3D Printing Can Play Pivotal Role in Fueling EV Growth3D Printing Can Play Pivotal Role in Fueling EV Growth
The push toward going all-in on EVs creates a natural pivot point to leverage industrial 3D printing, also known as additive manufacturing.
April 6, 2021
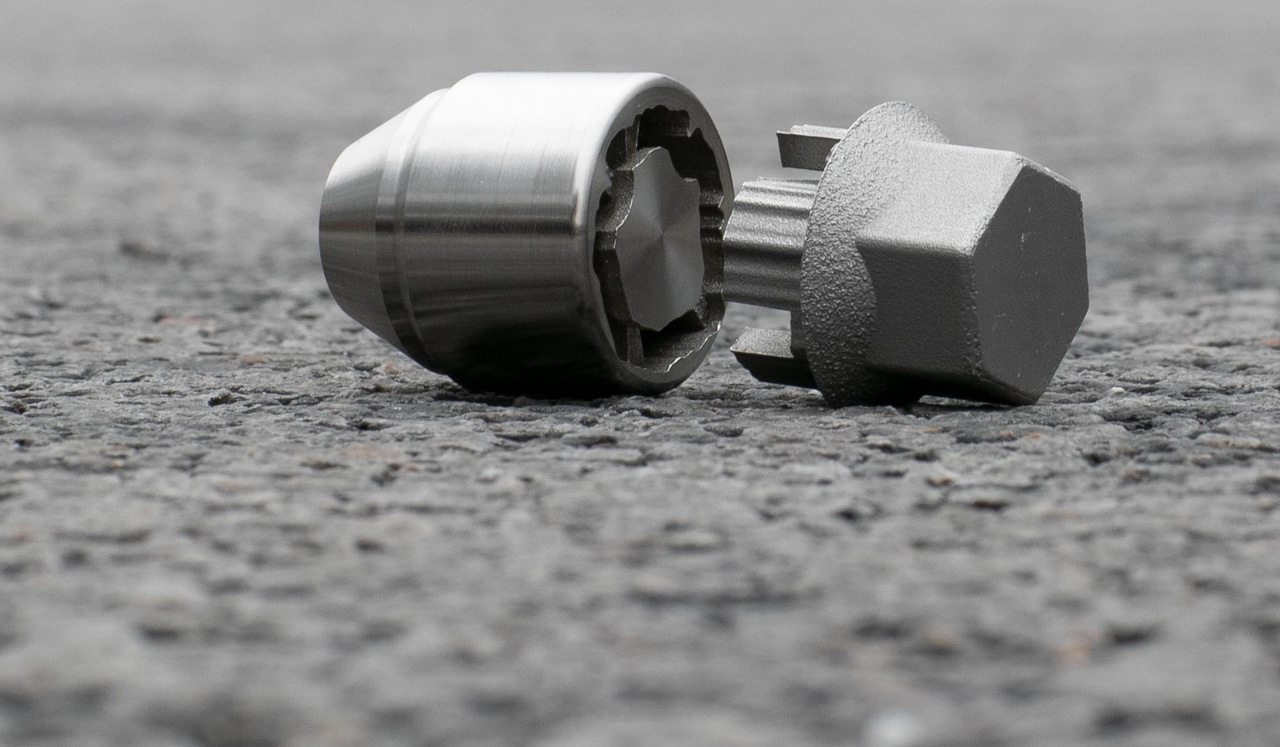
In the past year, we’ve seen a drastic shift across the automotive industry and among consumers with a growing appetite for electric vehicles.
General Motors, Ford and other OEMs have made recent announcements signaling they're pursuing EVs more heavily. President Biden signed an executive order requiring the replacement of the entire fleet of federal vehicles, about 645,000 cars, trucks, and vans, with U.S.-made electrics.
This push toward going all-in on EVs creates a natural pivot point to leverage industrial 3D printing, also known as additive manufacturing (AM). Here’s why:
EV battery life is affected by a variety of factors, including temperature and weight, and with so few charging stations and a lack of existing infrastructure to support widespread e-mobility, extending battery life, reducing weight and engineering wholly new designs are crucial to adopting electric vehicles en masse.
Industry-Voices-bug_30.jpg
As a completely digital and agile technology, AM is ideal for lightweighting. It allows for complex designs that deliver maximum performance not possible using traditional manufacturing methods.From a production perspective, it means designers and engineers can use smarter design geometries, eliminate tooling and fixture costs, and increase part durability and lifecycle, all while printing parts on-demand.
The growing number of materials for use in industrial 3D printing also plays a role in weight and improved thermal capabilities.
For example, AM makes it possible to replace metal with lighter plastic polymers, and you can even formulate custom materials with specific mechanical properties if required. Printing as a single component instead of several pieces welded together is another benefit, resulting in a stronger part requiring little or no assembly without sacrificing safety.
Ultimately, though, there’s still a gap in the industry between hitting cost-per-part targets and volume. The automotive supply chain has been in place for so long that conventionally manufactured parts are, down to the penny, as inexpensive as possible. But with EVs, there are new challenges and less established (or new) supply chains.
Integrating AM into this new era of EV production then becomes a numbers game – one that 3D printing tends to win.
Jon Walker EOS-Headshot
That’s because one of the biggest advantages of AM over traditional manufacturing methods, such as injection molding and casting, is its value in lower-demand scenarios. Molds and tooling by themselves traditionally drive breakeven production costs up, but with AM many of those costs are lowered or even eliminated.
Even with automakers shifting toward more EV-centric product portfolios, it’s not going to happen overnight.
There will be a rollout period as electric vehicles become more widely available (Edison Electric Institute predicts nearly triple the number of EV models will be available by 2023 compared to today), and this is where 3D printing can shine. Until OEMs are mass-producing EV parts, the cost equation typically favors additive manufacturing in such low volumes.
For an industry around for more than a century, keeping up with this high level of evolution is a huge undertaking. And just like EVs, additive manufacturing has, until recently, been underestimated. So, to stay at the forefront, now is the time to start integrating industrial 3D printing technologies into your production. If you wait, you're already behind the competition.
Ready to get started? See my October WardsAuto article about best practices for integrating industrial 3D printing.
Jon Walker (pictured above, left) is a business development manager for EOS, a leading provider of industrial 3D printing technologies and services.
About the Author
You May Also Like