Ford Reopens Cleveland Engine Facility for EcoBoost Output
To maintain quality, the plant features a new internal database that tracks the “birth history” of each engine, allowing engineers to follow every stage in the production process.
February 27, 2009
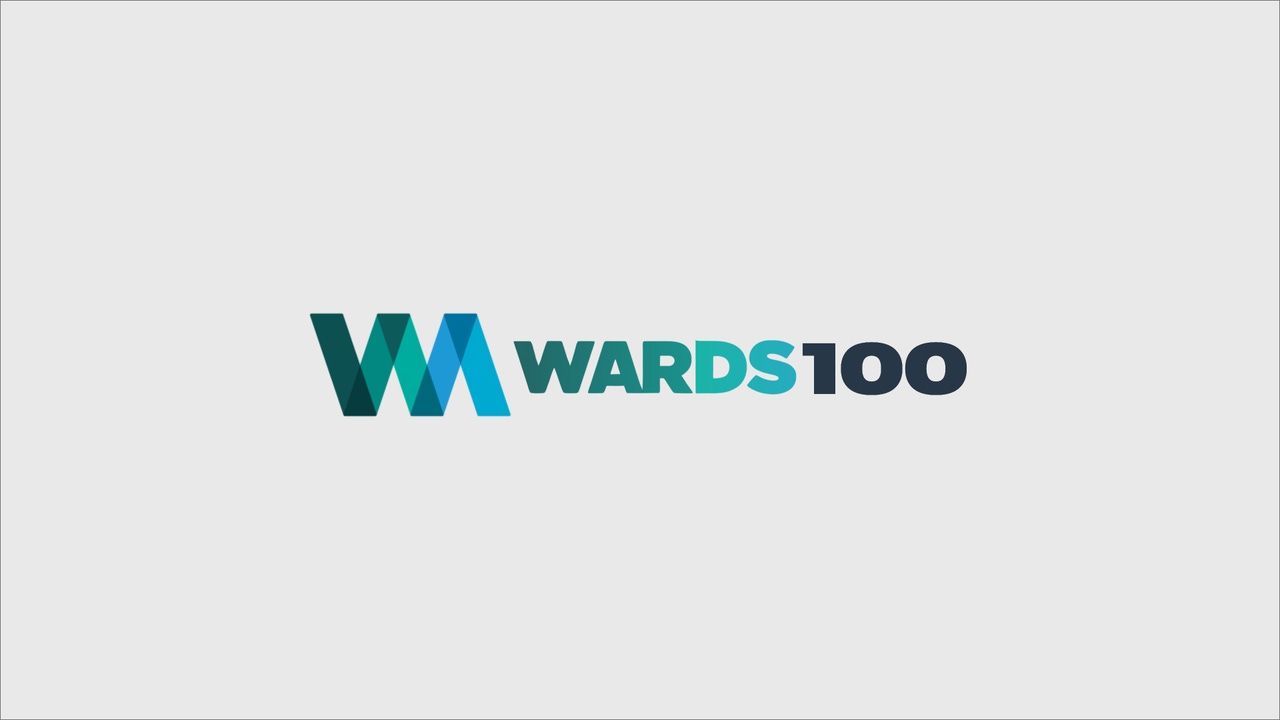
Ford Motor Co. is set to reawaken its historic Cleveland Engine Plant No.1 to build its new line of turbocharged, direct-injection EcoBoost engines.
The facility began churning out the auto maker’s iconic “302” and 5.0L V-8 mills in 1951. At the time of its closure in May 2007, the plant was building 3.0L engines and employed 577 workers. Production of the 3.0L engines subsequently was transferred to Ford’s Lima, OH, engine plant.
Located in Brook Park, OH, a southern suburb of Cleveland, the facility is set to begin volume production of 3.5L V-6 EcoBoost engines this spring. The EcoBoost mill makes 355 hp and 350 lb.-ft. (475 Nm) of torque and will be optional on the ’10 Lincoln MKS sedan, Lincoln MKT cross/utility vehicle and the Ford Flex CUV. It will come standard on the upcoming ’10 Taurus SHO.
EcoBoost engines are able to achieve 20% better fuel economy and 15% lower carbon-dioxide emissions compared with larger displacement engines without sacrificing power, Ford says.
By 2013, more than 90% of Ford’s North American lineup will be available with EcoBoost technology, and the auto maker plans to add a 4-cyl. variant to the range in the near future.
“The launch of EcoBoost is the big milestone in Ford’s commitment to deliver affordable fuel-efficient cars and trucks to millions of customers,” says Barb Samardzich, vice president-powertrain product development.
In preparation for EcoBoost output, Ford invested $55 million for tooling and equipment to create a flexible manufacturing process. The modern tooling easily can be reconfigured and reprogrammed to perform new tasks, says Jan Allman, Cleveland site manager.
“One of the main benefits of this system is its flexibility,” he says. “This system allows us to make changes within the plant without disrupting production. This is a complete change from the old way of doing things.”
To maintain quality, the plant features a new internal database that tracks the “birth history” of each engine, allowing engineers to follow every stage in the production process.
The engine history, maintained in a microchip database, includes hundreds of metrics and allows engineers to trace the precise path taken by any given part so that quality-control issues can be tracked to their source.
About 250 employees will comprise one shift to build the engine. Volume projections for the engine have yet to be announced.
Read more about:
2009About the Author
You May Also Like