FEV Concepts Advance Engine Downsizing, FlexibilityFEV Concepts Advance Engine Downsizing, Flexibility
The engineering firm’s Spray Guided Turbo engine and variable-compression assembly showcase what might result as auto makers boost R&D spending to improve vehicle efficiency.
April 23, 2008
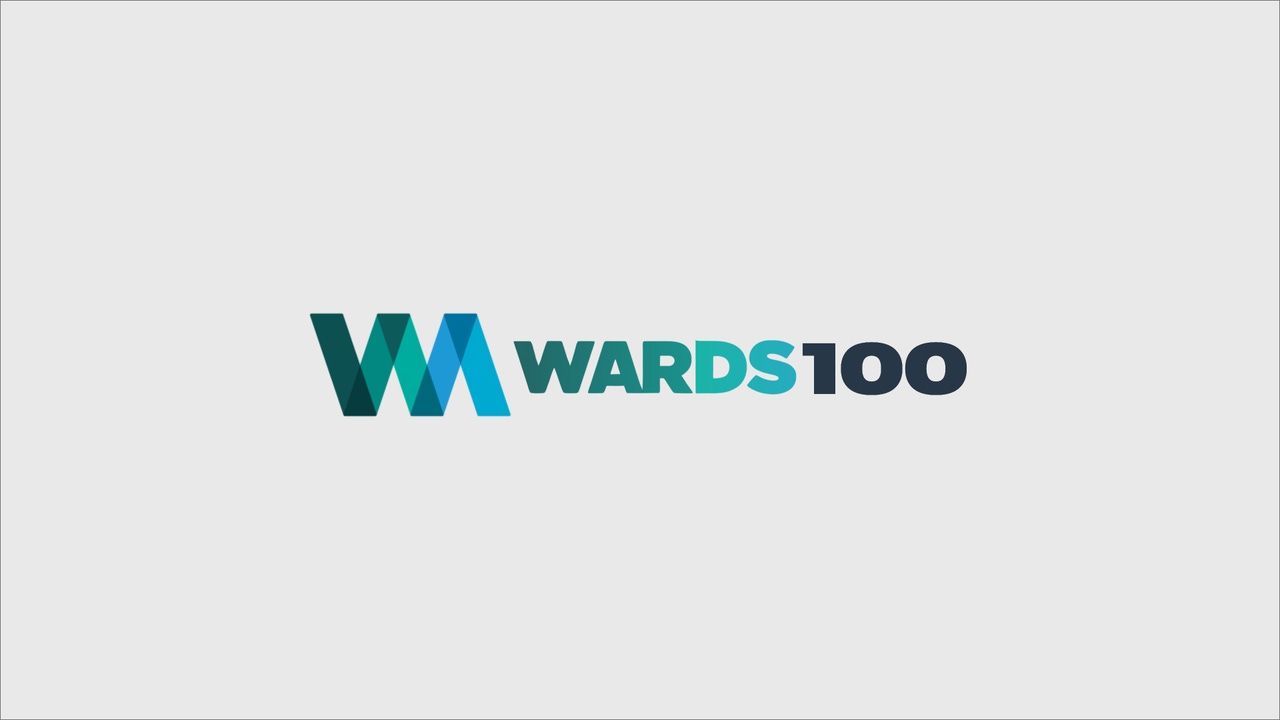
Special Coverage
SAE World Congress

As satisfying upcoming fuel economy and emissions regulations will require the internal-combustion engine to be fitted with numerous advanced technologies, FEV Inc. is offering a glimpse of what light- and heavy-duty powertrains might look like in the near future.
On display at last week’s SAE World Congress in Detroit, the concepts are part of the engineering firm’s internal development to showcase what the likely result will be from auto makers boosting their research and development spending to improve fuel efficiency without sacrificing performance.
For passenger cars and other light-duty vehicles, downsized engines such as FEV’s 1.8L Spray Guided Turbo 4-cyl. appear a must.
Two-stage variable-compression-ratio mechanism contained within connecting rod assembly.
Based on an existing production block, the rest of the powerplant was designed from the ground up to optimize the benefits of gasoline direct injection (GDI), turbocharging and a raft of complementary systems, says Jochem Wolschendorf, chief technical officer and vice president-vehicle systems.
The SGT engine uses lean-burn stratified combustion vs. conventional stoichiometric operation to achieve diesel-like fuel economy in a compact package aimed at replacing larger gasoline engines, such as a 3.0L V-6.
Output is 215 hp and 236 lb.-ft. (320 Nm) of torque, accompanied by a broad powerband characteristic of GDI/turbo engines.
Fuel consumption is 8%-10% less than existing GDI/turbo engines, with a carbon-dioxide output near 130 g/km in the European test cycle, FEV says. It also is flex-fuel compatible, capable of Super-Ultra-Low Emissions Vehicle status in the U.S. and easily can be configured for use with hybrid-electric drivetrains.
What makes the SGT unique is its built-in electronic tunability, as well as the flexibility to be scaled either up or down in size.
For optimum combustion, piezo-electric fuel injectors are centrally located in the cylinders next to the spark plug vs. a more conventional position in the side of the combustion chamber. This combination, yet to be seen on production engines, allows for the more efficient ignition of fuel, along with the ability to fine tune the burn with multiple and/or delayed injections.
Intake and exhaust camshaft phasers and external exhaust-gas recirculation are present for improved efficiency, while the standard wastegate turbocharger recoups lost energy exiting the engine.
The addition of a more advanced dual-stage and/or variable-geometry turbocharger (VGT) setup, similar to diesel engines, is possible, Wolschendorf says, but was not fitted to the SGT due mainly to excessive costs associated with expensive heat-resistant materials used in VGT components.
Although the SGT engine emits far less hydrocarbons and particulate matter than a diesel mill, Wolschendorf adds, the catch with the lean-burn combustion is the increased production of oxides of nitrogen.
NOx levels still are less than those from diesel engines, but reducing this pollutant will require use of expensive, exhaust-aftertreatment technology, such as a NOx absorber or catalyst.
Medium- and heavy-duty vehicles with large diesel engines face similar challenges. However, their size and work cycle make broad redesigns prohibitively expensive and hard to implement.
FEV addresses this issue with a simplified, 2-stage version of its variable-compression-ratio (VCR) technology designed for large diesel engines.
Similar in theory to the company’s continuous VCR concept, the new mechanism allows the compression ratio to be mechanically varied (from 14:1 to 17:1) depending on engine load for improved fuel economy and reduced emissions.
The difference between the two technologies is the 2-stage system is contained entirely in the cylinder’s connecting-rod assembly vs. the continuous version’s more complex mechanism that varies the position of the whole crankshaft.
The advantage is 80% of the continuous VCR’s benefits at a much lower cost, Wolschendorf says, noting diesel engines don’t always need their compression ratios varied wildly, and packaging and durability of the continuous system become issues when scaled up for large diesels.
Helping with the 2-stage VCR’s simplicity is the use of conventional pistons and piston pins. The variability is focused within the con-rod, which suspends the piston with an eccentric gear that can be hydraulically actuated via a small electric motor.
Activating the eccentric gear effectively moves the piston up or down in relation to the centerline of the crankshaft. The only other modifications required are for accommodation of the extra electro-hydraulic components and the related electronic controls.
Along with improved efficiency, FEV says the 2-stage VCR can support higher turbo-boost pressures without exceeding the mechanical limits of the engine, as well as offer improved cold starting, long a problem with large diesels.
Despite the harsh environment inside an engine’s cylinder and the violent forces con-rods must endure, Wolschendorf says the new system has completed its internal durability testing.
“It’s essentially a concept that’s been fully tested,” he says, adding production validation is all that remains because customers have yet to sign up.
The 2-stage VCR also offers the benefit of being a scalable design, able to operate in a 15.0L Class 8 heavy-truck engine, as well as small-displacement gasoline mills for passenger cars.
However, the bulk of the VCR con-rod adds significantly to the reciprocating mass of a gasoline engine, sapping efficiency and hurting its ability to rev. As diesel engines are inherently robust in their construction, the added weight has a much lesser effect, Wolschendorf says.
In addition to the SGT and VCR concepts, FEV also presents a conventional overhead-camshaft diesel cylinder head design featuring an optimized valvetrain that reduces overall height up to 0.6 in. (15 mm).
By reconfiguring the traditional valve guides and actuation components, a shorter and less-expensive valve can be used, says Derek B. Woodcroft, program manager-engine design.
Valve-stem forces, lubrication needs and final machining are reduced, as well, he adds, with the head also benefiting from increased stiffness compared with conventional designs.
Other benefits of a shorter cylinder head include a narrower angle between cylinder banks for improved packaging, particularly for front-wheel-drive vehicles with transverse-mounted engines, along with greater hood-to-engine clearance for softer impacts in the event of a pedestrian collision.
About the Author
You May Also Like