Comau Sells Smart Assembly
Comau’s SmartCell allows one sophisticated and highly flexible machine to replace an entire transfer line of about a dozen machines dedicated to powertrain assembly.
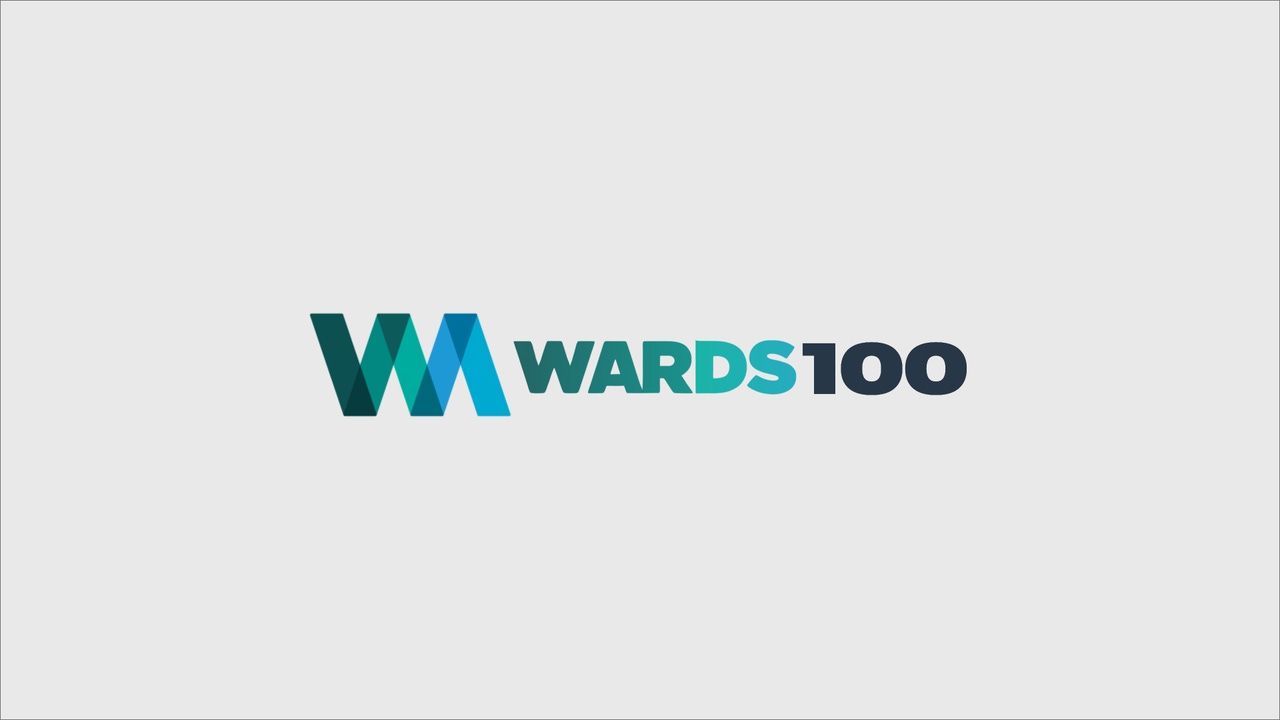
With assembly plants closing and auto makers looking to redeploy machines and assets, executives at Comau Inc. say there’s never been a better time to overhaul the manufacturing paradigm.
Wholly owned by Fiat Group, Comau is a leader in the field of industrial automation, applying the latest technology to advanced manufacturing systems in the constant quest for lower piece price, greater efficiency and lower capital investment. Operating in 17 countries, Comau has 11,000 employees worldwide, including 1,100 in North America.
Its latest development is the “SmartCell,” which enables for assembly operations the same type of sea change that accompanied computer-numeric-controlled machines for metal cutting some two decades ago.
Today, assembling a cylinder head requires a transfer line, a series of machines each dedicated to a particular procedure or task. In the traditional configuration, between nine and a dozen machines are necessary to assemble the pieces of the valvetrain, says Ted Brown, Comau’s vice president and general manager-powertrain.
A valvetrain is a complicated piece of machinery that operates under extreme conditions at high speed, allowing an engine to breathe.
But the assembly and installation of 72 parts in one case study is slow and laborious. The cylinder head moves from machine to machine via pallet and conveyor and is rotated as seals, springs, valves, retainers and other hardware are installed from above and below the head unit.
Cycle time for each machine in the transfer line is between 25 and 30 seconds, which translates into several minutes and significant capital investment to produce one valvetrain.
Perkins Engine first customer for Comau’s SmartCell.
Comau’s SmartCell allows one sophisticated machine to replace the entire line, while completing the assembly procedure with four operations in a mere 54 seconds.
Operations are combined in the single station with manual or automated kitting operations feeding the assembly cell until the process is complete. The part can be transferred in and out of the SmartCell by gantry, robotically or manually.
“From a lean-manufacturing standpoint, it’s all about work-in-process,” Brown says. “Imagine those nine machines – all are going to need parts in-process as well as on-deck. That’s a minimum of 18 parts in-process that are not value-added. You have pallets and conveyors, all non-value-added.”
By comparison, the SmartCell has just one part in-process, perhaps one on-deck. “So from a lean-manufacturing standpoint, it’s not even a comparison,” he says. “It’s so far advanced from that perspective that it’s almost unmeasurable.”
The impact on floor space is tremendous. Traditional assembly of 325,000 cylinder heads annually requires about 8,100 sq.-ft. (753 sq.-m). Comau says the SmartCell can do the same job with a mere 2,400 sq.-ft. (223 sq.-m) of space.
Comau says the Smart Cell is ideal for automated assembly of other components requiring tight tolerances, such as turbochargers, engine sub-assemblies, transmissions, differentials and power take-off units.
Perhaps the most important benefit to the Smart Cell is added flexibility that allows the machine to be reconfigured quickly to produce something else.
In today’s volatile market, it’s not far-fetched to imagine an auto maker wrestling with a decision to retool its assembly lines to build more 4-cyl. and fewer V-8 engines.
“Presently with the serial process, it would take roughly six months of preparation time and three months to tear that system down and reconfigure it for a transfer line with conveyor and pallets,” Brown says.
“That’s a minimum of nine months to do that, and they lose three months of production. It’s a big deal, and every assembly line that builds cylinder heads in the world has that problem.”
It’s a problem that faces the domestic U.S. auto makers as well as the most efficient transplants, not only with regard to cylinder heads.
“It’s every assembly process they do: engine assembly, transmission assembly, all the subcomponent assembly,” he says.
Comau says the SmartCell will allow customers to switch out the old tools for new ones and change the programming at a moment’s notice. “Now this machine can assemble a completely different part over a weekend,” Brown says. “You’re ready to assemble a different part, a different cylinder head or maybe a transmission.”
Comau’s first customer for the SmartCell is Perkins Engine, which will use the system for cylinder-head output in the U.K., beginning in January. Perkins is purchasing two cells – one to produce valvetrains for 6-cyl. diesels, the other to make valvetrains for 4-cyl. diesels, Brown says.
In a letter to Comau this past summer, a Perkins executive says the SmartCell will allow valvetrain assembly in a quarter of the space usually required and at a third of the cost. Perkins considers SmartCell the “low-risk, high-gain route.”
In an apples-to-apples comparison, occasionally the cost savings are not significant, depending on the level of automation.
Comau also is in talks with Ford Motor Co. about the system. Brown says the SmartCell should be just as attractive to domestic OEMs in downsizing mode as to transplants eager to expand their manufacturing footprint.
Constructing an assembly line requires a production model with a theoretical market to achieve certain volumes within, say, five years to justify capital investment.
“With this parallel processing, they only have to invest in the market they have in the short term,” Brown says. “They’re only tying up their cashflow based on real market demand. In our industry, we’ve never had that flexibility before.”
Auto makers recently emerging from bankruptcy – or trying to stay out of bankruptcy – could find Comau’s new machine a smart buy.
About the Author
You May Also Like