Behr Developing Cooling Solutions for Electric, Conventional Engines
The supplier’s cooling technology can be found in the Chevrolet Volt extended-range electric vehicle, Mercedes S400 HEV and Ford Fusion HEV.
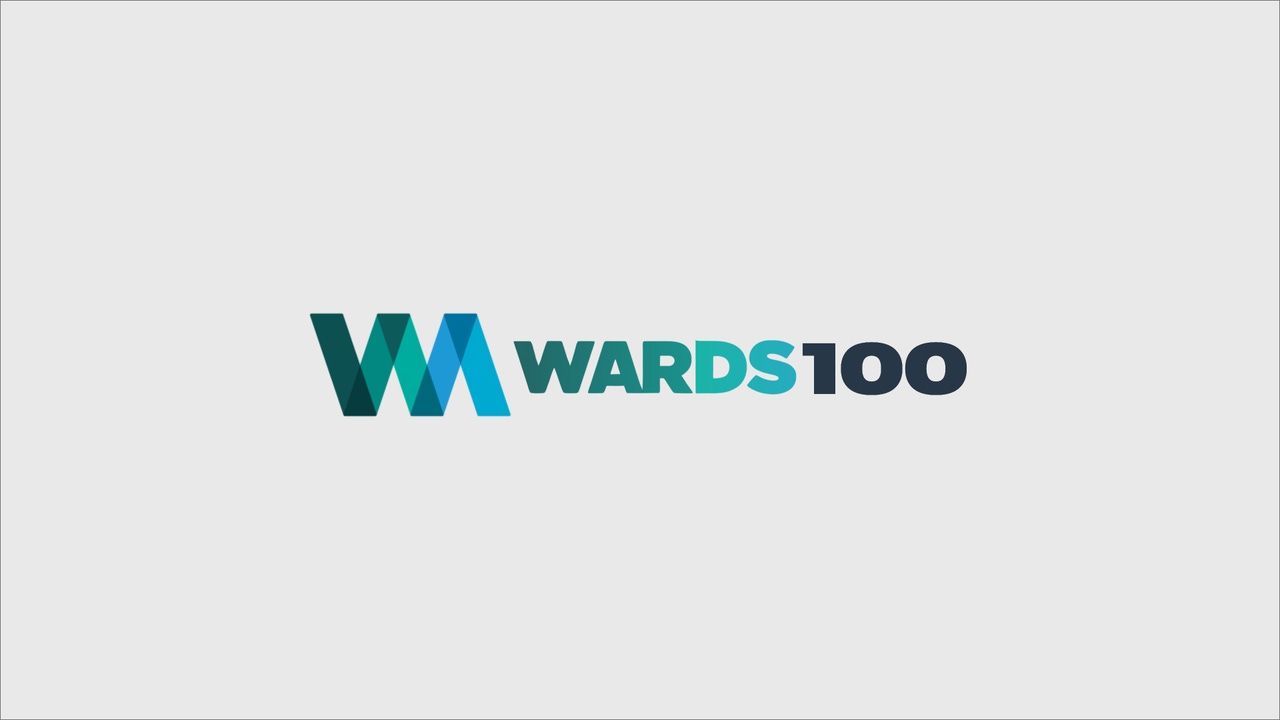
Special Coverage
SAE World Congress

DETROIT – Behr America is seeing increased demand for its line of cooling systems from global auto makers striving to increase the fuel efficiency of their vehicles, a company executive says.
Business has increased exponentially, but the most dramatic increase is being driven by North American-based OEMs, Uwe Krueger, vice president-engineering, tells Ward’s at the 2011 SAE World Congress here.
Applications include vehicles powered by conventional internal-combustion engines, as well as hybrid- and pure-electric vehicles, Krueger says.
Hybrids and EVs “are an important part of future mobility,” and the biggest challenge is the “thermal stability of the battery.”
Advanced lithium-ion batteries have to be kept at a precise temperature to optimize performance. Any degradation can lead to instability and reduce the efficiency of a battery, and in the case of EVs, the vehicle’s range.
Behr has partnered with the world’s top battery suppliers to develop its line of cooling systems, currently found in the Chevrolet Volt extended-range EV, Mercedes S400 HEV and Ford Fusion HEV, Krueger says.
“What we’re doing is using our refrigerant and HVAC technology to cool the battery in every condition, especially under hot conditions. “You can’t just use a radiator. You need a coolant.”
Behr offers unique solutions that depend on the configuration of the battery pack, Krueger says. In packs where the cells are flat, the supplier has developed a system of cooled plates that are positioned between each cell, drawing heat away.
Thermal stability of battery biggest challenge for hybrids and EVs, says Behr’s Uwe Krueger.
In the case of the Mercedes S400, which uses cylindrical cells, Behr developed cooled “pins” that cradle the cells to maintain the proper temperature.
Krueger admits other suppliers offer similar solutions but says Behr’s systems are more energy-efficient and smaller, making it easier to fit them into the vehicle.
Behr also has seen increased demand for its cooling technology for downsized internal-combustion engines. In an effort to offer smaller, fuel-efficient mills without sacrificing performance, auto makers such as Ford have turned to turbochargers or superchargers.
“Charging engines is good because it gets more compressed air into the combustion chamber, but the compression and charging of the air heats it up, and that’s bad,” Krueger says.
Heated air produced by compression leads to turbo lag, which causes a brief delay of full power once the accelerator is depressed.
To mitigate the problem, Behr has developed a cooling system that is positioned closer to the turbocharger or supercharger. In previous systems, the cooling system was located further away from the charger, which meant heated air had to travel a long way before being cooled, leading to lag.
Krueger says Behr perfected the technology through its business in Europe, where it offers a line of cooling solutions for charged diesel engines.
Read more about:
2011About the Author
You May Also Like