Time TrialTime Trial
When the Ford GT goes into production next year, it will boast the industry's first interior constructed from Azdel SuperLite, project insiders say. The original Ford GT was a racecar, so J Mays Ford Motor Co. group vice president-design demanded the interior of its descendant reflect this heritage. And it had to be done in 12 months. Suddenly, engineers became harried pit-crew members. But instead
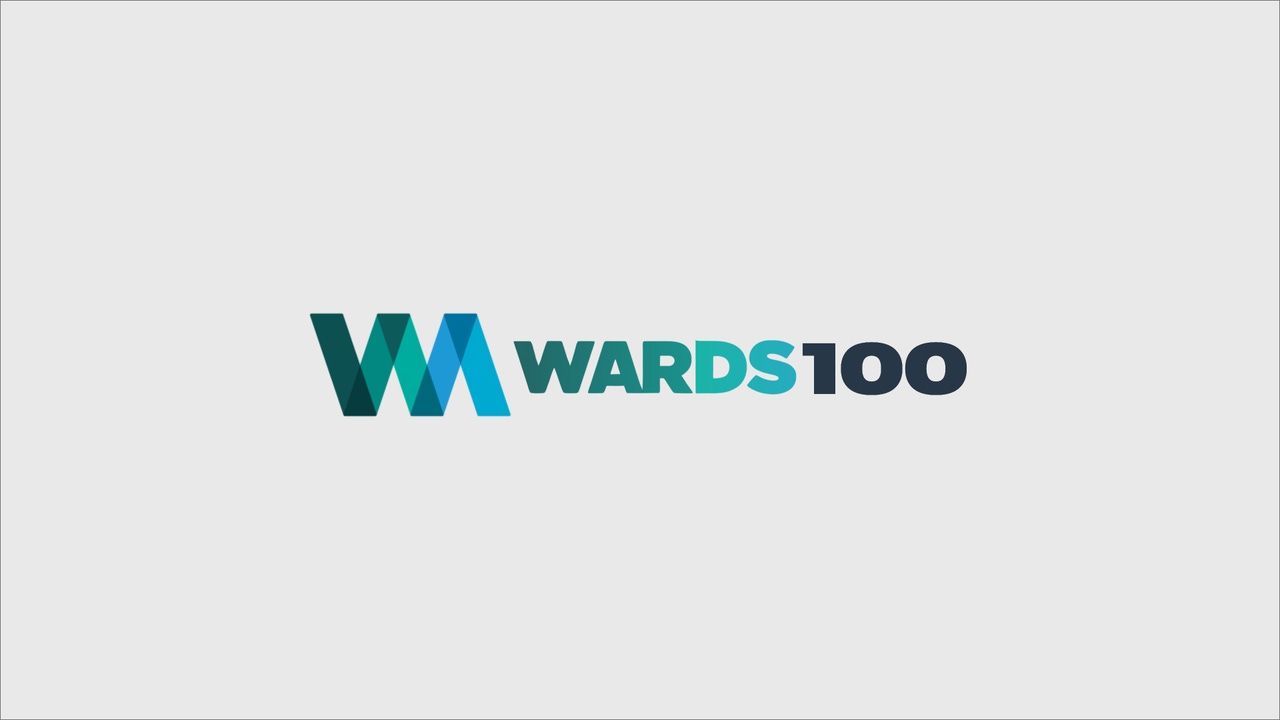
When the Ford GT goes into production next year, it will boast the industry's first interior constructed from Azdel SuperLite, project insiders say.
The original Ford GT was a racecar, so J Mays — Ford Motor Co. group vice president-design — demanded the interior of its descendant reflect this heritage. And it had to be done in 12 months.
Suddenly, engineers became harried pit-crew members. But instead of changing rubber and refueling, they had to bring the car to market.
The result? On-time delivery of an industry breakthrough.
Developed for headliners by GE Plastics, Azdel SuperLite forms the GT's door trim, pillar trim and “probably the lightest instrument panel in the world,” says Jim Masters, president-electrical systems division at Lear Corp., which designed and engineered the 2-seater's interior.
Compared to typical injection-molded trim parts, Azdel SuperLite — 55% glass fiber and 45% polypropylene and additives — afforded weight-reduction opportunities of 15% to 30%, Lear says.
In addition, the use of Renwood tooling — soft, but durable enough for low-volume programs — translated into a 70% cost reduction.
As with any race, however, there were numerous twists and turns en route to the finished product. Because Azdel SuperLite had no track record, Lear explored alternate solutions as a backup.
There was a contingency to use conventional tooling with wood fiber. Thermoplastic olefin (TPO) was considered instead of the vinyl substrate covering. (Vinyl proved more durable and attractive, prompting development of a unique technology for forming and application.)
And then there were the dynamics between project participants. The lines between supplier and OEM were “blurred,” says Masters, who is also Lear's executive champion for the Ford GT program.
“Decisions were made in real time. If there was a question on a supplier or part or design, they got together that minute and made a decision and moved forward.” Just like a racing team.
Says Ford's Bill Clarke, body engineering supervisor for the GT: “We never really had lengthy debates over things. There wasn't time. Lear came in with GE and both felt (Azdel SuperLite) was ready for a program like ours. We discussed it and felt that it was a risk worth taking. The savings (were) very attractive.”
Because of GT's low volume — Ford plans to build 4,500 total units in yearly increments of about 1,100 — Michigan-based WK Industries is handling Lear's production chores.
Ironically, there is no Azdel SuperLite in the GT's headliner — the material's originally intended use. In another first, Lear fashioned it from aluminum.
About the Author
You May Also Like