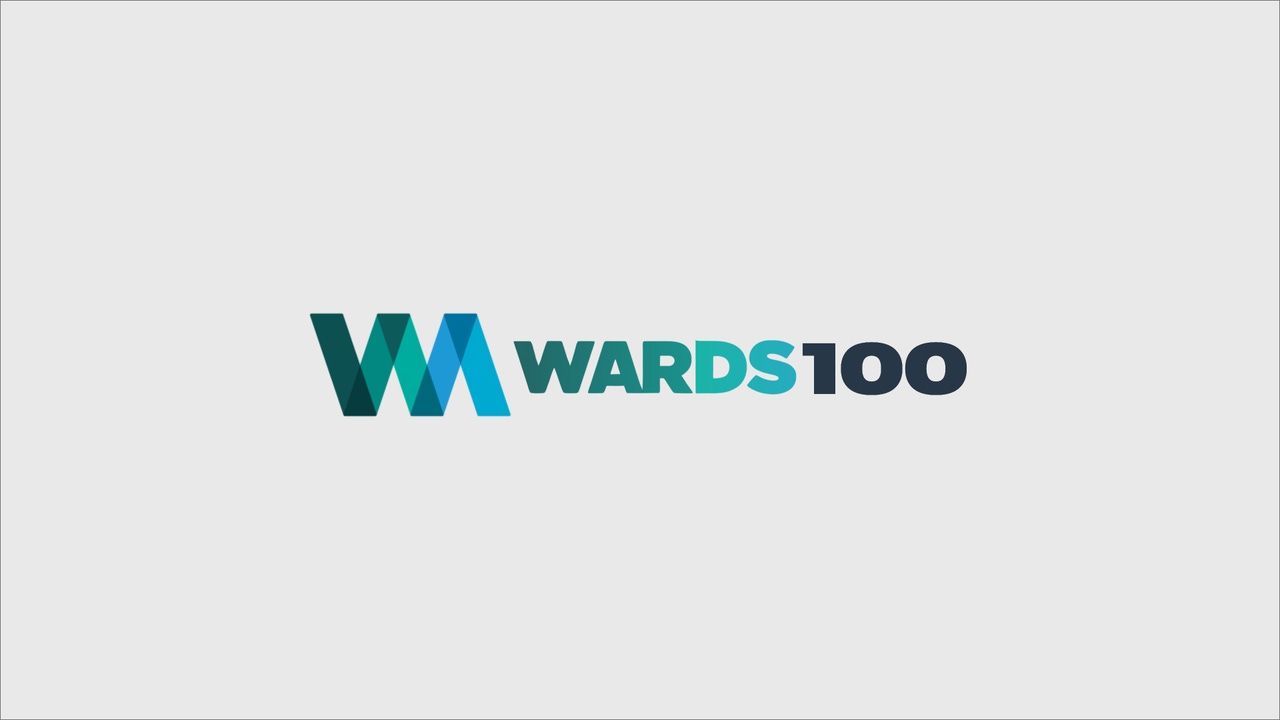
Automotive interiors giant Johnson Controls Inc. says about 80% of the seats it has produced for multiple auto makers over the past four years have a common bond: They all share the same guts.
JCI's MS seat frame — an acronym for Master Plan Structure — is part of an industry-wide push by component makers to commonize parts whenever practical.
JCI has been pushing its standardized seat frame for a number of years, and auto makers, constantly under pressure to cut costs and development time, apparently are jumping on board.
The supplier has contracts to apply its MS architecture to 28 vehicle programs with eight major auto makers. The programs will cover eight different vehicle segments and four regions of the world.
A standardized frame, however, does not mean all seats eventually will be the same. With the help of various grades of foam and fabric and a full range of kinematics in the finished product, JCI says seats always will be unique to a particular vehicle.
Since 1996, Chrysler Group products as disparate as the Dodge Neon, Jeep Wrangler and Dodge Viper have shared seat frame DNA.
Over the course of several years, JCI has produced some 2 million seats for Chrysler using the architecture.
Consumer research by JCI has found vehicle owners are just as happy with seats from the MS architecture as with other seats.
“In our comfort labs, we develop the actual ride and feel of the seat,” says Paul Lambert, group vice president-North America Seating. “Every one is unique as far as the consumer is concerned. It's only the seat structure itself that the consumer doesn't see where we've really commonized and leveraged the scale we have globally.”
JCI says a seat structure consists of several “no-change zones,” meaning engineers need only validate them once before applying them across a wide array of seating projects.
The zones include the back frame upper cross member joint, part of the rail, the recliner attachment and the manual latch. Some of the attachment points of the seat also can be commonized.
Lambert says new business in hand demonstrates the need for standardized seat frames.
“I would say 80% of the new business we are selling now provides the customer with the level of uniqueness but is built off a platform that gives them the benefit of the global scale, using the standard MS structure,” he says.
JCI also has won a light-truck seat program for '09 that will use the MS architecture, he says.
Potential cost savings are significant. JCI has reduced from 40 to 11 the number of tools necessary to build a seat frame in North America.
Shared tooling for the common architecture can generate up to 70% in cost savings, while fabrication costs can improve by as much as 40%, JCI insiders say.
About the Author
You May Also Like