Applying Pressure
Robert Bosch GmbH is developing a common-rail fuel-injection system for diesels that would achieve efficiency-enhancing pressures of around 36,200 psi (2,500 bar) or even 43,500 psi (3,000 bar), far higher than current-production, best-in-class 26,100-psi (1,800-bar) systems, or next-generation 29,000-psi (2,000-bar) systems. Stefan Kampmann, senior vice president of engineering for Bosch diesel systems,
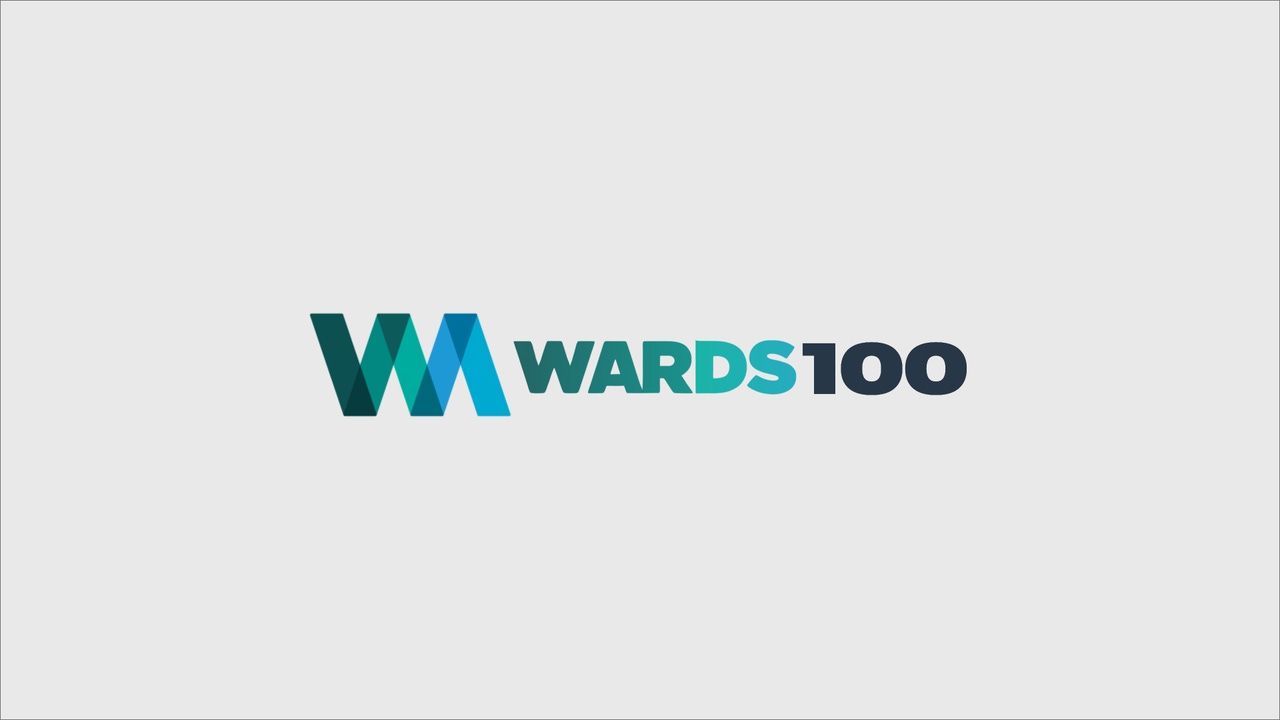
Robert Bosch GmbH is developing a common-rail fuel-injection system for diesels that would achieve efficiency-enhancing pressures of around 36,200 psi (2,500 bar) or even 43,500 psi (3,000 bar), far higher than current-production, best-in-class 26,100-psi (1,800-bar) systems, or next-generation 29,000-psi (2,000-bar) systems.
Stefan Kampmann, senior vice president of engineering for Bosch diesel systems, says the program for HADI, or Hydraulically Assisted Diesel Injection, still is in advanced development.
Higher pressure results in more control of the combustion process. Engineers can use the higher pressure to reduce emissions or improve fuel economy.
In Bosch's third-generation common-rail systems with piezoelectronic injectors (starting production later this year), the 1,800-bar system delivers 3.7 times less engine-out particulate matter and oxides of nitrogen (NOx) than the 23,200-psi (1,600-bar) system that has been in production since 2003.
The Bosch 2,000-bar common-rail fueling system going into production in late 2007 has 4.5 times less emissions than the 1,600-bar system.
Pressures of 2,000 bar generally are considered to be at the limit of what steel fuel rails and other components can safely contain. Kampmann says the 2,500-bar HADI will use high-strength steel, as well as a new injector design that will allow the pressure to be boosted inside the injector.
In the unit-injector system that Bosch has been making for Volkswagen AG, it achieves pressures of up to 31,900 psi (2,200 bar). Rather than using a fuel pump that supplies pressurized fuel to the common rail that feeds each cylinder's injector, the VW system employs camshaft-driven pumps that are integral with each injector.
Kampmann says the ultra-high-pressure HADI system, in which the pressure is amplified within the injector (which still is fed by a common rail), may well be needed to meet future emissions regulations. The big question is, “what kind of quality and cost level we can achieve.”
The 2,000-bar system with piezo injectors will be needed in larger passenger cars to meet 2007 U.S. emission regulations and the probable Euro 5 emissions regulations.
Diesel exhaust already has been considerably cleaned up in Europe by the common-rail injection systems Bosch pioneered in 1997, but future regulations will be more severe.
DaimlerChrysler AG CEO Dieter Zetsche spent half his press conference at January's Detroit auto show talking about DC's BlueTec diesel aftertreatment system, which he expects will meet the toughest current U.S. emissions regulations in all 50 states.
Zetsche described a mix of better engine control and aftertreatment that will provide clean exhaust and deliver 25 mpg (9.4 L/100 km) in a Jeep Grand Cherokee.
Bosch is one of DaimlerChrysler's development partners for BlueTec, working on both engine-out emissions and aftertreatment. Excessive NOx now is the main problem with diesel exhaust, as existing particulate filters can meet all anticipated regulations for particulate matter (PM).
Bosch engineers are developing NOx traps, or storage catalysts, that would use precious metals to reduce the NOx to harmless components, and selective catalytic reduction (SCR) systems that inject urea and water into a second catalyst in the exhaust stream.
With SCR, the urea becomes ammonia and continuously reduces NOx into nitrogen, water and carbon dioxide (CO2). The German auto industry uses the word “blue” for urea. Where DC talks of “BlueTec,” Bosch uses the phrase “ad blue” to mean urea-added.
Dirk Naber, director of the diesel systems test laboratory at Bosch's Stuttgart headquarters, says the urea systems almost certainly will be the solution for heavy trucks, as too much precious metal would be required in a NOx trap. For passenger cars, he says, the economics are closer.
The urea approach has the advantage of being robust and providing continuous treatment for the life of the vehicle. Current Bosch testing is reducing NOx by 50% to 70%, and engineers expect to reach 60% to 90% NOx reductions.
The system works as long as the urea tank is not depleted or the urea is not frozen, which occurs at temperatures below about 12° F (-11° C). The NOx trap approach suffers from aging problems because the catalyst is subjected to periodic flamethrower-like blasts of 1,200° F (650° C).
With SCR systems, there is concern about urea tanks running dry, but Kampmann suggests the urea supply can be replenished during routine maintenance so the vehicle owner never is responsible for dealing with the system.
Another future idea is to have double nozzles at diesel filling stations, one delivering fuel and the other enough urea to treat that fuel.
DaimlerChrysler is examining both NOx traps and SCR to meet the goal of being clean enough for diesel sales in all 50 states. When the time comes, says Kampmann, their engineers “will have to make a business decision on which way they would go.”
Bosch repeats Zetsche's assertion at the North American International Auto Show that if 40% of U.S. vehicles were powered by diesels — a proportion similar to new-vehicle penetration rates in Western Europe — the U.S. could entirely eliminate oil imports from Saudi Arabia.
Bosch says based on current tax policies that have diesel and gasoline priced about the same, the U.S. economy would save $9 billion annually and CO2 production would be reduced by 15% to 20%.
Diesel fuel has about 22% more energy content than gasoline, which gives it a natural advantage in terms of fuel economy and range. Besides improved mileage, Bosch counts on the high torque of modern diesels and their towing power to win over Americans. “The size of the boat you can pull out of the water” will convince buyers of SUVs and large cars that a diesel is a good choice, he says.
Bosch forecasts diesels will power 27% of the 67 million vehicles produced worldwide this year, 29% of 75 million in 2010 and 31% of 79 million in 2014.
For North America, Bosch predicts diesels will account for 10% to 15% of production by 2014.
Selling diesels in Japan will be tougher, says Kampmann. The Japanese driving conditions of low speeds and lots of idle time do not play to diesel's strength, while the disadvantage of engine noise is more pronounced.
Kampmann says Bosch is working on strategies to meet Japanese auto makers' request “that a diesel in idle is as quiet and smooth as a big gasoline engine.”
Bosch also is working on cost. A diesel system in Europe generally costs about $1,200 more than a gasoline engine of similar performance. “Our customers need to make a profit,” says Kampmann. “We must not make a diesel powertrain too expensive for the main market.”
To cut costs, part of Bosch's strategy is to produce some components in low-cost countries.
About the Author
You May Also Like